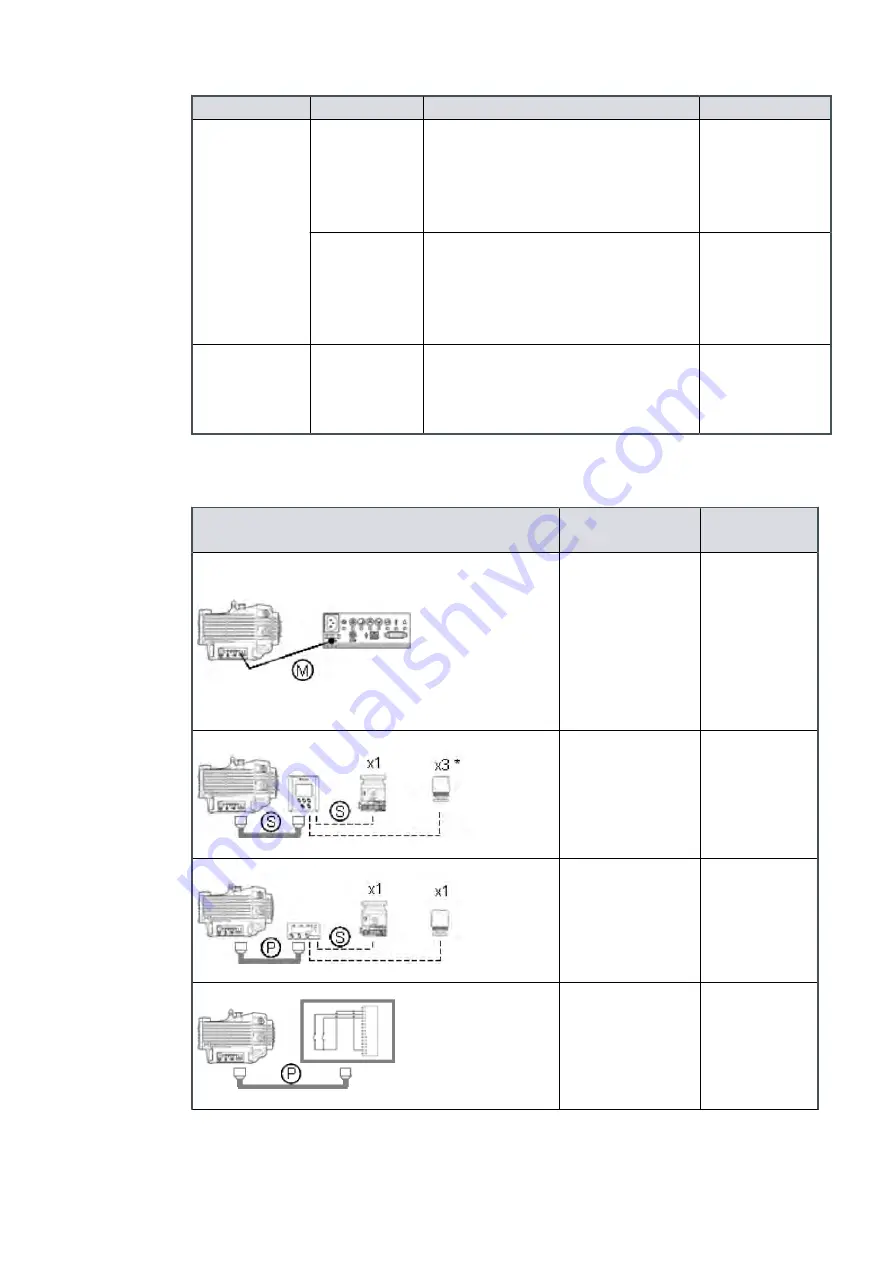
OPERATION
SELECT
STATUS
SECTION
Increase or
decrease the
pump speed
when in
standby mode
STANDBY
SPEED
INCREASE
BUTTON
The pump speed will increase.
The INCREASE STANDBY INDICATOR
will remain illuminated when the
pump reaches a maximum of 100% of
full speed.
STANDBY
SPEED
DECREASE
BUTTON
The pump speed will decrease.
The DECREASE STANDBY INDICATOR
will remain illuminated when the
pump reaches a minimum of 67% of
full speed.
Select and
deselect the
Auto
‑
run
function
START or STOP
BUTTON
(>8 sec)
When engaged, the AUTO
‑
RUN
INDICATOR will illuminate. The pump
will re
‑
start automatically after the
power has been restored.
* The pump is set to 30 Hz rotational full speed (factory default).
Table 1
nXDS Control modes
Configuration
Control mode
Manual/
Section
Manual control via
nXDS user
interface
in this manual
Serial control via
(TIC) *Turbo
Instrument
Controller or
Turbo Controller
Manual
D39722880
Parallel control via
(TAG) Turbo &
Active Gauge
Controller
Manual
D39592880
Parallel control via
Digital I/O e.g. PLC
control
in this manual
Page 13
A73501880_G - Introduction
Summary of Contents for nXDS10i nXDS15i
Page 57: ...Page 55 A73501880_G Service ...
Page 58: ...edwardsvacuum com ...