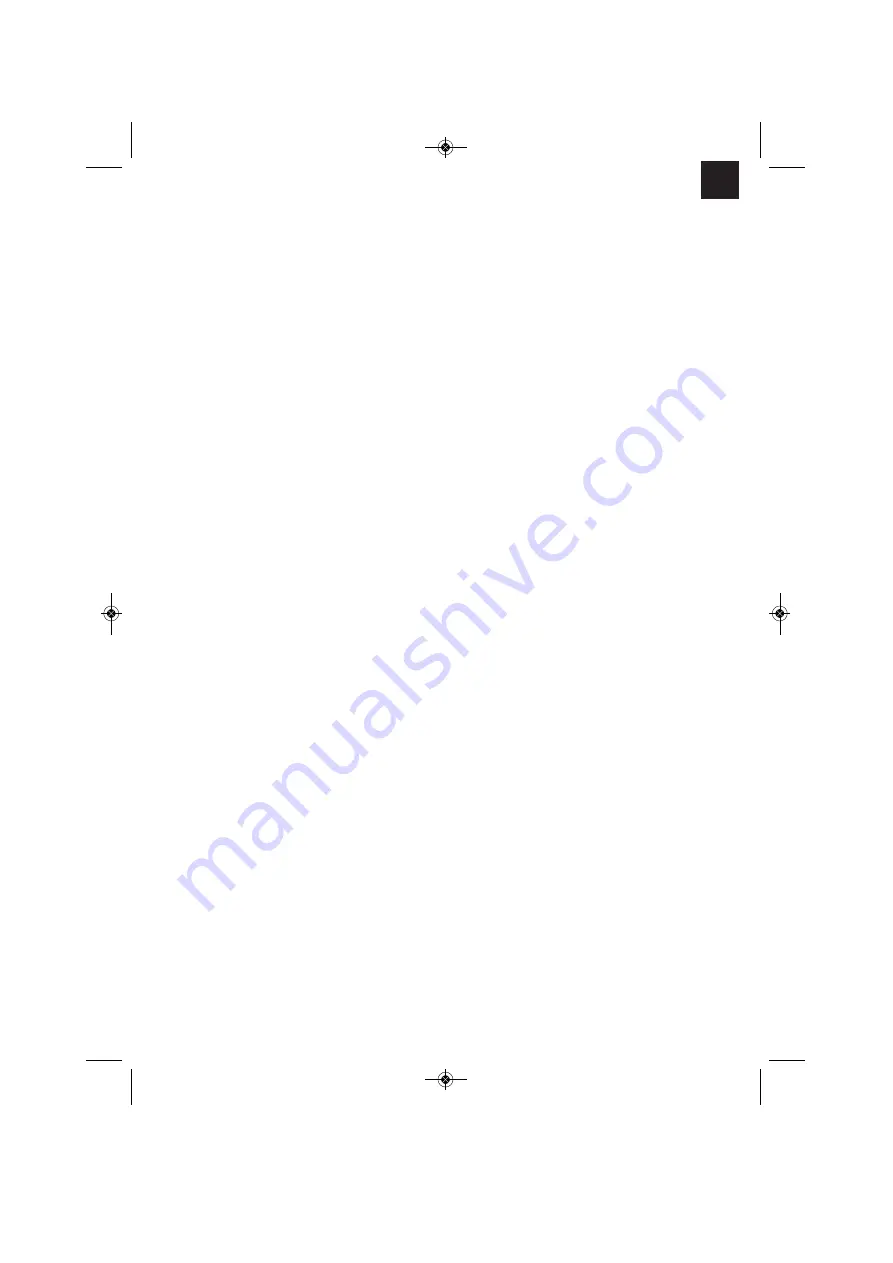
When the arc is burning, the welding set will feed
wire into the weld pool. When the weld nugget is
large enough, move the burner slowly along the
required edge. Move it to and fro if necessary to
enlarge the weld pool a little.
Find the ideal setting of the welding current and wire
feed speed by carrying out a test weld. Ideally an
even welding noise will be audible. The penetration
depth should be as deep as possible, but the weld
pool must not be allowed to fall through the
workpiece.
Do not remove the slag until the weld has cooled. If
you want to continue a welding job on an interrupted
weld seam, the slag from your initial attempt must
first be removed.
6.4 Safety equipment
6.4.1 Thermostat
The welding set is fitted with an overheating guard
that protects the welding transformer from
overheating. If the overheating guard trips, the
control lamp (2) on your set will be lit. Allow the
welding set to cool for a time.
7. Cleaning, maintenance and ordering
of spare parts
Always pull out the mains power plug before starting
any cleaning work.
7.1 Cleaning
n
Keep all safety devices, air vents and the motor
housing free of dirt and dust as far as possible.
Wipe the equipment with a clean cloth or blow it
down with compressed air at low pressure.
n
We recommend that you clean the equipment
immediately after you use it.
n
Clean the equipment regularly with a damp cloth
and some soft soap. Do not use cleaning agents
or solvents; these may be aggressive to the
plastic parts in the equipment. Ensure that no
water can get into the interior of the equipment.
7.2 Servicing
There are no parts inside the equipment which
require additional maintenance.
7.3 Ordering replacement parts:
Please provide the following information on all orders
for spare parts:
n
Model/type of the equipment
n
Article number of the equipment
n
ID number of the equipment
n
Spare part number of the required spare part
For our latest prices and information please go to
www.isc-gmbh.info
8. Disposal and recycling
The equipment is supplied in packaging to prevent it
from being damaged in transit. The raw materials in
this packaging can be reused or recycled. The
equipment and its accessories are made of various
types of material, such as metal and plastic.
Defective components must be disposed of as
special waste. Ask your dealer or your local council.
13
GB
Anleitung_BT_FW_100_GB_SPK7__ 13.03.13 13:12 Seite 13