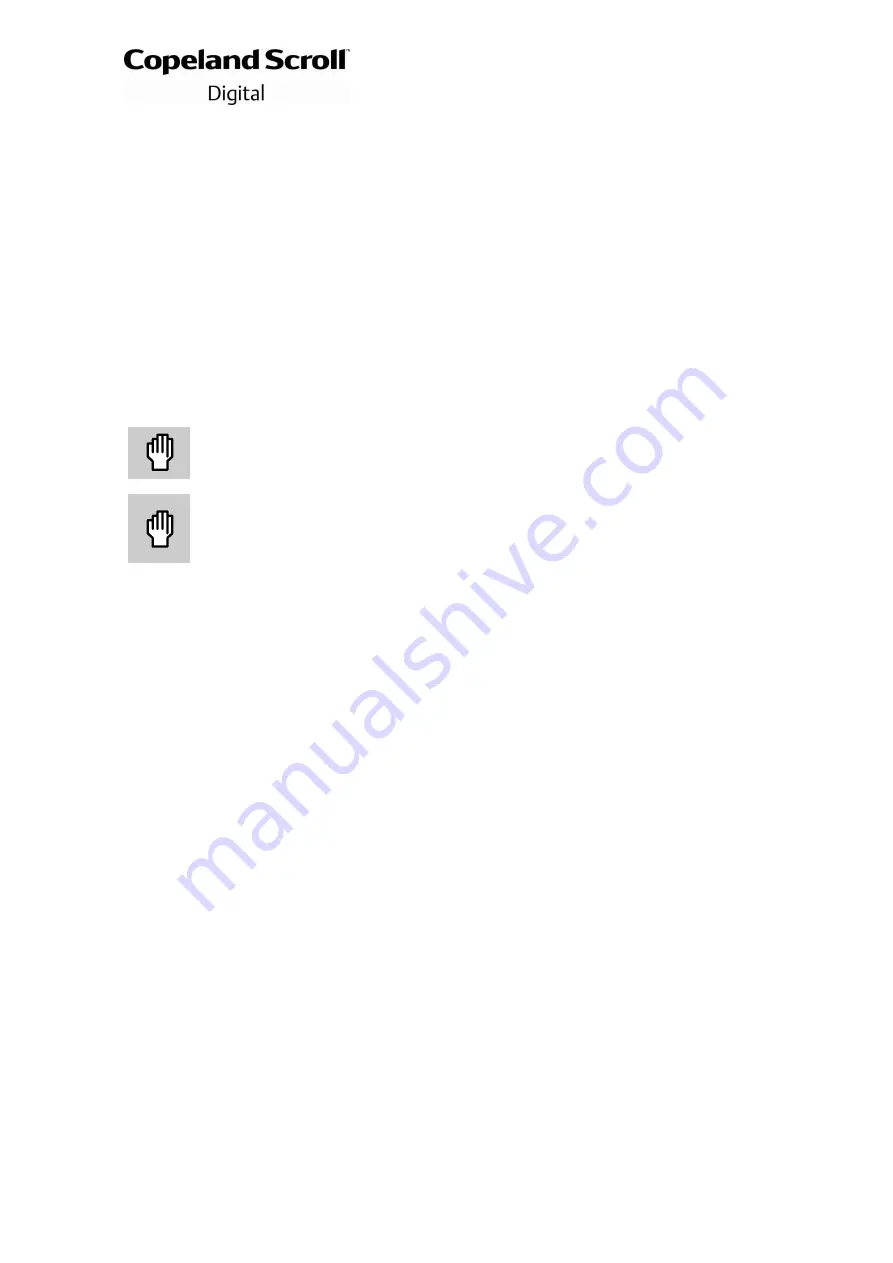
22
C6.2.44/0219/E
5.8 Pressure fluctuations
During the normal operation of the Digital Scroll compressor, there is a fluctuation in the suction
and discharge pressures. This fluctuation will be in the range of 2 to 3.5 bar. During the unloaded
state, the discharge pressure will start to drop and the suction pressure will start to rise. This is
normal. This pressure fluctuation has no effect on the reliability of any system component.
NOTE: All ZRD*KRE compressors require a minimum 3.5 bar differential between the
suction pressure and the discharge pressure to unload properly.
5.9 Starting sound
During the very brief start-up, a clicking sound is audible, resulting from initial contacting of the
spirals and is normal. Due to the design of the Copeland scroll compressors, the internal
compression components always start unloaded even if system pressures are not balanced. In
addition, since internal compressor pressures are always balanced at start-up, low-voltage starting
characteristics are excellent for Copeland scroll compressors.
5.10 Deep
vacuum
operation
CAUTION
Vacuum operation! Compressor damage!
Scroll compressors should never
be used to evacuate a refrigeration or air-conditioning system.
CAUTION
Vacuum operation! Bearing damage!
Vacuum operation causes damage to
the drive bearing of the scrolls. Copeland Scroll compressors are able to pull
vacuum very quickly and this should be avoided.
The scroll compressor can be used to pump down refrigerant in a unit as long as the pressures
remain within the operating envelope. Prolonged operation at low suction pressures will result in
overheating of the scrolls and permanent damage to the compressor drive bearing. ZRD scrolls
incorporate internal low vacuum protection; the floating seal unloads when the pressure ratio
exceeds approximately 10:1.
5.11 Shell
temperature
The top shell and discharge line can briefly but repeatedly reach temperatures above 177°C if the
compressor cycles on its internal protection devices. This only happens under rare circumstances
and can be caused by the failure of system components such as the condenser or evaporator fan
or loss of charge and depends upon the type of expansion control. Care must be taken to ensure
that wiring or other materials that could be damaged by these temperatures do not come in contact
with the shell.
5.12 Pump-down cycle
To control refrigerant migration a pump-down system could be used. The discharge check valve
with a refrigeration scroll compressor is designed for low leak back and will allow the use of a
pump-down without the addition of an external check valve.
If the compressor is stationary for prolonged periods, refrigerant could migrate into the compressor
and therefore a crankcase heater must be installed.
If cold air is constantly drawn over the compressor this could make the crankcase heater
ineffective and therefore a pump-down system is recommended.
For ZRD*KRE models care should be taken because the scroll sets will unload at a pressure ratio
of approximately 10:1. If the unit fails to pump down the pump-down pressure should be reset to
a higher value. The low-pressure control differential for all models needs to be reviewed since a
relatively lower volume of gas will re-expand from the discharge plenum of the compressor into
the low side on shutdown.
5.13 Minimum run time
Emerson recommends a maximum of 10 starts per hour. There is no minimum off time because
scroll compressors start unloaded even if the system has unbalanced pressures. The most critical