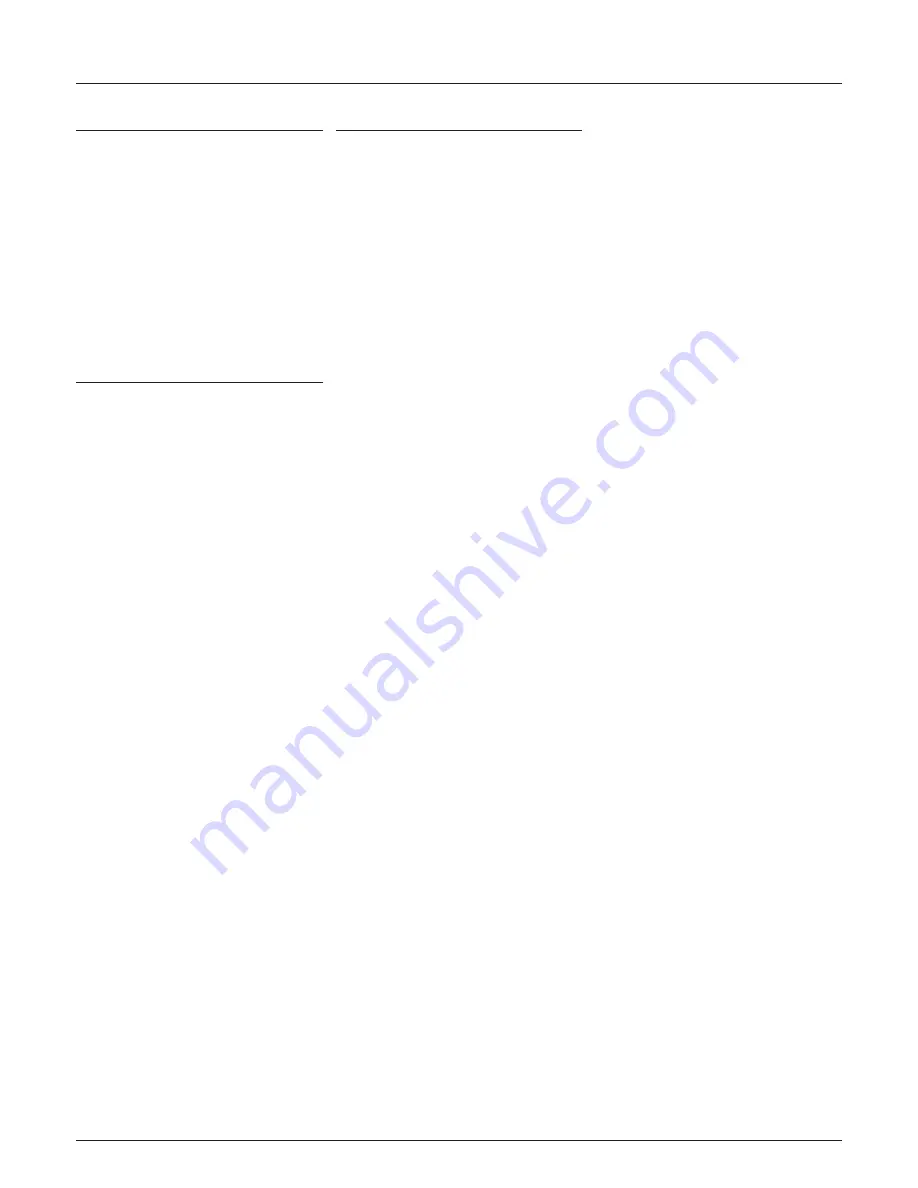
2
ANDERSON GREENWOOD
SERIES 96A VACUUM BREAKER
INSTALLATION AND MAINTENANCE INSTRUCTIONS
1 GENERAL DESCRIPTION AND OPERATION
The Anderson Greenwood Type 96A Vacuum
Breaker is designed to provide vacuum relief
and access for a positive pressure relief valve,
with one tank penetration (Refer to Figure 1).
The outlet to the positive pressure relief valve
is available with a flange size equal to the tank
size connection and one equal to the next
smaller size. A capped outlet is also available
where a relief valve is not required.
Construction of the vacuum breaker is
of aluminum and/or stainless steel with
elastomer seats and seals. NBR is the standard
elastomer with EPR and FKM optional. The seat
plate is designed to have a dead weight loading
such that opening begins at ½ oz. (0.22 kpag)
vacuum with full lift occurring at 1 oz.
(0.43 kpag) vacuum. Higher vacuum openings
are available.
Under positive pressure tank conditions,
the seat plate is held tightly against the seat due
to positive pressure acting against the inside
surface of the seat plate. As tank pressure
decreases and goes negative with respect to
the ambient pressure, the seat plate lifts in
accordance with the pressures noted above.
The elastomer seat consists of two parts: an
O-ring for sealing at high positive pressures,
greater than 2 psig (13.8 kpag), and a closed
cell sponge seat for sealing at low pressures,
less than 2 psig (13.8 kpag). Only the sponge
seat is retained in place with an adhesive.
A protective screen, 1” x 1” (25.4 mm x 25.4 mm),
mesh is provided as standard at the vacuum
inlet to prevent foreign particles from being
ingested into the breaker when the seat pallet
is open, relieving tank vacuum.
2 VACUUM BREAKER REPAIR (See figure 1)
2.1 Disassembly
2.1.0 Remove the retainer ring bolts, retainer
ring and inlet screen. Remove the seat ring
and seat plate/guide tube assembly, being
careful not to damage the sealing surfaces.
2.1.1 To disassemble the seat plate/guide
tube assembly, insert a .250 [6.35 mm]
diameter or smaller rod through the
cross drilled hole in tube to prevent it
from rotating while removing the lower
nut. Remove the nut, weight if used, and
spacer. Remove retainer and O-ring
from seat plate bolt. The guide tube
may be removed from the seat plate
bolt by placing the tube in a “VEE” block
and driving out the spring pin with a ⅛”
(3.17 mm) diameter punch for 4”-12”
valves or a
3
/
16
” (4.76 mm) diameter punch
for 16” valves.
2.1.2 Remove the guide rod bolt, guide rod, and
guide rod seal. To facilitate disassembly
insert a .250 (6.35 mm) diameter rod
through the cross drilled hole.
2.1.3 Remove sponge seat from seat ring.
(The sponge seat is cemented in place
with an adhesive)
2.1.4 Remove O-ring seat from seat ring.
2.1.5 Discard all soft goods (seats, seals and
gaskets).
2.2 Repair and assembly
2.2.1 Clean all metal parts. Any particles of
elastomer adhering to the metal parts
should be removed to facilitate proper
seating and adhesion of the new seats.
2.2.2 Inspect seat plate sealing surface for
scratches. If damaged, replace seat
plate. It may be polished with fine sand-
paper and crocus cloth, but it must be
recoated with PTFE to prevent adhesion
of the plate to the elastomer seat.
2.2.3 Inspect guide tube for wear at spring
pin holes. If holes are excessively worn,
replace tube.
STORAGE AND HANDLING
Pressure relief valve performance may be
adversely affected if the valve is stored for an
extended period without proper protection.
Rough handling and dirt may damage, deform,
or cause misalignment of valve parts and
may alter the pressure setting and adversely
affect valve performance and seat tightness.
It is recommended that the valve be stored in
the original shipping container in a warehouse
or as a minimum on a dry surface with a
protective covering until installation. Inlet and
outlet protectors should remain in place until
the valve is ready to be installed in the system.