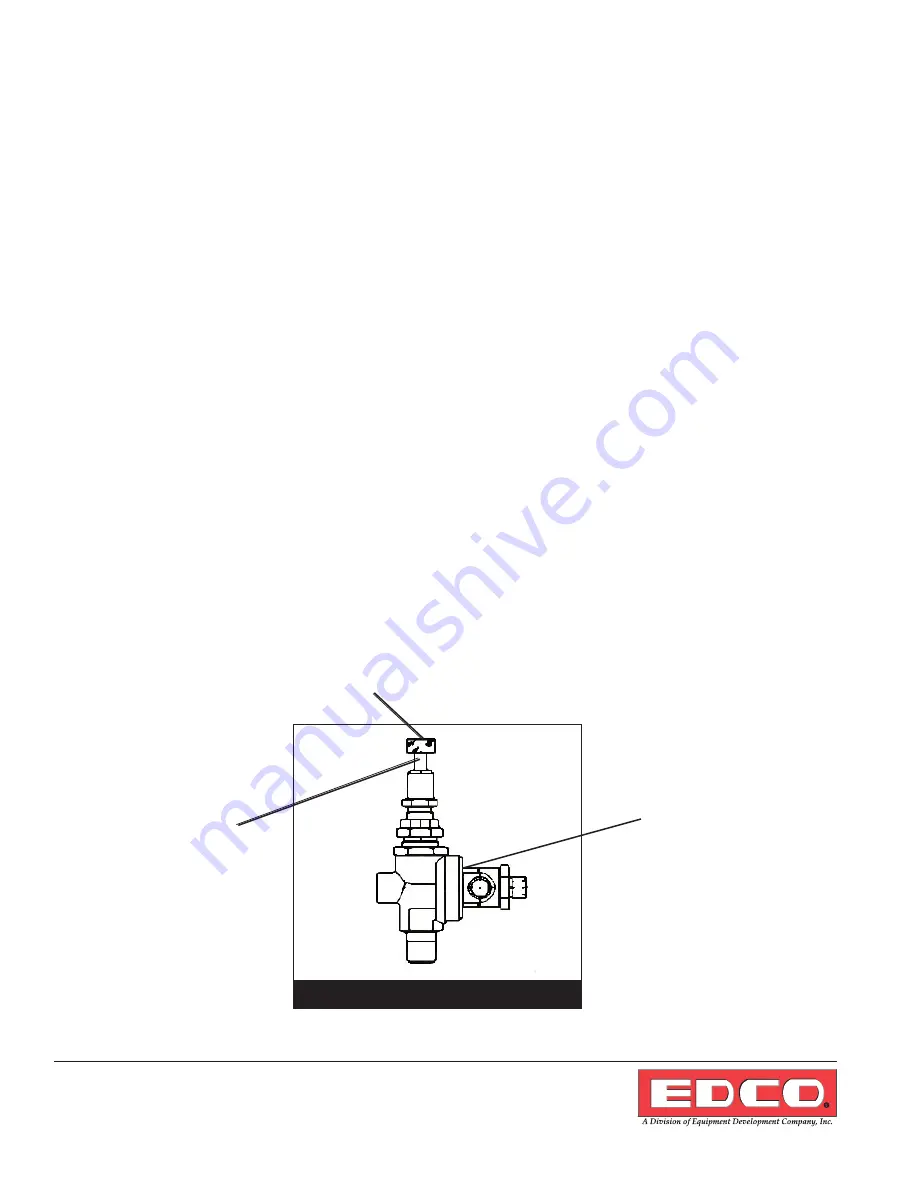
E-PAC5,8,1.5,HCP2-1008
Printed in USA
©2008
TVW
Page 6
100 Thomas Johnson Drive, Frederick, MD 21702-4600 USA
Phone (301) 663-1600 • 1-800-638-3326
Fax (301) 663-1607 • 1-800-447-3326
Website: www.edcoinc.com
Email: [email protected]
CONTROLS
START/STOP CONTROL (electric motor option only)
When the pressure in the air receiver reaches a designated low level, approximately 110 P.S.I.G. (drawing 9.9 Amps), the pres-
sure switch starts the motor. When the pressure in the air receiver reaches a designated high level, approximately 135 P.S.I.G., the
pressure switch stops the motor. Single stage compressors cut in at approximately 105 P.S.I.G. and cut out at approximately 125
P.S.I.G
.
NOTE: An electric motor should not be subjected to more than fi fteen (15) starts per hour. Damage to the
equipment will result.
CONSTANT SPEED CONTROL
The electric motor or gasoline engine is constantly running and the pump on the compressor is constantly pumping. When the
pressure in the air receiver reaches the designated high level, approximately 127 P.S.I.G., a pilot unloader valve will channel the
air being compressed into the atmosphere instead of into the air receiver. During this step, the motor or the engine, continues to
run (engine will idle). When the designated low pressure in the air receiver is reached, approximately 105 P.S.I.G. (drawing 9.9
Amps), the pilot unloader valve will redirect the air being compressed to the air receiver (the engine speed will return to the high
RPM level).
NOTE: All gasoline units must be built this way and any electrical units can be ordered with constant speed
control
.
DUAL CONTROL
Compressors can be equipped with both start-stop and constant speed controls. With this feature the operator can change the
control of the unit as their needs change from start-stop to constant speed. (See Figure 2).
COLD-STARTING PROCEDURE
Cold weather conditions present starting problems for air compressors. As operating temperatures decrease, the oil weight used in
the air pump must be thinned according to the OIL TYPE TABLE on page 7.
It is also necessary to remove the effects of the back pressure (load) on a cold motor. A drain cock is installed on the 90º “fi nned”
aftercooler as a means to eliminate the load. Open the aftercooler drain cock and allow the motor and the pump to run “unloaded”
for one to two minutes. Repeat the procedure if the motor continues to struggle.
Available on electric with
dual control option only.
Figure 2
FOR START/STOP:
Rotate thumbscrew
completely clockwise.
Pilot
Unloader
Valve
FOR CONSTANT SPEED:
Rotate thumbscrew completely
counter-clockwise.
Electric
models
only