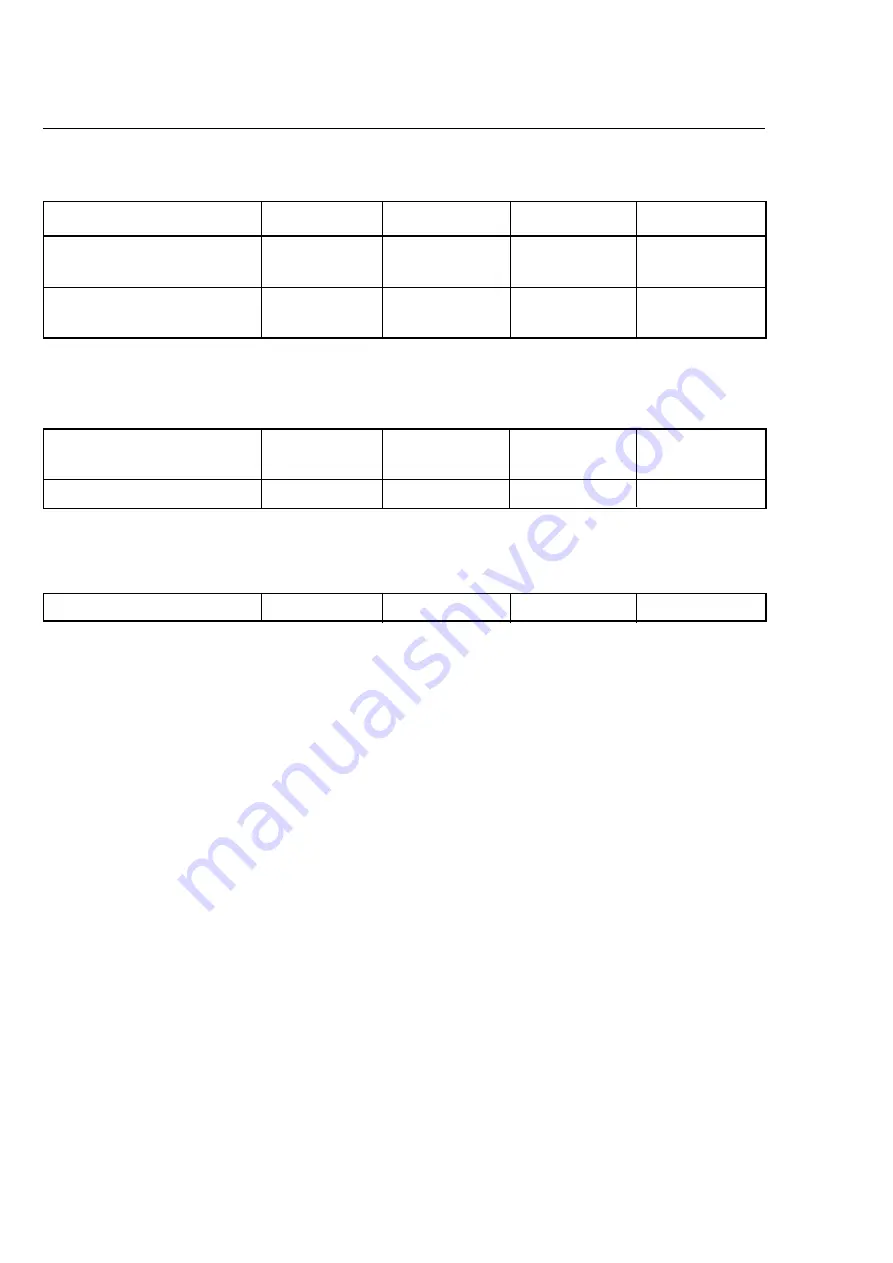
10
Technical data
W4400H
W4600H
W4850H
W41100H
13.8
12.7
12.0
11.1
15.8 ± 1.2
15.9 ± 6.4
22 ± 7.3
24 ± 7.3
Frequency of the
dynamic force
Hz
Max floor load
at extraction
kN
Technical data
5.5
6
6.7
6.8
Sound levels
Airborne sound level
dB (A) re 2x10
-5
Pa
With insulation
Motor
Power consumption kW
75
76
73
73
< 70
< 70
< 70
< 70