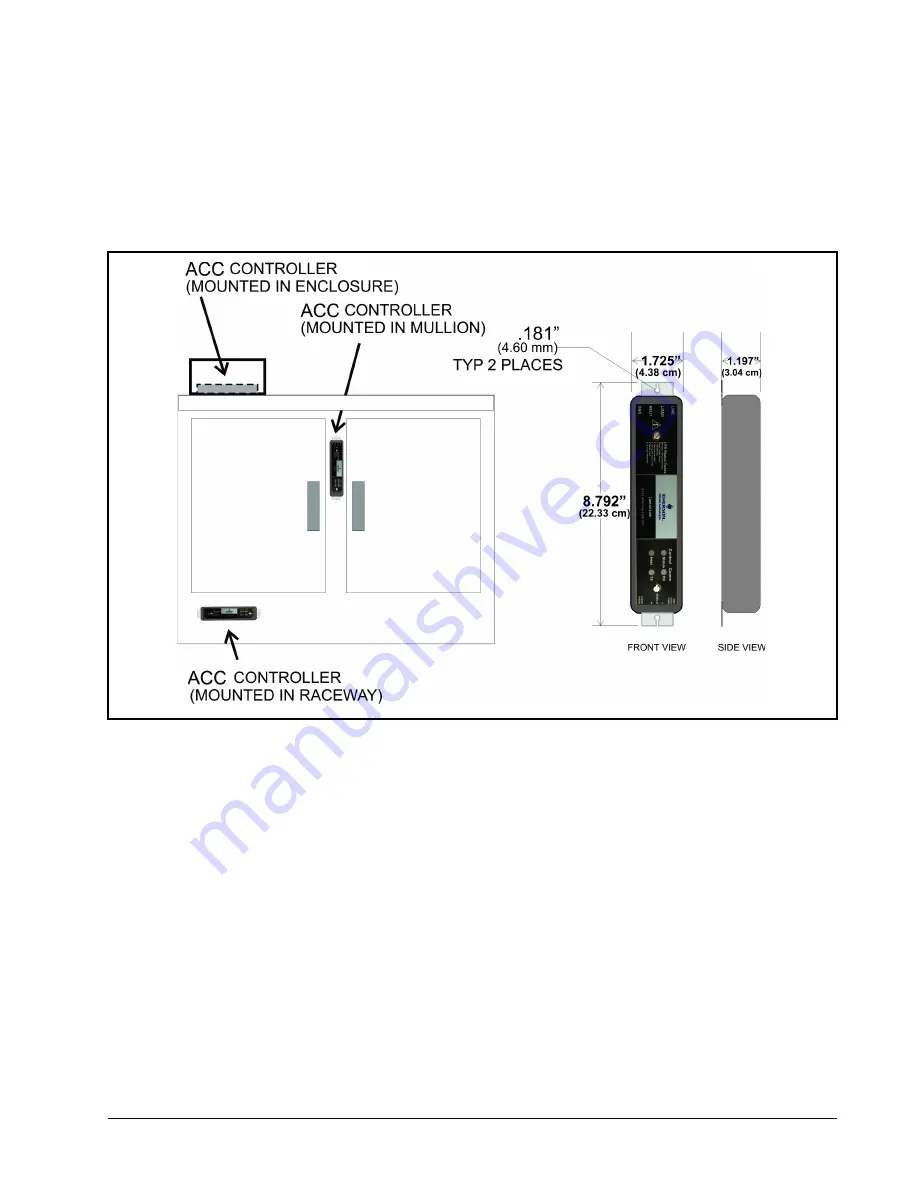
Door Frame Temperature Sensor (P/N 281-0002)
Mounting the Control Link ACC • 3
3
Mounting the Control Link ACC
The Control Link ACC is designed to be mounted in a case mullion, but may also be mounted in the raceway
or in a metal electrical enclosure on the top of the case.
Figure 3-1
shows examples of where the Control Link
ACC may be mounted.
Use the two mounting tabs at the top and bottom of the enclosure to screw the enclosure to the case wall,
raceway, or enclosure.
Use 9/64” (3.57 mm) drill pilot holes for mounting, and secure the Control Link ACC to the metal surface
using #8-32 thread forming screws. Mounting screws are not included with the Control Link ACC.
For heater current greater than 10A, the Control Link ACC UL Recognized version with external heat sink
must be used (
P/N 815-6105
). The heat sink of the Control Link ACC must be
securely mounted against a
large heat-conductive surface
. Using thermal grease, the Control Link ACC has a metal back which acts as a
heat sink, dissipating heat from the Triac that controls the heater.
The metal must be mounted against a conductive metal surface
so heat can be conducted out of the
controller. Failure to secure against the case mullion or other metal surface may cause controller overheating
and shutdown.
Figure 3-1
-
Control Link ACC Mounting