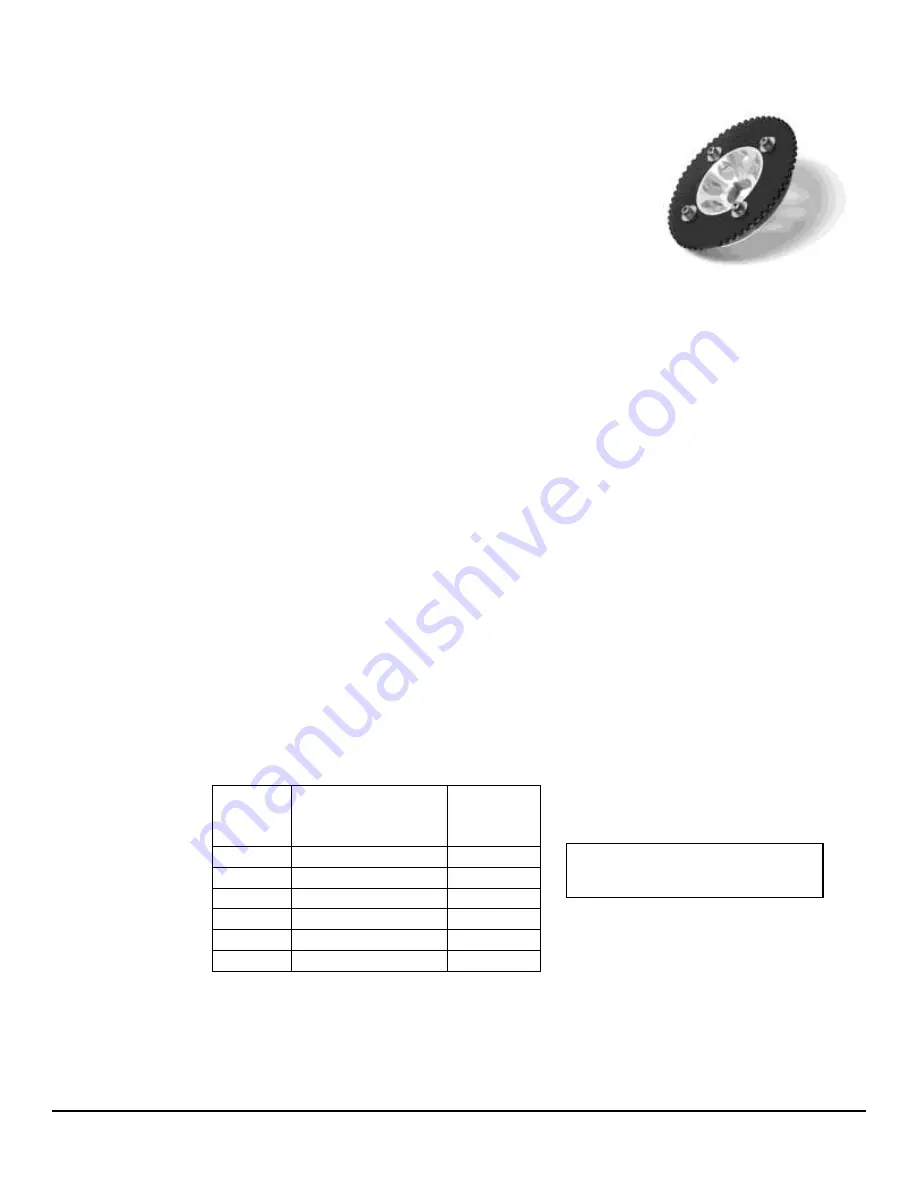
XDI Manual Version 1.8
Page 12
2017 Electromotive, Inc.
3.5 Trigger Wheel and Sensor Installation
The foundation of the XDI ultra-high resolution ignition is the 60(-2) tooth
trigger wheel. The trigger wheel is designed to give uncompromising timing
accuracy at the highest engine acceleration rates. As such, Electromotive does not
support other triggering systems, particularly those of the “flying magnet” variety.
These systems can lead to vastly inaccurate spark timing, and can contribute to
engine damage. For most applications, the 60(-2) tooth trigger wheel is mounted
on the crankshaft damper or pulley. Some applications may warrant the use of a
camshaft- or distributor-mounted trigger wheel. With this setup, a 120(-4) tooth
trigger wheel is necessary, since the camshaft turns at half the speed of the crank.
3.5.a Crankshaft Trigger Installation for 60(-2) Tooth Wheel
For a crankshaft-mounted trigger wheel setup, an appropriate place must be found to mount the wheel
and trigger. Typically, the easiest place to mount a trigger wheel is on the harmonic damper or pulley. If it is
mounted on a damper, it should be mounted on the inner hub rather than the outer dampening ring. The
damper/pulley must be keyed to the crankshaft so that it cannot spin on the crankshaft, as this would cause an
ignition timing error. When using a damper that has bolt-on pulleys, the trigger wheel can usually be mounted
between the pulleys and the damper. However, the accessory pulleys will need to be shimmed out by 1/8” (the
thickness of the trigger wheel). A variety of application-specific trigger wheels are available. Universal trigger
wheels are also available in a variety of sizes.
To choose the proper size trigger wheel, find the diameter of the pulley or damper on which the wheel is
to be mounted. The trigger wheel diameter should be at least ½” larger than this diameter. It should also be
noted that the trigger wheel should be at least ¼” from any moving magnetic pieces, such as bolts or other
fasteners, to avoid interference and false triggering. It is important that the trigger wheel be perfectly concentric
with the crankshaft centerline. To achieve concentricity, a shallow cut can be machined in the front or rear face
of the damper to create a centering ledge, and a hole can be created in the trigger wheel to match the ledge
diameter. The trigger wheel can then be drilled to bolt it to the damper.
See
Table 2
below to determine the tolerances that must be maintained when mounting the trigger
wheel. These tolerances may require the use of a lathe to true the trigger wheel with the crankshaft centerline,
which can be accomplished by putting the entire damper/trigger wheel assembly on the lathe. Note that the
maximum out-of-round is the distance between the lowest and highest teeth and the crank sensor. That is, if a
feeler gauge is used between the sensor and the wheel to measure the out-of-round, the reading between the
lowest and highest teeth should not exceed the guidelines in the table.
Trigger
Wheel
Size
Air Gap
Maximum
Out-of-
Round
2.5"
0.025" max
0.002"
3.5"
0.035" max
0.003"
5"
0.050" max
0.005"
6"
0.060" max
0.006"
7.25"
0.070” max
0.007"
8.25"
0.080” max
0.008"
Table 2
–
Crank Trigger Specifications
Summary of Contents for xdi
Page 31: ...XDI Manual Version 1 8 Page 31 2017 Electromotive Inc Appendix B Quick Reference Sheets ...
Page 32: ...XDI Manual Version 1 8 Page 32 2017 Electromotive Inc ...
Page 33: ...XDI Manual Version 1 8 Page 33 2017 Electromotive Inc ...
Page 34: ...XDI Manual Version 1 8 Page 34 2017 Electromotive Inc ...
Page 35: ...XDI Manual Version 1 8 Page 35 2017 Electromotive Inc ...
Page 36: ...XDI Manual Version 1 8 Page 36 2017 Electromotive Inc ...