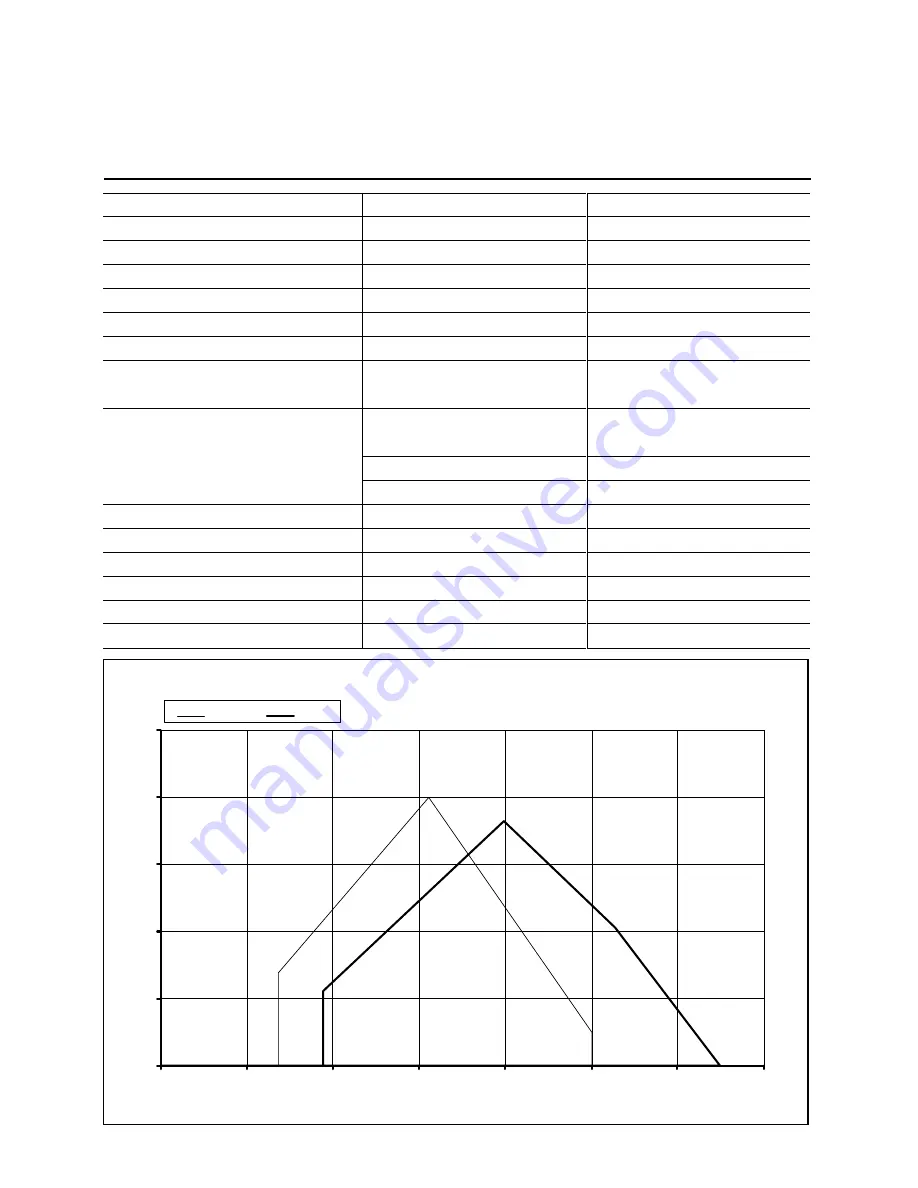
5
Technical Data Sheet
Monoblock Oil Burner
EK 6.240 / 300 L-E
Technical Data
Burner output
Fuel flow rate
Operating mode
Type of fuel
Burner control box
Flame sensor
Fan motor
Pump unit
Gear output
Pressure
Nozzle rod
Nozzle
Oil hoses / External connection
Actuator
Ignition transformer
Weight
Operating range EK 6.240 / 300 L-E
0
5
10
15
20
25
0
500
1000
1500
2000
2500
3000
3500
6.240 L
6.300 L
Q Burner output [kW]
F
Air temperature 20°C, test values according to EN 267 (DIN 4787) at 171 m
above sea level
P
res
su
re
i
n
c
om
bu
s
tio
n
c
ha
m
b
er
[
m
b
a
r]
6.240 L-E
681 - 2500 kW
57 - 210 kg/h
fully modulating
Light oil EL
BCS / LAL 2 / LOK 16
QRB 3 / RAR 7
400 / 690 V, 50Hz
4,0 kW, 8,5 A, 2800 min-¹
SMG 16026 - 1,1 kW
735 l/h
30 bar
RDN
Thread 7/8"
DN 20 x 1500 / R 1/2"
SAD 15 / STM 40 / MM1004
160 kg
≈
ZA20 140 / ZM20-14
6.300 L-E
940 - 3250 kW
79 - 280 kg/h
fully modulating
Light oil EL
BCS / LAL 2 / LOK 16
QRB 3 / RAR 7
400 / 690 V, 50Hz
4,0 kW, 8,5 A, 2800 min-¹
SMG 16026 - 1,1 kW
735 l/h
30 bar
RDN
Thread 7/8"
DN 20 x 1500 / R 1/2"
SAD 15 / STM 40 / MM1004
160 kg
≈
ZA20 140 / ZM20-14
No.:
102.880.4353
03/05
Technical Data
EK 6.240 / 300 L-E