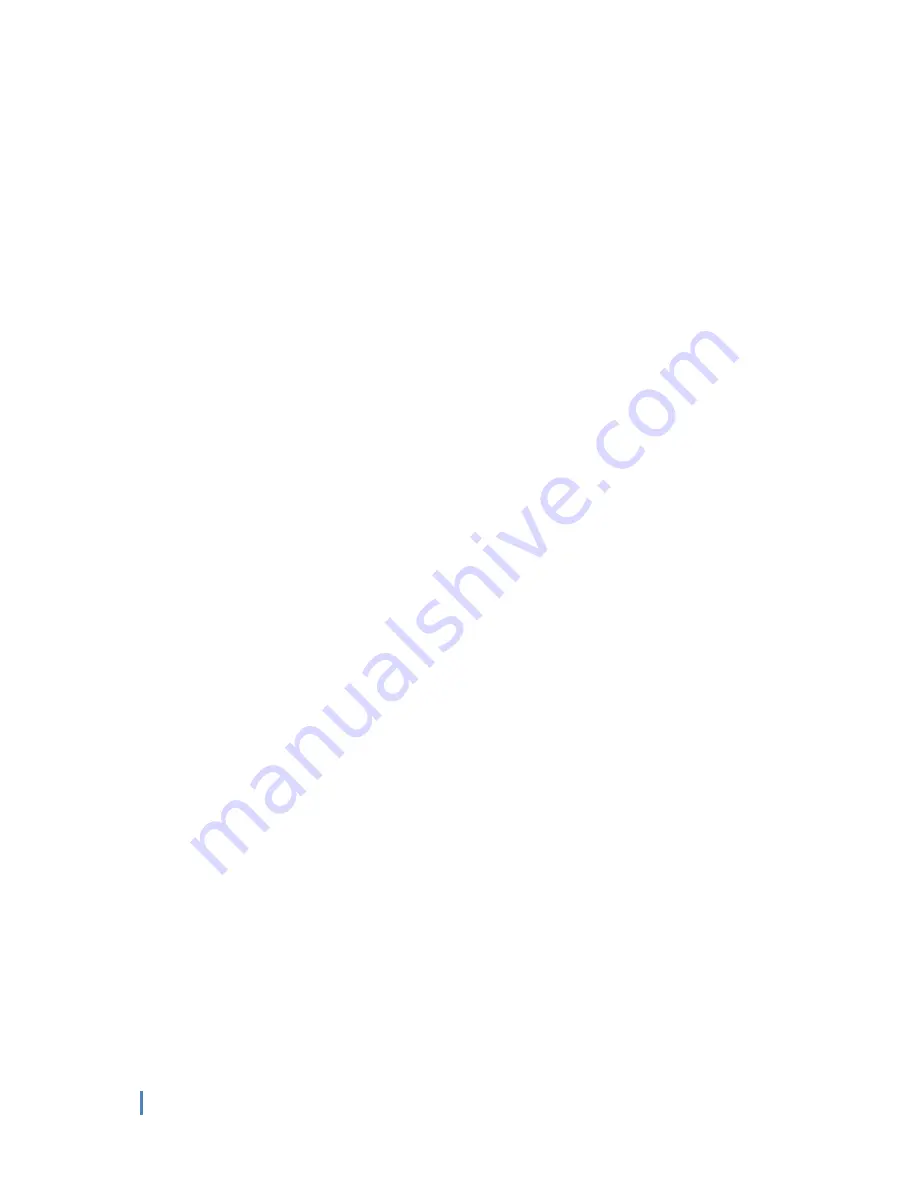
6
Electronics Inc. • (574) 256-‐5001 • www.electronics-‐inc.com
Operation
Note:
Refer to Operator Control Panel and Technical Adjustment Panel diagrams in the “Factory Default Settings”
section for location of buttons.
Setpoint
The setting for the desired motor current may come from a remote source, such as PLC, or it may be set locally
from the front panel of the AC-‐24 Controller. To set or change the Setpoint, push the Setpoint Local/Remote
button (27), select “Local”, then push the Setpoint button (8) to display the value. To change the Setpoint value,
push and hold the Setpoint button (8) and use the Down button
▼
(11) or Up button
▲
(12) as required.
Enable
The Mode button (22) will select the enable state. The choices are Off, Ready and On. The On mode will transmit
an enable signal to the MagnaValve to commence flow. The Ready mode will transmit the enable signal only when
a remote enable signal (from a PLC, for example) is received. The Off mode prevents any operation of the
MagnaValve—it will ignore the remote enable command. Note: When in the Ready mode, the Enable Delay button
(21) will delay the enable signal to the MagnaValve if set greater than 0 seconds.
Servo
Press the Servo On-‐Off button (20) to toggle between On and Off. Turn the Servo on for closed-‐loop operation and
ensure the Servo On LED (9) is lit. The dynamic operating parameters of the Servo are set with the Gain (23) and
Speed (24) buttons. These are set to typical values by the factory that should give smooth and stable performance.
The output signal of the servo command starts at zero media flow and slowly increases until the motor current
feedback signal equals the Setpoint current request. The Gain and Speed settings can be changed to help stabilize
the media flow rate or to increase the response time of the MagnaValve.