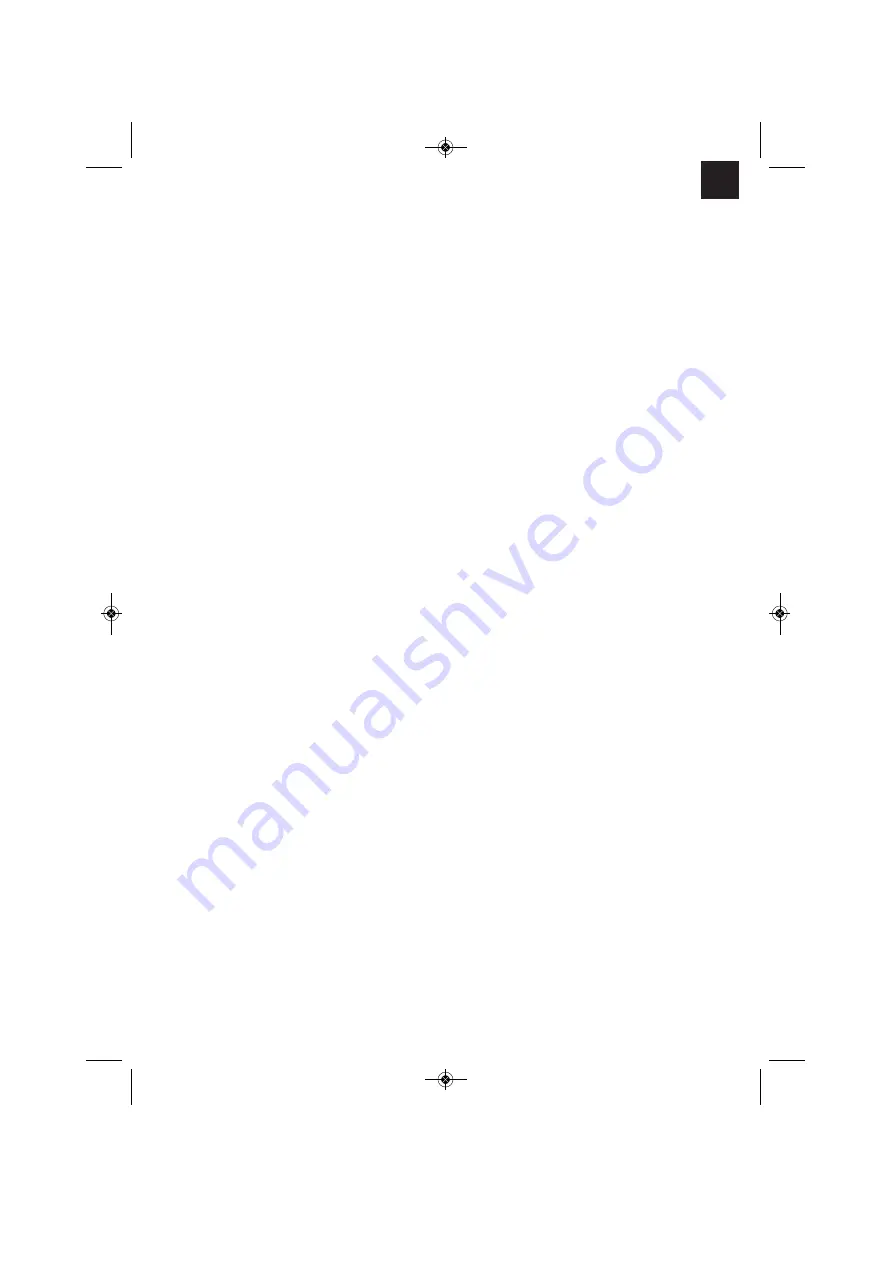
11
GB
5. Before starting the equipment
5.1 Assembly (Fig. 7-13)
5.1.1 Fitting the carrying strap (1)
n
Guide the carrying strap (1) through the slit on
the rear of the equipment, over the housing
cover (3) and through the slit on the front of
equipment. Connect the ends of the carrying
strap as shown in Figure 5 and adjust the strap
to the required length.
Fitting the welding screen (13)
n
Place the welding glass (l) and the transparent
safety glass (m) over it in the frame for the safety
glass (k) (Fig. 7).
n
Press the safety glass retaining pins (q) into the
holes in welding screen frame (s) from the
outside. (Fig. 8).
n
Place the frame for the safety glass (k) with the
welding glass (l) and transparent safety glass (m)
from the inside into the recess in the welding
frame (s), press the safety glass retaining
bushes (n) on to the safety glass retaining pins
(q) until they engage to secure the frame for the
safety glass (k). The transparent safety glass (m)
must be on the outside. (Fig. 9).
n
Bend the top of the welding screen frame (s)
inwards (Fig. 10/1) and fold down the top corners
(Fig. 10/2) Now bend the outer sides of the
welding screen frame (l) inwards (Fig. 10/3) and
connect them by pressing the top corners and
outer sides together. When the retaining pins
engage, you should be able to hear 2 clear clicks
on each side (Fig. 10/4).
n
When the top corners of the welding screen are
connected as shown in Figure 11, place the
screws for the handle (p) from the outside
through the three holes in the welding screen.
(Fig. 12).
n
Turn over the welding screen and place the
handle (r) over the threads on the three screws
for the handle (p). Secure the handle (r) to the
welding screen using the three nuts for the
handle (o). (Fig. 13).
5.2 Mains connection
n
Before you connect the equipment to the mains
supply make sure that the data on the rating
plate are identical to the mains data.
n
The equipment may only be operated from
properly earthed and fused shock-proof sockets.
5.3 Fitting the wire spool (Fig. 1, 2, 3, 14 – 22)
The wire spool is not supplied.
5.3.1 Wire types
Various welding wires are required for different
applications. The welding set can be used with
welding wires with a diameter of 0.9 mm. The
appropriate feed rollers and contact tubes are
supplied with the set. The feed roller, contact tube
and wire cross-section must always match each
other.
5.3.2 Wire spool capacity
Wire spools with a maximum weight of 0.4 kg can be
fitted in the welding set.
5.3.3 Inserting the wire spool
n
Unlock the housing cover (Fig. 1/3) by turning
the fastening screw (Fig. 6/12) through 90° and
flip open the cover.
n
Check that the windings on the spool do not
overlap so as to ensure that the wire can be
unwound evenly.
Description of the wire guide unit (Fig. 14-22)
A Wire
spool
B Spool
holder
C Guide
tube
D Adjusting screw for roller brake
E Screws for feed roller holder
F Fee roller holder
G Feed
roller
H Hose package mounting
I Pressure
roller
J
Pressure roller holder
K Pressure roller spring
L
Adjusting screw for counter-pressure
Inserting the wire spool (Fig. 14, 15)
Place the wire spool (A) on the spool holder (B).
Ensure that the end of the welding wire is unwound
on the side of the wire guide, see arrow.
Inserting the welding wire and adjusting the wire
guide (Fig. 16-22)
n
Push the pressure roller spring (K) upwards and
swing it forwards (Fig. 16).
n
Pull the pressure roller holder (J) with the
pressure roller (I) and pressure roller spring (K)
downwards (Fig. 17).
n
Undo the screws for the feed roller holder (E)
and pull off the feed roller holder (F) upwards
(Fig. 18).
n
Check the feed roller (G). The appropriate wire
thickness must be specified on the top of the
feed roller (G). The feed roller (G) is fitted with
Anleitung_BT_FW_100_GB_SPK7__ 13.03.13 13:12 Seite 11