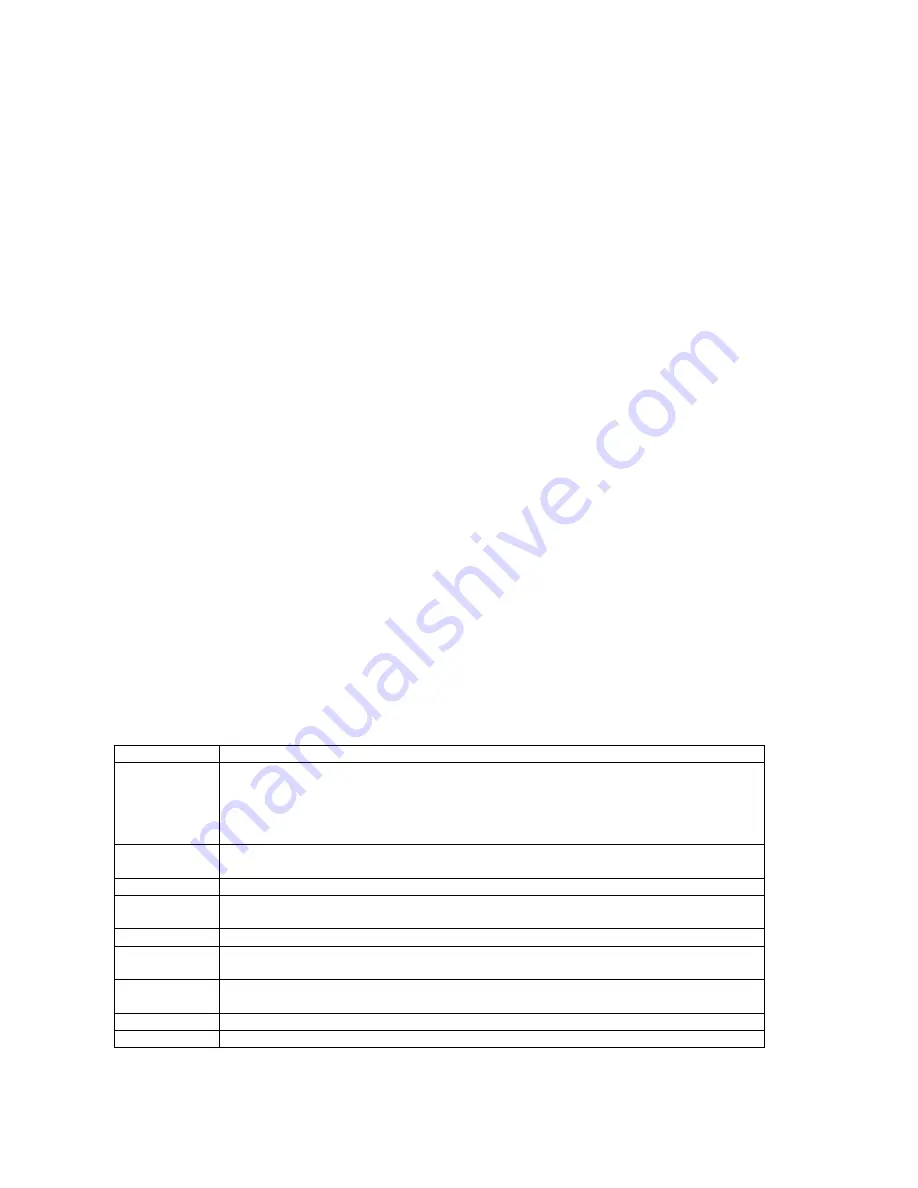
©
09.02.2006 ELKA-Torantriebe GmbH u. Co. Betriebs KG page 11
EST 204, EST 404, EST 804
11.9.
Alter the force reserve
a) Press the LERN button until Diag LED turns on (approx. 3 s).
b) Press the LERN three times. The Diag LED lights and the SL-LED flashes fast.
c) Press the BT button once to activate alteration of force. The SL-LED turns off and the Diag LED displays
the level of force reserve as sequence of flashing. The higher the number of flashes is, the higher is the
force level. Values between 1 and 16 flashes are possible.
d) Each use of the BT button increases the level about one step. Each use of the LERN button decreases
the level about one step.
e) When the required level is selected, press the BT button, keep on pressing and press the LERN button
once. The new level of force reserve is stored. After this procedure the controller returns to normal
operation mode by itself.
Note:
With every new learning of the running time, the force reserve is set to default (level 6)
11.10.
Set all parameters back to default
a) Press the LERN button until Diag LED turns on (approx. 3 s).
b) Press the LERN four times. The Diag LED flashes fast and the SL-LED lights.
c) Press the BT button once more and
keep on pressing.
The Diag and SL LED light.
d) In addition press the LERN button once. All parameters are set to default. After this procedure the
controller returns to normal operation mode by itself.
Note:
The controller has to be programmed again now.
12.
Operation after power supply break / Emergency mode
When power is switched on, the position of the gate is not known to the controller. Therefore it is only
possible to close the gate until the end position closed is found (gate is pressed against mechanical stopper).
After the position closed is known, the controller changes into normal operation mode.
If a safety device has a malfunction, it is not possible to operate the gate in normal operation mode into the
appropriate direction.
But it is possible to operate the gate in dead man (hold to run) operation using the BT button (external button
fix to terminals BT, or BT button on the controller itself). To activated dead man operation, you press the BT
button keep on pressing for 10 s. During this time the warning light will flash in periods of seconds.
Emergency mode is not possible using the radio remote control.
13.
Error codes MO 56/S
The controller displays certain error codes in case an error is detected. The code is given by the Diag LED.
The Led is flashing several times, makes a break, and repeats flashing several times. To specify the code,
please count how often the LED flashes between two breaks.
Error code
Reason
1 flash
(flashes non-
stop)
DIP switch error
1. Operation mode has been changed. Confirm with button LERN.
OR
2. The data in the EEPROM and the DIP switches are different. If the error remains
(after 1. – conforming with button LERN) send the controller back to your dealer.
2 flashes
Photocell error. During the photocell test the transmitter was switched off, but the
receiver didn’t report an obstacle.
3 flashes
Safety edge error. During the test of safety edges an error had occurred.
4 flashes
The data in the EEPROM got lost. Try to program again. If the error remains, send
the controller back to your dealer.
5 flashes
The EEPROM can’t be programmed. Send the controller back to your dealer.
6 flashes
TS observation faulty. The controller has got a hardware fault in the redundant TS
observation. Send the controller back to your dealer.
7 flashes
Relay faulty. One of the motor relays doesn’t react. Send the controller back to your
dealer.
8 flashes
Pulse creator (Hall IC) in the motor or cable between motor and controller faulty.
9 flashes
Measuring amplifier faulty. Send the controller back to your dealer.