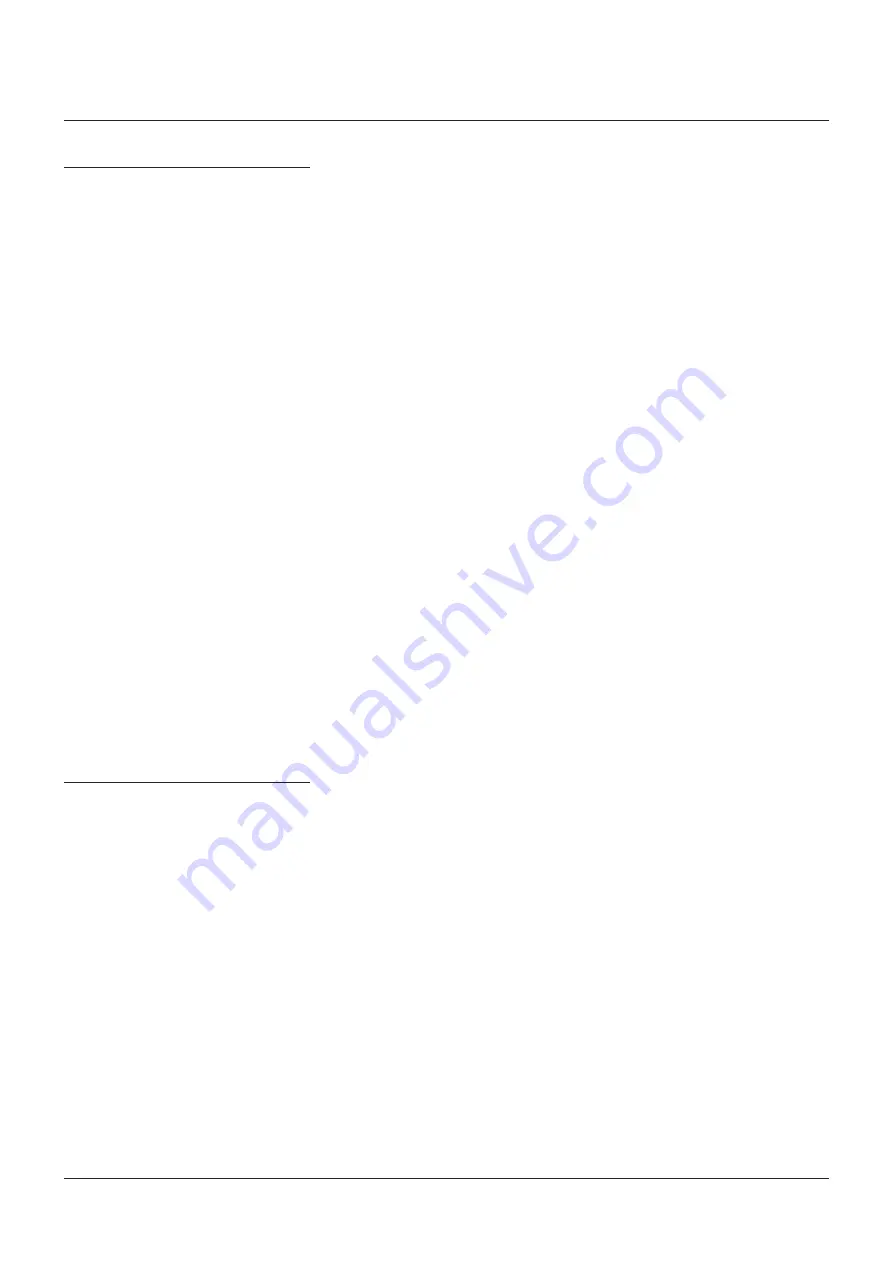
3
ANDERSON GREENWOOD
5910C PRESSURE/VACUUM RELIEF VALVE WITH INTEGRATED
FLAME ARRESTER (ATEX APPROVED)
OPERATION
When the internal tank pressure approaches
the valve setting, the pressure pallet in the
valve begins to lift. As the pressure exceeds
the valve setting, the pressure pallet lifts
off the seat ring. Excess product vapor is
allowed to vent to the atmosphere, relieving
the over pressure condition. The valve pallet
automatically re-seats as the tank pressure
drops below the valve setting. If a vacuum
within the tank approaches the valve setting,
the vacuum pallet in the valve begins to lift.
As the vacuum exceeds the valve setting,
the vacuum pallet lifts off the seat ring.
