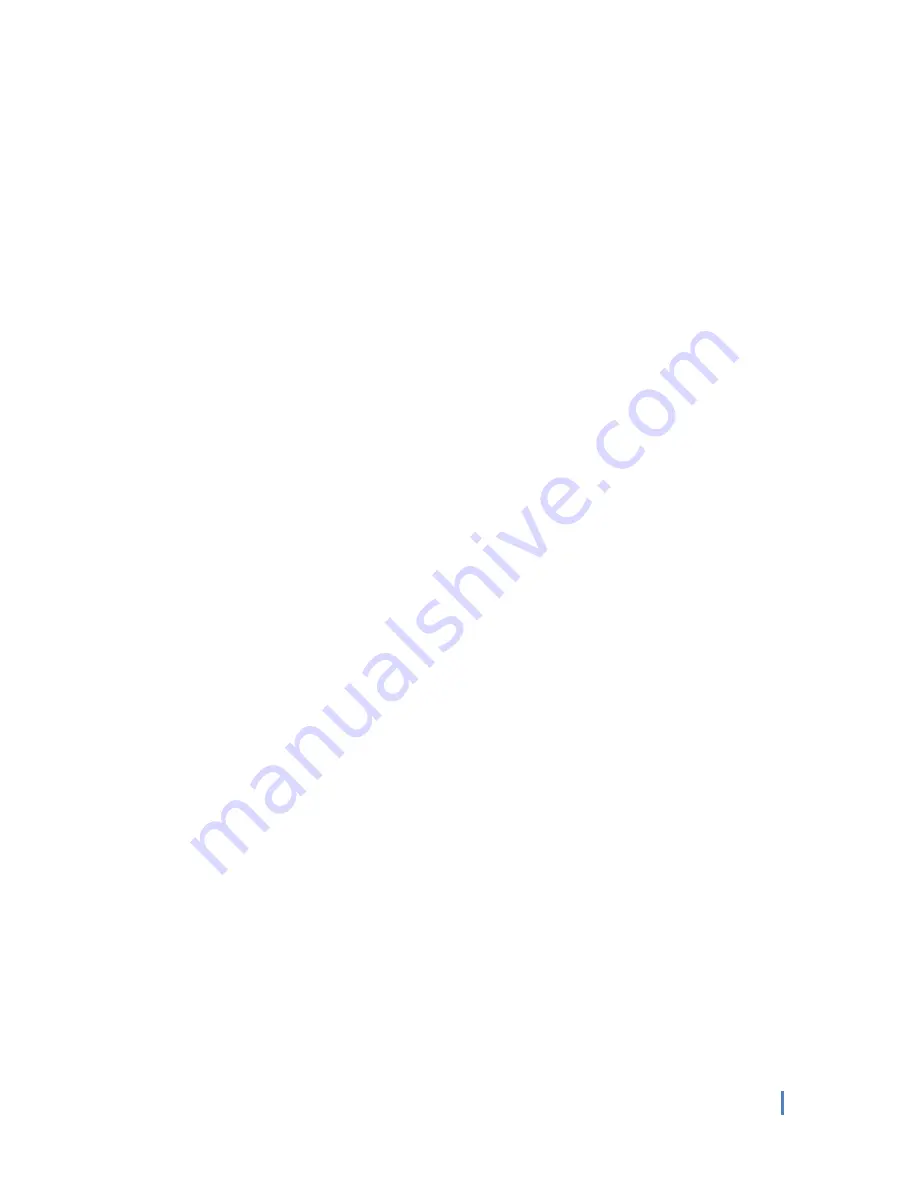
Electronics Inc. • (574) 256-‐5001 • www.electronics-‐inc.com
9
7 -‐ Process Input (0-‐0.5 Vac)
This is the 0-‐0.5 Vac process input. This input is used in junction with a current transformer. The input has a
factory-‐installed current shunt attached between terminals 7 and 5. The shunt converts 5 Aac from the current
transformer to 0.5 Vac. This input signal represents the motor current where 0 Vac input represents zero motor
amps and 0.5 Vac input represents maximum motor amps (that is, the rating of the current transformer). This
signal is displayed on the Operator Control Panel’s digital display (1). When 5 amps is applied, it is converted to 0.5
Vac and the AC-‐24 Controller will display the number set for the Display Range (28/29). The display range should
be set to match the current transformer. For example: The factory default display range is set to 100.0 for a 100:5
current transformer. If the current transformer rating is 50:5, the display range should be set to 50.0.
8 -‐ Servo Output (0-‐10 Vdc)
This is the 0-‐10 Vdc output. The Servo Output terminal (8) is connected to the Analog Input of the attached
MagnaValve (orange wire) and controls the flow of media through the MagnaValve. Zero (0) Vdc commands the
MagnaValve to flow 0 lb/min and 10 Vdc commands the MagnaValve to flow its maximum capability.
9 -‐ Enable Output (24 Vdc)
•
When the mode is in the Ready state and an Enable Input signal is received, an Enable Output signal is
generated at terminal #9.
•
When the mode is in the On state, an Enable Output signal is generated at terminal #9.
•
When the mode is in the Off state, no Enable Output signal is generated at terminal #9.
The Enable Output terminal (9) is normally connected to the Enable Input wire of the MagnaValve (blue wire).
12 -‐ Alarm Reset (24 Vdc)
When a 24 Vdc signal is temporarily applied to the Alarm Reset terminal (12), all alarms will be reset. If a constant
24 Vdc signal is applied to the Alarm Reset terminal (12), the alarms will be held in the reset state, essentially
disabling them.
13 -‐ Alarm High
The Alarm High relay contact (13) is a normally open relay contact. The Alarm High relay contact (13) will close if
the Process Input (6/7) is higher than the Setpoint value (8) plus the Alarm Band value (4) for a duration longer
than the Alarm Delay (17). The Servo On-‐Off (20) must be on for alarms to work.
14 -‐ Alarm Common
A common connection to all relays.
15 -‐ Alarm Low
The Alarm Low relay contact (15) is a normally open relay contact. The Alarm Low relay contact (15) will close if the
Process Input (6/7) is lower than the Setpoint value (8) minus the Alarm Band value (4) for a duration longer than
the Alarm Delay (17). The Servo On-‐Off (20) must be on for alarms to work.
16 -‐ Flow OK
The Flow OK relay contact (16) is a normally open relay contact. The Flow OK relay contact (16) will close if the
Process Input (6/7) is at the Setpoint within the Alarm Band (4) and will remain closed for the duration of the
blasting/peening cycle. If the Process Input (6/7) goes higher or lower than the Setpoint value (8) plus the Alarm
Band value (4) for longer than the Alarm Delay (17), the Flow OK relay contact (16) will open and remain open until
the alarms are reset. The Servo On-‐Off (20) must be on for any of the alarms to work (press the Servo On-‐Off
button (20) and ensure the Servo On LED (9) is lit).