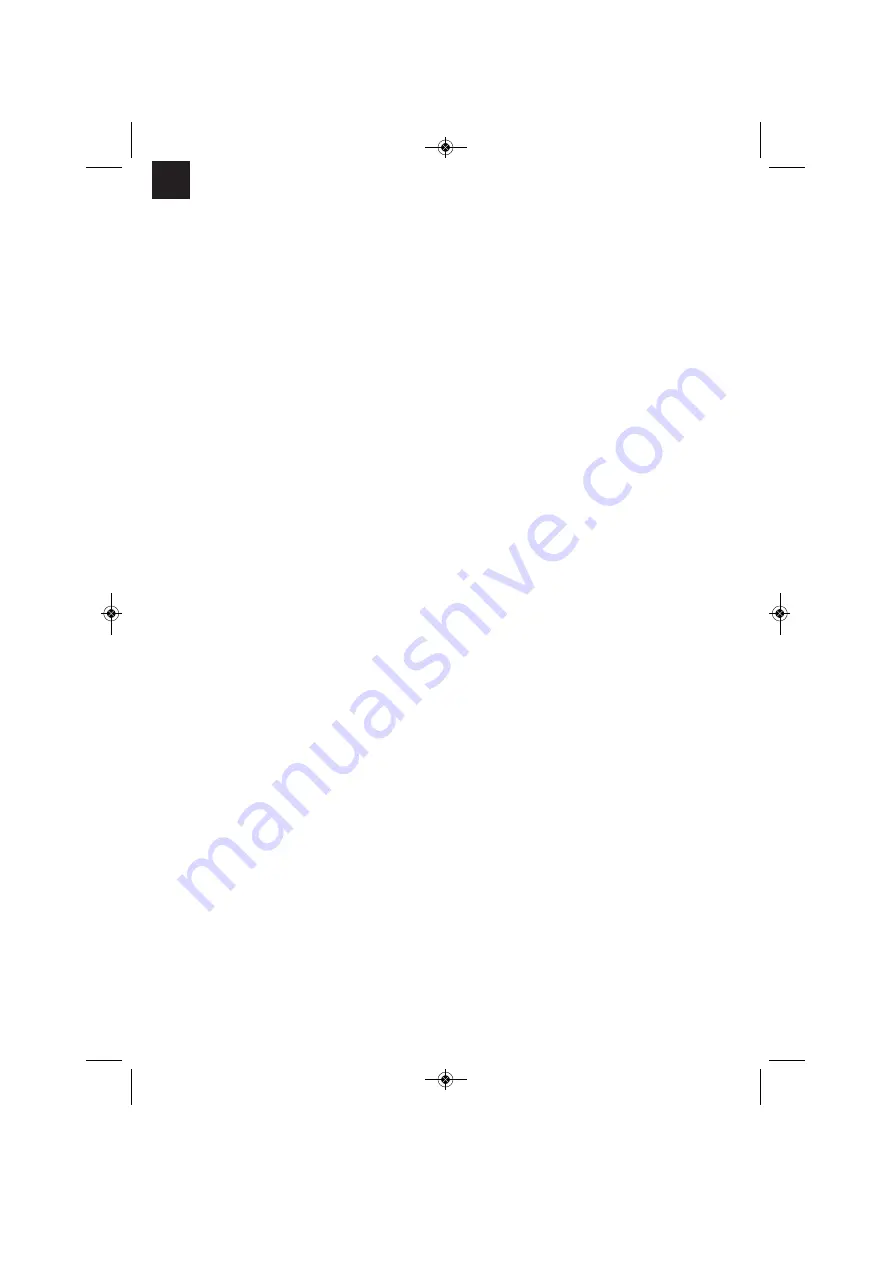
Important!
When using the equipment, a few safety precautions
must be observed to avoid injuries and damage.
Please read the complete operating instructions and
safety regulations with due care. Keep this manual in
a safe place so that the information is available at all
times. If you give the equipment to any other person,
hand over these operating instructions and safety
regulations as well. We cannot accept any liability for
damage or accidents which arise due to a failure to
follow these instructions and the safety instructions.
1. Safety regulations
Safety information
Please note
Handling this system incorrectly may be hazardous
for persons, animals and property. The user of this
system is responsible for his/her own safety and for
the safety of others.
Read these operating instructions and follow all the
regulations.
앬
Repairs and/or maintenance work may only be
carried out by qualified personnel.
앬
Use only the welding cables supplied.
앬
Ensure that the appliance is looked after properly.
앬
To ensure that sufficient air can be drawn in
through the ventilation slits, the appliance should
not be constricted or placed next to a wall while it
is operating. Make sure that the appliance is
correctly connected to the mains supply.
Do not subject the mains lead to any tensile
stress. Unplug the appliance before you change
its position.
앬
Check the condition of the welding cables, the
burner and the earth terminals; wear on the
insulation and the live parts may result in
dangerous conditions and reduce the quality of
the welding work.
앬
Arc welding generates sparks, molten metal
particles and smoke, so the following is required:
Remove all inflammable substances and/or
materials from the working area.
앬
Ensure that there is adequate ventilation.
앬
Do not weld on tanks, vessels or pipes that have
contained inflammable liquids or gases. Avoid all
direct contact with the welding circuit; the idling
voltage between the burner and the earth terminal
may be dangerous.
앬
Do not store or use the appliance in wet or damp
conditions or in the rain.
앬
Protect your eyes with specially designed goggles
(DIN level 9-10), which you can attach to the
supplied safety shield. Wear gloves and dry safety
clothing that are not contaminated by any oil or
grease to ensure that your skin is not exposed to
ultraviolet radiation from the arc.
앬
Do not use this welder to defrost pipes.
앬
Make sure that the equipment is set up so it stands
firmly. If the equipment is set up on an angled
surface, it may need to be secured by tying or
blocking the wheels.
Remember.
앬
The radiation from the arc can damage your eyes
and cause burns on skin.
앬
Arc welding generates sparks and droplets of
molten metal; the welded workpiece may start to
glow and will remain very hot for a relatively long
period of time.
앬
Arc welding releases vapors that may be harmful.
Every electric shock is potentially fatal.
앬
Do not approach the arc within a radius of 15 m
unprotected.
앬
Protect yourself (and others around you) against
the possible hazardous effects of the arc.
앬
Warning: Depending on the mains connection
conditions at the connection point of the welding
set, other consumers connected to the mains may
suffer faults.
Important!
If the supply mains and circuits are overloaded, other
consumers may suffer interference during the
welding work. If you have any doubts, contact your
electricity supply company.
Sources of danger during arc welding
Arc welding results in a number of sources of
danger. It is therefore particularly important for the
welder to comply with the following rules so as not to
place himself or others in danger and to avoid
endangering people and equipment.
1.
Have all work on the mains voltage system, for
example on cables, plugs, sockets, etc.,
performed only by trained electricians. This
particularly applies to configuring intermediate
cables.
2.
If an accident occurs, disconnect the welding
power source from the mains immediately.
3.
If electric touch voltages occur, switch off the
welding set immediately and have it checked by
an expert.
4.
Always check for good electrical contacts on the
welding current side.
5.
Wear insulating gloves on both hands for
8
GB
Anleitung_BT_FW_100_GB_SPK7__ 13.03.13 13:12 Seite 8