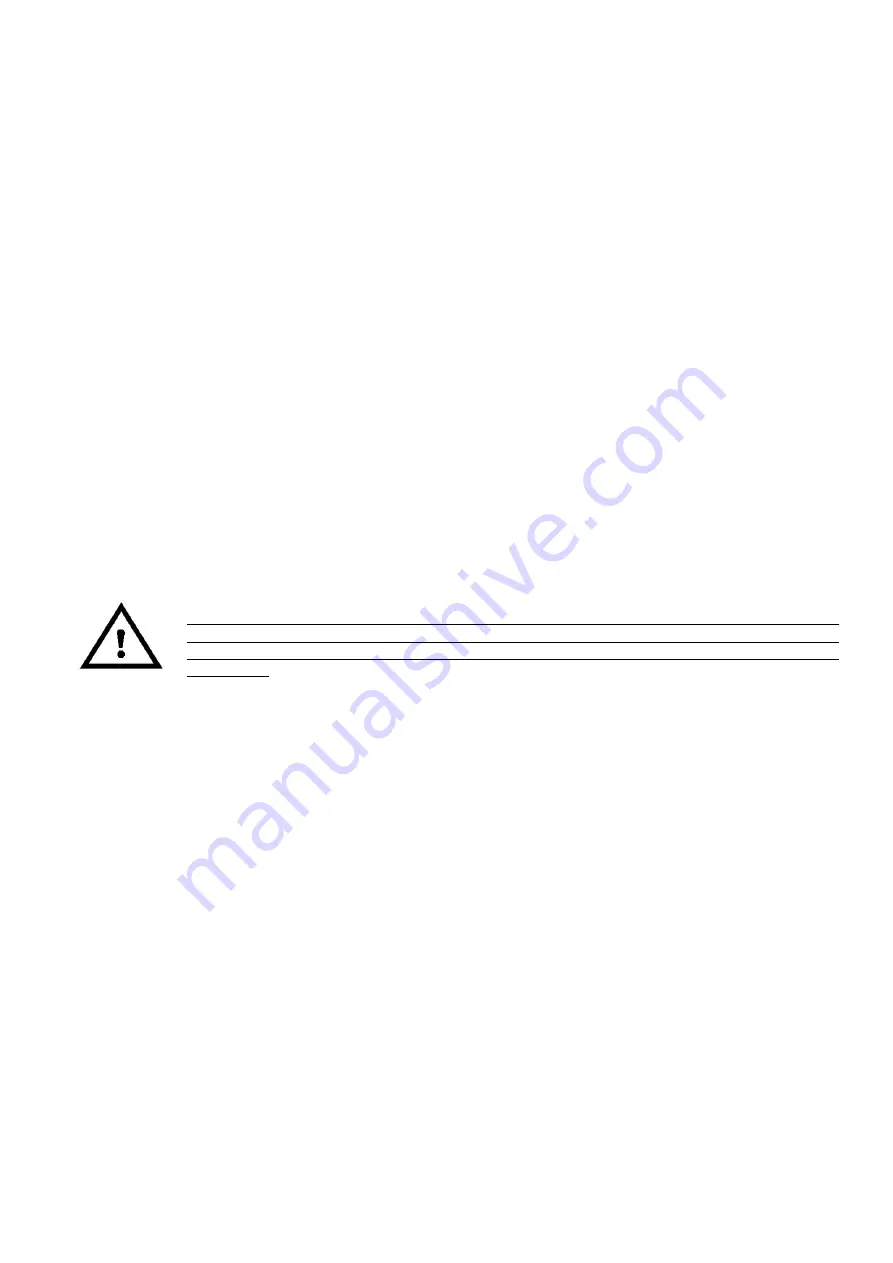
10
IMTP(D) 2.2 – ITTP(D) 2.2/4.0/5.5/7.5 - ELECTROIL
ENG
5.3
Pump hydraulic connection
Connect the hydraulics according to the standard regulations.
This product can work when connected to the waterworks or taking water from a water tank.
If you connect the system to the waterworks, you have to respect the regulations in force issued by local authority
(Common, local authority, etc…). It is important to put a pressure switch on the inlet leader; it switches off the
motor power in case of low pressure (it is a dry-working external protection). The inverter have a port for a
normally-closed generic contact: EN and GND (0V) on the logic board.
Verify the amount of pressure between the waterworks and the maximum pump pressure, does not exceed the
maximum pump pressure value (nominal pressure).
Besides, it is important to put a pressure gauge on the inlet and on the outlet leader, so it is possible to regulate
the differential pressure value, according to the real conditions of the system.
For the absolute pressure control, for centrifugal pumps, on the delivery side it is necessary to install a special
pressure gauge (standard K16) with an output signal between 4 – 20 mA to connect on the specific electronic
port.
For the Differential pressure control, for circulating pumps, on the inlet and delivery side it is necessary to install
a special pressure gauge for high temperature (K3T or K5T) with an output signal between 4 – 20 mA to connect
on the specifics electronic port.
As a rule it would be better to install flexible or rigid pipes on inlet and outlet branches, on-off valves on inlet and
outlet branches, a no return valve. To avoid drying the system for replacement of the membrane surge tank
(recommended), pressure gauge or pressure transducer, it would be better to install some on-off valves between
the tank connection and the system. Put the pressure transducer downstream the non-return valve, if it is present.
It would be better to install a cock, used during the system calibration; it is not necessary if there is an exit near
the pump.
5.4
Electric wirings
Check voltage and frequency of the power supply are the same of the nominal values of the control system, that are
written on the box. Be certain of having a good short-circuit protection in your electric system.
Before working, be certain all the circuit is without voltage (also the connections voltage clear). Disconnect the
inverter from the power supply before working on electrical or mechanical parts of the system.
Wait at least 2 minutes after the power supply disconnection before working on the inverter; this
allow the capacitors discharge (after 2 minutes delay, opening the inverter case, check that the led
on the electronic power must be completely switched off in order to be sure that are completely
discharged).
If the local regulation about electric system provides for a magneto-thermal differential switch, install one. Select the
protection with curve for alternative current or pulsing current (type A or C).
The unit is equipped with all those technical arrangements required to ensure a good functioning under normal
installation.
The control system has a entry-filter and it conforms to the EMC directive, also have a current overload protection
which guarantees absolute protection when the Inverter is combined with motors that not exceed
the maximum
power.
IMPORTANT: For EMC is necessary that the power wires of control panel and motor power wires (when the motor
are separated from the inverter) are shielded type (or armoured) with individual conductors of appropriate section
(current density <= 5 A/mm2). These cables must be the minimum length necessary. The screen conductor must
be connected to the ground by both sides. On motor use the metal case for connection to the ground of the screen.
To avoid loops that can create mass disturbances radiated (antenna effect), the motor operated by the frequency
converter must be connected on the ground individually, always with a low-impedance using the metallic box of the
machine.
The wires from power supply to frequency converter and wires from frequency converter – motor (if the motor is
separated to the Inverter) must be spaced as much as possible, not to create loops, not place them parallel at
distance less than 50 cm.