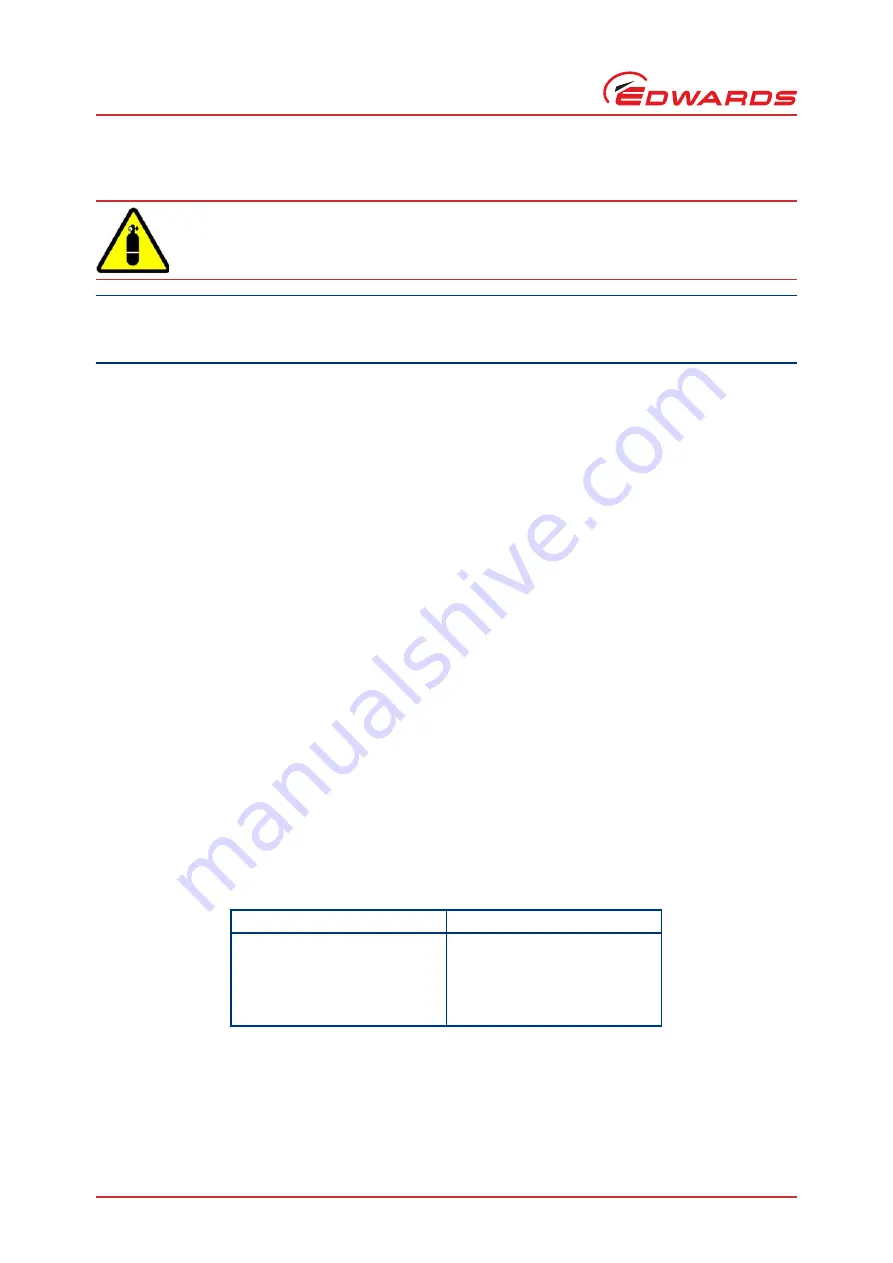
B756-50-880 Issue C
Page 10
© Edwards Limited 2013. All rights reserved.
Edwards and the Edwards logo are trademarks of Edwards Limited.
INSTALLATION
3.3.2
Backing connection
CAUTION
Do not use the EXT70/70/200H pump with a backing pressure below 5 x 10
-4
mbar (5 x 10
-2
Pa). Lower backing
pressures will increase the evaporation rate of the lubricating oil and may reduce the life of the bearings.
Use suitable vacuum tubing and connectors to connect the NW25 flange of the backing port to the backing pump. If
necessary, use flexible pipe or bellows to reduce the transmission of vibration from the backing pump to the EXT70/
70/200H Split Flow pump.
Edwards recommends using an Edwards E2M28 rotary vane or XDS35I scroll backing pump. It may be necessary to use
a larger backing pump if the pump is run at a high inlet pressure. The EXT70/70/200H is also suitable for use with
diaphragm backing pumps, although the effect of higher backing pressure on the pump's performance and cooling
requirements should be noted (see
3.4
Vent options, vent valve connection and control
To maintain the cleanliness of the vacuum system, whenever the pump is switched off, vent the pump (or vacuum
system) when the speed of the EXT70/70/200H pump is between 100% and 50% of full rotational speed. At and above
50% of full rotational speed, the rotor spins fast enough to suppress any back streaming of hydrocarbon oil from the
backing pump. Venting may be accomplished by one of the following methods:
Use a TAV5 or TAV6 solenoid vent valve accessory (see
) in place of the manual vent valve.
Use a TAV5 or TAV6 solenoid vent valve connected to a convenient flange on the vacuum system.
Use an alternative valve, with appropriate restriction, connected to the vacuum control system.
If the pump is manually vented when it is at full rotational speed, and the rate of pressure rise is too high, the pump
life may be reduced. When using the manual vent valve supplied, it is recommended to either limit the vent or only
open the vent valve after the EXT70/70/200H pump speed has fallen to 50% of full rotational speed.
Do not vent via the backing line; this may lead to contamination. If venting into the vacuum system, select a point
upstream of the pump to prevent oil back streaming from the backing line.
gives an indication of the appropriate orifice size to be fitted to the vent valve for given vacuum system
volumes in order that the vent rate is kept within the limits given in
3.5
Electrical installation
The EXT70/70/200H pump should be electrically bonded to earth. Refer to the customer system fitting specifications
for further details.
WARNING
Vent dangerous gases and gas mixtures safetly. Do not expose personnel to these gases.
Table 3 - Vent restructure orifice diameter (with atmospheric pressure at the inlet of the vent valve)
Vacuum system volume (l)
Orifice diameter (mm)
< 20
< 1.0
< 10
< 0.7
< 5
< 0.5
< 2
< 0.35