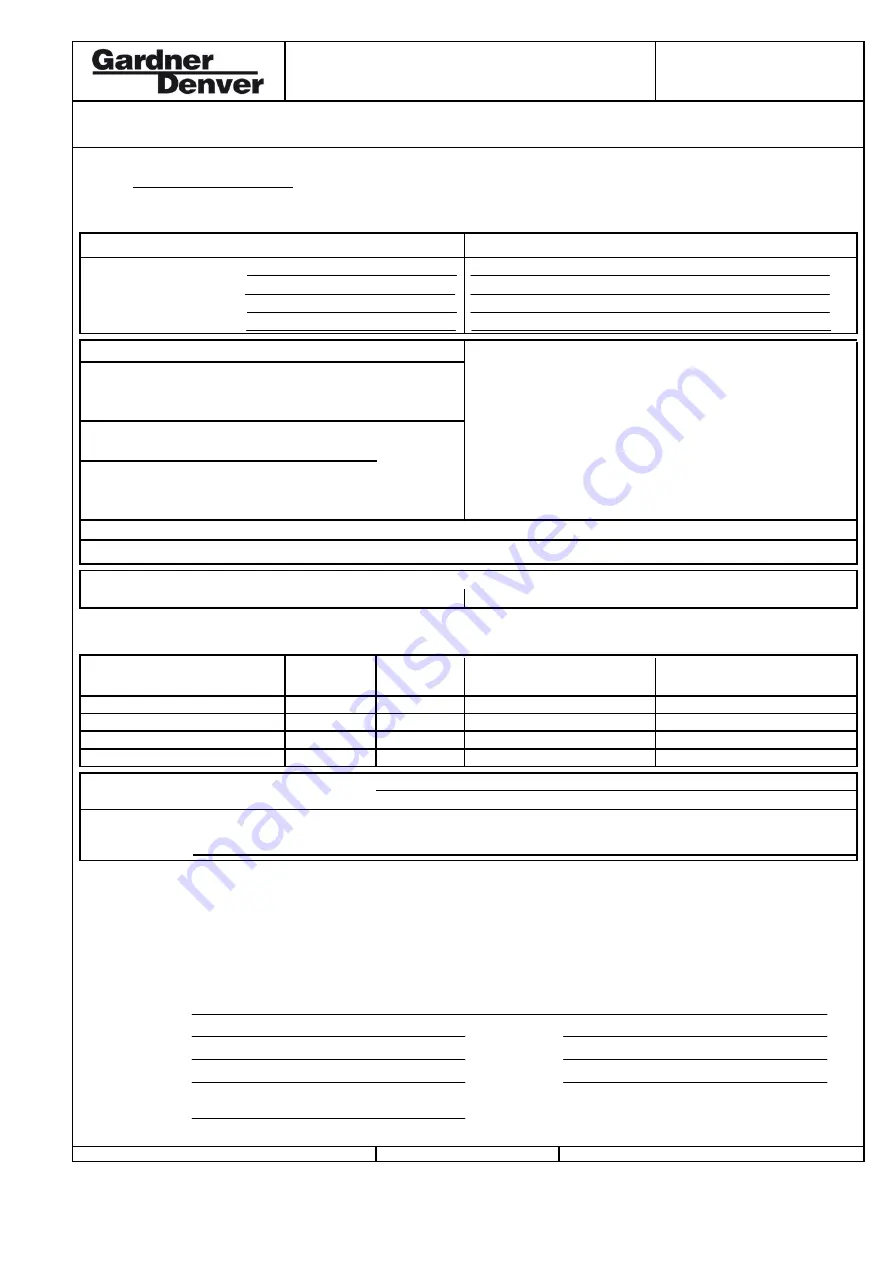
Safety declaration form
for vacuum pumps and components
Page 1 of 1
Gardner Denver Schopfheim GmbH
Roggenbachstr. 58, 79650 Schopfheim
Phone: +49/(0)7622/392-0 Fax: +49/(0)7622/392-300
Repairs and/or maintenance of vacuum pumps and components will only be carried out if a declaration has been
filled in correctly and completely.
If not, the repair work cannot be started and delays will result.
This declaration must only be filled in and signed by authorised qualified staff.
Type description:
Machine number
Order number:
Delivery date:
3. Condition of vacuum pumps/ components
4. Contamination of the vacuum pumps/
Was this being operated?
YES
NO
components when in use
Which lubrication was used?
Toxic
YES
NO
Corrosive
YES
NO
Was the pump/ component emptied?
Microbiological
*)
YES
NO
(Product/Consumables)
YES
NO
Explosive*)
YES
NO
Has the pump/ component been cleaned and decontaminaRadioactive*)
YES
NO
other
YES
NO
YES
Cleaning agent:
Cleaning method:
*) Microbiological, explosive or radioactively contaminated vacuum pumps/ components will only be accepted
with proof that they have been cleaned properly.
Type of toxic substance or process-related, dangerous reaction products with which the vacuum pumps/
components came into contact:
Trade name, manufacturer's Chemical
Hazard
Action to be taken if toxic
First aid in the event of
product name
name
class
substances are released
accidents
1
2
3
4
Personal protection measures:
Hazardous decomposition products when subjected to thermal load
YES
NO
Which?
5. Legally binding declaration
We swear that the information in this declaration is accurate and complete and that I, the undersigned, am in a
position to judge this. We are aware that we are liable to the contractor for damage caused by incomplete and
inaccurate information. We undertake to release the contractor from any damage claims from third parties arising
from incomplete or incorrect information. We are aware that, regardless of this declaration, we are directly liable
to third parties including in particular the contractor's staff entrusted with handling or repairing the product.
Company:
Street:
Post code/ Town:
Phone:
Fax:
Name (in capitals)
Position:
Date:
Company stamp:
Legally binding signature:
TOS no. / Index: 7.7025.003.17 / 03
Office responsible: GS
File management: ..\7702500317.xl
Gardner Denver Schopfheim GmbH Postfach 1260 D-79642 Schopfheim
2. Reason for the submission
1. Type of vacuum pumps/ components
7.7025.003.17