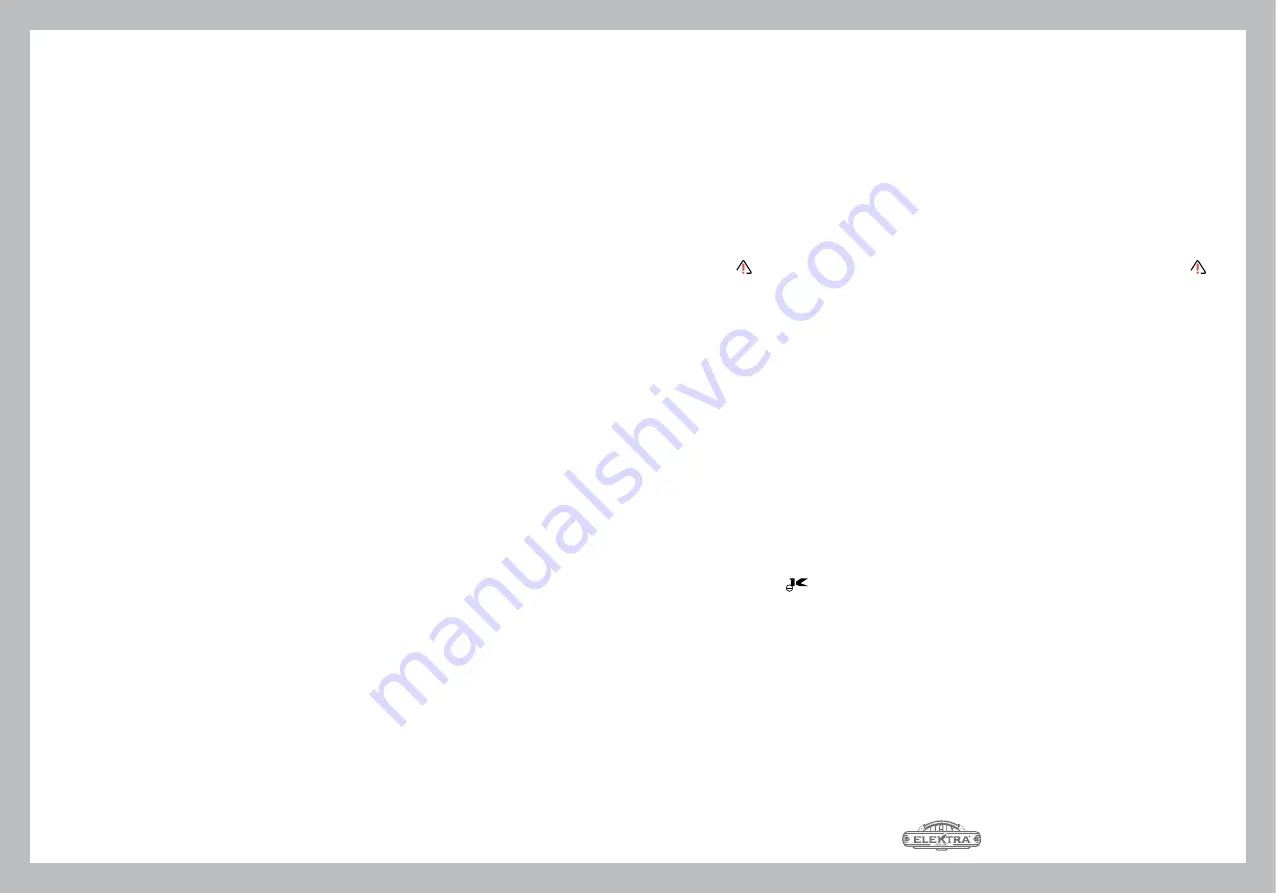
31
30
ELECTRICAL CONNECTIONS
The machine is equipped with a connecting power cable, approx. 2 metres in length, with
5 wires of the following colours:
- Green/Yellow:
Ground
- Blue:
Neutral
- Brown:
Phase 1
- Black:
Phase 2
- Grey:
Phase 3
The wires should be connected only to a terminal board on the electric switchboard
The wiring diagram is shown on an adhesive tag applied to the end of the power cable.
Electrical power specifications are given on the plate applied to the front of the machine.
The connection may be made without any modification being required to the machine,
either to a single-phase 230VAC power supply or to a triple phase 400VAC N3 power
supply, as follows:
SINGLE-PHASE 230VAC CONNECTION
Hook up the Ground and Neutral wires to the two respective terminals on the
electric switchboard.
Join up the three wires of phases 1, 2 and 3 themshelves and connect them to the
single terminal of the phase present in the electric switchboard.
THREE-PHASE 400VAC N3 CONNECTION
Hook up the Ground and Neutral wires to the two respective terminals on the
electric switchboard.
Connect each of the three wires of phases 1, 2 and 3 to the respective terminals
of the phases present in the electric switchboard.
FILLING THE HYDRAULIC CIRCUITS
1) Ensure that the water supply is turned on.
2) Switch on the machine.
3) Activate the manual dispensing of each group by pressing the button, marked by
the symbol, of the pushbutton, until complete elimination of the air contained
in the water circuits and regular outflow of water.
ADJUSTING THE FEET
Place the machine on the work counter and ensure that it is level, by adjusting the length of
the feet.
Turn the black foot counter-clockwise, when viewed from underneath, to lengthen it and
clockwise to shorten it. There are no screws or nuts to be loosened or tightened.
WATER CONNECTION
The water is fed thanks to a connection with the drinkable water supply at a minimum
pressure of 0.15 MPa (1.5 bar) and a maximum pressure of 0.6 MPa (6 bar).
Hardness of the water not above 20°F.
Were the hardness should be higher than the above value, install a water softener between
the water supply and the machine.
Should the water supply pressure exceed 0.6 MPa (6 bar), install a pressure reducer upline
of the coffee machine / water softener system.
An external check-valve may be required to meet local regulations.
The machine has a flexible steel-braided connection pipe with a 3/8 female connection,
approx. 1.7 metres in length.
1) Connect the flexible pipe to the coupling located on the bottom of the machine.
2) Connect this flexible tube to the water softener, if present, or directly to the water
supply (water mains).
INSTALLATION
B
1
3 DRAIN CONNECTION
The machine has two rubber connecting pipes, one of 20 mm in external diameter and the
other of 18 mm in external diameter, both approx. 1.5 metres in length.
This flexible pipes must be made to flow into a fixed drain manifold with a minimum internal
diameter of 50 mm located underneath the machine work counter.
The space created by difference in diameter of the two pipes inserted into the drain manifold
must be left free for the venting of air during the discharging of the water.
1) Hook up the rubber pipe of 20 mm in diameter between the pipe fitting on the plastic
drain box installed at the bottom of the machine to the drain manifold located underneath
the counter, ensuring that it does not sag and that it is not strangled.
2) Hook up the rubber pipe of 18 mm in diameter between the metal pipe fitting on the
bottom of the machine to the drain manifold located underneath the counter, ensuring
that this too does not sag and that it is not strangled.
4
4.1
4.2
5
2