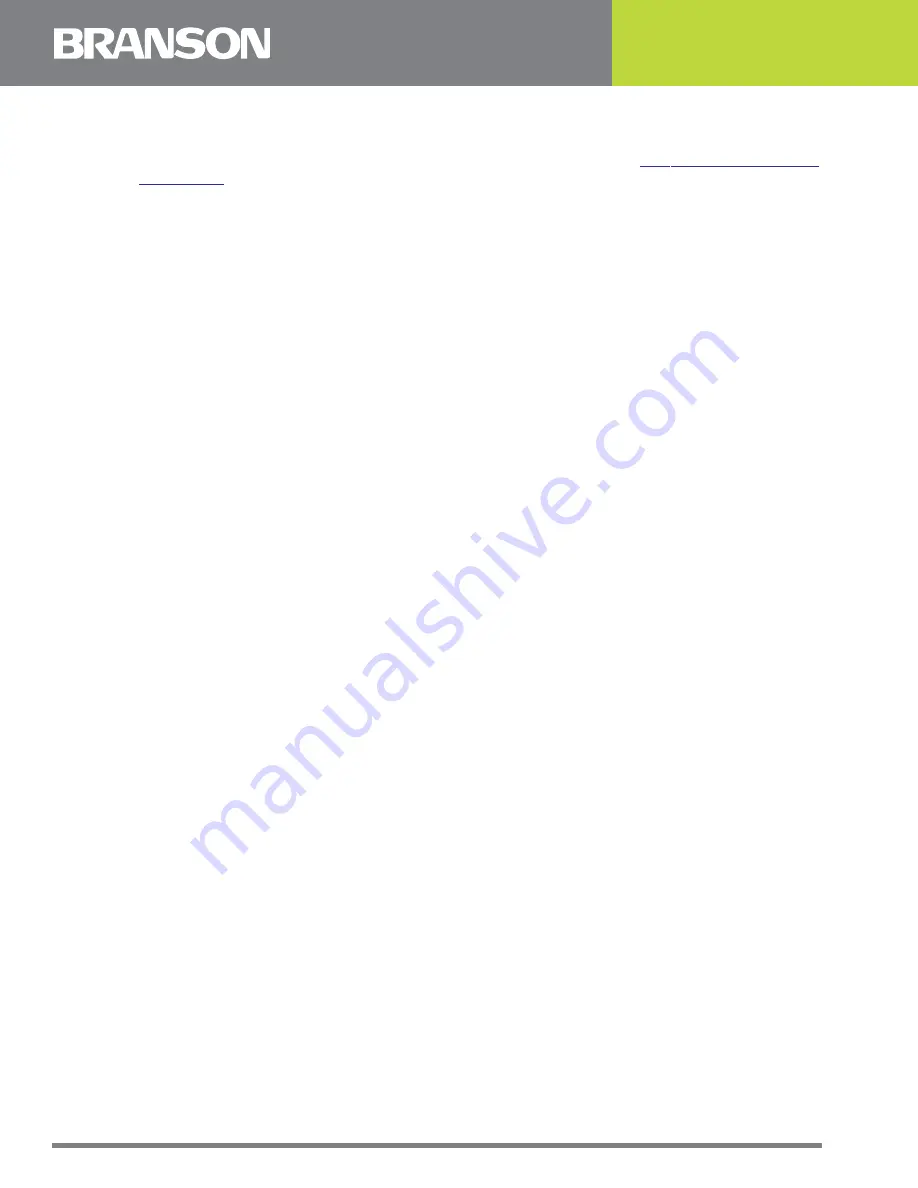
32
100-412-196 REV. 06
5.1
Installation Checklist
The LPX Power Supply is shipped with an appropriate power cordset. Additional items
required to operate the power supply in a system are detailed in
The unit should be positioned away from radiators and heating vents. A fan inside the unit
maintains a safe operating temperature in the power supply by circulating air over the
components. Therefore, place the unit so that the air intake at the back of the power
supply is not blocked. Periodically, unplug the unit and clean the air intake and also the air
exhaust underneath the power supply to ensure that dust or dirt is not restricting the flow
of air.
If the LPX Power Supply is to be used for remote operation, ensure that the unit is situated
within full view of the operator, to prevent injury or equipment damage through an
accidental or automatic start-up.
A Fan Filter Kit (EDP 101-063-934) is available (factory installed only), and is
recommended for use in areas that are high in airborne contamination.
Summary of Contents for Branson LPX
Page 4: ...iv 100 412 196 REV 06 ...
Page 6: ...vi 100 412 196 REV 06 ...
Page 8: ...viii 100 412 196 REV 06 ...
Page 10: ...x 100 412 196 REV 06 Table 7 2 System Trouble Analysis Chart 73 Table 7 3 Alarms Errors 76 ...
Page 24: ...14 100 412 196 REV 06 ...
Page 33: ...100 412 196 REV 06 23 Chapter 3 Delivery and Handling 3 1 Delivery and Handling 24 ...
Page 38: ...28 100 412 196 REV 06 4 1 4 Declaration of Conformity Figure 4 1 Declaration of Conformity ...
Page 76: ...66 100 412 196 REV 06 ...
Page 85: ...100 412 196 REV 06 75 Figure 7 2 LPX Power Supply Interconnect Diagram ...