Atmospheric air is allowed to flow into the tank,
relieving the excess vacuum condition. The
pallet automatically re-seats as the vacuum
drops below the valve setting. Flame element
assemblies integrated into the unit do not
prevent ignition of flammable mixtures but
provide protection from unconfined deflagration
from the outside atmosphere to the internal
tank space Flame Arresters in the unit do not
prevent the ignition of flammable mixtures but
prevents the propagation of flame in case of
ignition . The Flame Arrester element assembly
stops the propagation of flame by absorbing
and dissipating heat through the surface
area of the crimped foil. Heat is absorbed
as ignited gas attempts to pass through the
small passages within the element assembly.
This action lowers the temperature of the
gas below its ignition point and quenches the
flame. Also, 5910C models rated for short-time
burning provide protection from deflagration
when a stabilized burn condition exists on the
unprotected side of the element.
INSTALLATION (PLACING INTO SERVICE)
5910C Series pressure and vacuum relief valves
must be mated with the appropriate flange(s).
The valve is installed vertically. The nozzle
must be plumb and the inlet flange face level to
ensure proper operation of the relief valve. The
valve’s vacuum inlet and pressure outlet must
remain clear and at a reasonable distance
from any obstructions to ensure free and easy
access for maintenance and any obstructions
which may impair flame protection or flow.
1. Remove the valve from the shipping
container. Check to see if extra loading
weights were bagged and packed separately.
CAUTION
Whenever the flame element assembly and/or
cover(s) is removed and reinstalled, the end of the
pallet stem must engage the stem guide in the
flame element assembly and/or the stem guide
chamber in the cover(s) for proper seating and
valve operation.
4. To load pressure pallet weights, perform the
following:
a. With weatherhood and flame element
assembly removed, remove pressure
pallet assembly from body.
b. Remove grip ring from pallet stem.
c. Non-variable setting: locate weight
marked “PRESSURE” and place on top
of compensating weight and/or pallet.
Secure with grip ring. If setting is less
than 2” WC, weight will be pre-loaded on
the pallet.
d. Variable setting: each lead weight is
calibrated from 1” WC increment.
(Increments of ¼” WC and 1/2” WC may be
supplied on special order). Those weights
necessary for the initial specified setting
will be tagged separately from any extra
weight provided. Remove the packaging
on the weights tagged from the initial
specified setting and place the weights on
top of the compensating weight. Secure
with grip ring. Store remaining weights for
future use (in case the setting needs to be
increased).
e. Weigh entire pallet assembly (including
installed weights). Using Table 5, confirm
that the assembly is the proper weight to
achieve the required setting. Allowable
weight tolerance is +5%,-5%.
f. Remove any remaining packing material
from valve body. Wipe pressure seat ring,
guide posts and pallet assembly with a
soft cloth to remove any material which
could affect valve operation.
g. Place pallet assembly on seat. Ensure that
pallet moves freely within guide posts and
rests flat on the seat ring.
h. Replace the weatherhood and flame
element assembly.
CAUTION
The end of the pallet stem must engage the stem
guide chamber in the cover for proper seating and
valve operation.
CAUTION
The end of the pallet stem must engage the stem
guide in the flame element assembly or the stem
guide chamber in the cover for proper seating and
valve operation.
2. Remove the weatherhood, flame element
assembly and/or cover(s) and all packing
material above the pallets and within the
valve.
3. To load vacuum pallet weights, perform the
following:
a. With vacuum cover and gasket removed,
remove vacuum pallet assembly from
body.
b. Remove grip ring from pallet stem.
c. Non-variable setting: locate weight
marked “VACUUM” and place on top
of compensating weight and/or pallet.
Secure with grip ring. Note: if setting is
less than 2” WC, weight will be pre-loaded
on the pallet.
d. Variable setting: each lead weight is
calibrated from 1” WC increment.
(Increments of ¼” WC and ½” WC may be
supplied on special order). Those weights
necessary for the initial specified setting
will be tagged separately from any extra
weight provided. Remove the packaging
on the weights tagged from the initial
specified setting and place the weights on
top of the compensating weight. Secure
with grip ring. Store remaining weights for
future use (in case the setting needs to be
increased).
e. Weigh entire pallet assembly (including
installed weights). Using Table 5, confirm
that the assembly is the proper weight to
achieve the required setting. Allowable
weight tolerance is +5%,-5%.
f. Remove any remaining packing material
from valve body. Wipe vacuum seat ring,
guide posts and pallet assembly with a
soft cloth to remove any material which
could affect valve operation.
g. Place pallet assembly on valve body seat.
Ensure that pallet moves freely within
guide posts and rests flat on the seat ring.
h. Replace the cover gasket and cover.
Tighten cover screws uniformly.