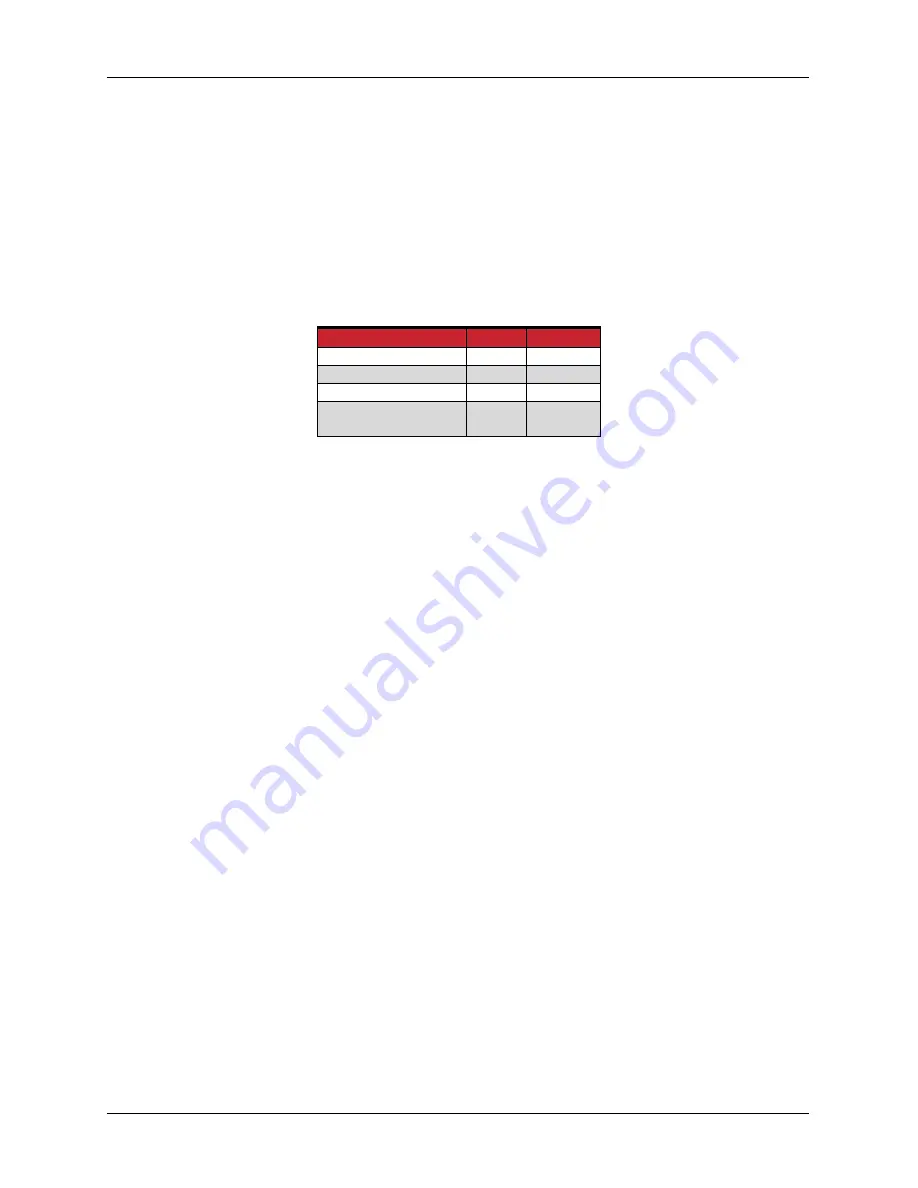
© ElectroCraft 2022
42
CPP-x06V48A-SA-CAN Drive User Manual
The power rating of the braking resistor
need not
be the maximum power value, as the value of power
dissipated across the resistor depends on the duty cycle of braking.
Duty Cycle = Time in Braking / Total cycle Time
Calculation for average power value of the braking resistor using duty cycle is as follows:
Average Power value = Resistor On voltage x Maximum deceleration current of the motor x Duty Cycle
For example, consider an application with power supply voltage of 24V and motor deceleration current of
6A, so a 4 ohm resistor is picked (according to section 13.3.1). The load accelerates for 6 seconds and
brakes for 4 seconds, which gives a total cycle time of 10 seconds. Example parameters are referenced
in the table below:
Parameter
Value
Unit
Total cycle Time
10
Seconds
Time in Braking
4
Seconds
Volts during braking
28
Volts
Deceleration
current
6
Amps
Duty Cycle = 4/10 = 0.4
Average Power value = 28 x 6 x 0.4 = 68 Watts
Therefore, in this example a 68 Watts resistor will be able to handle the braking power of 168 watts for 4
seconds and cools down for 6 seconds as long as the maximum current of the resistor is not exceeded,
and the thermal sensitive switch does not trip.
Considering the same application as referenced in the
above example but the “Total cycle Time” is 10
minutes and “Time in Braking” is 4 minutes.
Duty Cycle = 4/10 = 0.4
Average Power value = 68 Watts
A 68 watts resistor will not handle 168 watts of braking power for 4 minutes. The brake resistor will get too
hot and it will trip the user supplied temperature sensitive switch (refer to section 13.5), in turn
disconnecting the braking resistor from the drive. The drive will then fault due to shunt overpower or bus
over voltage after the braking resistor is disconnected from the drive while braking. Hence, the Average
power value of the resistor also gets affected by the duration of the braking time. The selected power
rating for any external brake resistor is application dependent. Usually, a heavy-duty wire wound resistor
will work best.
13.4 Minimum external bulk capacitance
A bulk capacitor is used to delay the bus voltage rising up to the brake resistor On voltage during braking.
This increases the braking resistor Off time, in turn giving more time for the brake resistor to cool. The
capacitor must be rated to a voltage equal or higher than the brake resistor On voltage (set in the
configuration software).
ElectroCraft recommends connecting a capacitor of 50
μF per each ampere deceleration current across
J1 pin 1 and pin 2 as shown in section 13.5. For example, the application given in section 13.3.2 has a
deceleration current of 6A, so it will need a 300
μF capacitor. This recommendation has proven sufficient
in the majority of applications. If further support is needed or this recommendation does not provide the
required performance, please contact ElectroCraft.