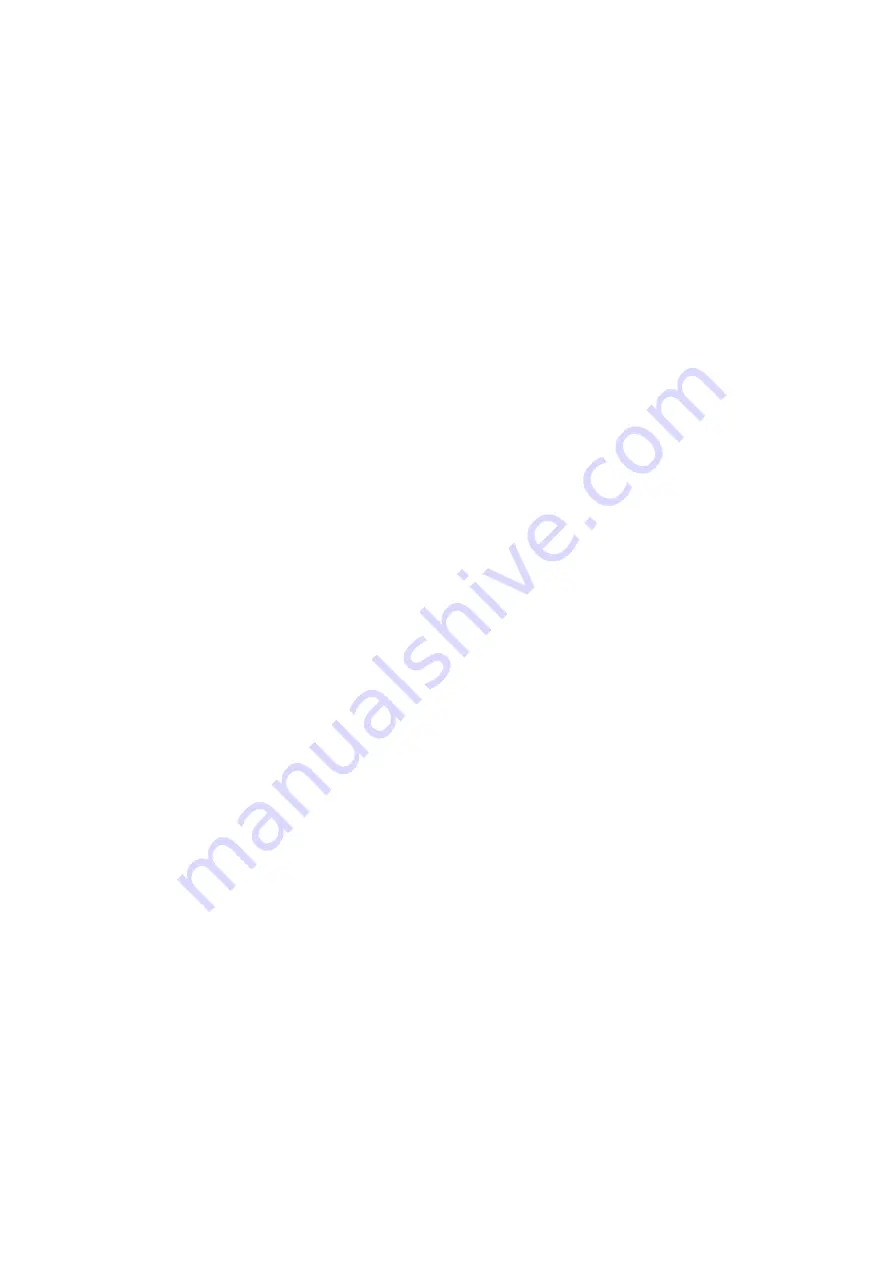
▪
Install the pump on a solid, level surface, suitable for taking its weight. Respect the
minimal distance between the pump and the walls (Refer to
on page 22).
▪
Correct process lines sizes must be used to prevent restrictions and resulting
pressure drops. The inlet diameter of the pump should be maintained as far into
the process as possible. Contact us for piping recommendations.
▪
The required ventilation capacity to limit the vacuum pump room temperature can
be calculated from Qv = 0.2 N/
D
t, with:
▪
Qv = required ventilation capacity in m
3
/s
▪
N = shaft input of the vacuum pump in kW.
▪
D
t = temperature increase of the incoming ventilation air in the vacuum
pump room in °C
▪
Make sure all piping connections from the pump to the point of use are leak
‑
tight
and secure. Leaks add load to the vacuum pump. They decrease the available
pump capacity and prevent the attainable ultimate pressure from being reached.
All welds must be vacuum compatible.
▪
Vacuum rated isolation valves must be used. Compressed air valves and vacuum
valves differ in their sealing characteristics and compressed air valves may leak in
vacuum applications.
▪
All piping should be as straight as possible with non-restrictive diameters. Elbows,
bends, tees and tapers should be used only when necessary.
▪
Keep the plumbing and the system free of fluids, water, dirt, and debris that are
not part of the process. These can cause obstructions in the vacuum flow through
the piping and can reduce available pumping capacity.
▪
Exhaust piping should be installed to not create additional back pressure on the
vacuum pump. Also, the exhaust piping should be installed sloping away from the
vacuum pump.
▪
A recommended alternative is the use of a drip leg with drain point provision, to
prevent condensate from running back into the fluid reservoir.
▪
Take extreme care in selecting the proper inlet filtration system for the vacuum
pump. Liquids, solids and abrasive powders must be prevented from entering the
vacuum pump to prevent mechanical failure or reduced lifetime. Inlet filtration
must be installed on every pump. The potential for particulate contamination in
rough vacuum applications is significant. The particle micron retention of the filter
element must be smaller than the smallest possible particle load. Also, the inlet
filter should be mounted in such a way to prevent particles from falling into the
inlet of the vacuum pump during cleaning or changing of the filter element.
▪
If there is a risk for liquids to be drawn into the vacuum system, a liquid separator
should be used to separate these liquids from the incoming air. In applications
where there is a significant amount of liquid, contact us.
▪
Keep the vacuum pump room dry and free from contamination.
▪
Follow recommended lubricant change schedules in normal applications (air) and
watch closely the condition and appearance of the fluid in chemical or harsh
applications. Check the leak rate of the system by pumping down to the ultimate
pressure and then valve off the vacuum pump. Monitor the pressure rise for five or
ten minutes and record this rate of rise for future reference. This value is a good
tool to have if you believe there are pump or system problems. Compare new
value with the original.
07/2020 - Page 29
A35104880_B - Installation
Summary of Contents for nES Series
Page 5: ...This page has been intentionally left blank...
Page 6: ...This page has been intentionally left blank...
Page 55: ......
Page 56: ...edwardsvacuum com...