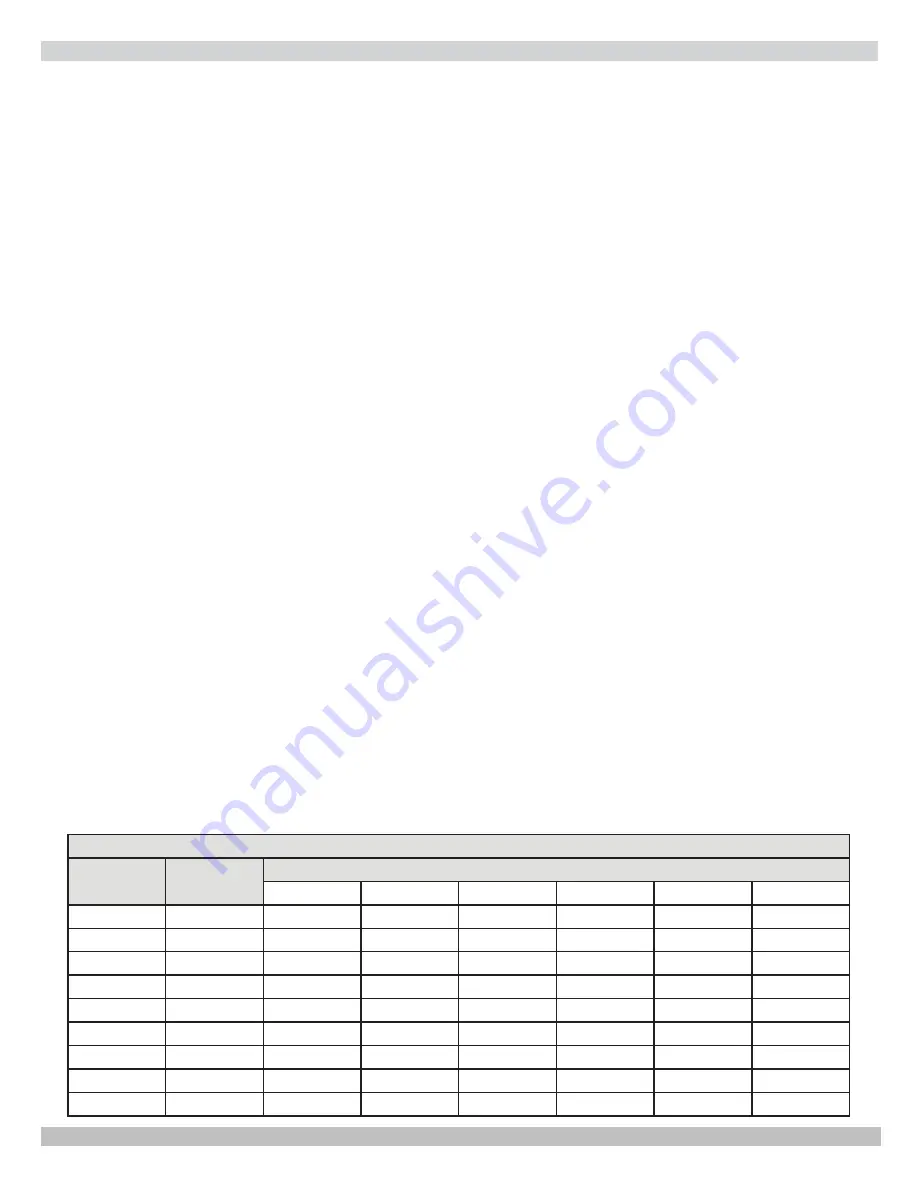
6
VENTILATION & COMBUSTION AIR
Provide combustion air and ventilation air in accordance
with the section “Air for Combustion and Ventilation,” of the
National Fuel Gas Code, ANSI Z223.1/NFPA 54, or Sections
8.2, 8.3 or 8.4 of Natural Gas and Propane Installation
Code, CAN/CSA B149.1, or applicable provisions of local
building codes.
Provide make-up air where exhaust fans, clothes dryers,
and kitchen ventilation equipment interfere with proper
operation.
National Fuel Gas Code recognizes several methods
of obtaining adequate ventilation and combustion air.
Requirements of the authority having jurisdiction may
override these methods.
Engineered Installations. Must be approved by
•
authority having jurisdictions.
Mechanical Air Supply. Provide minimum of 0.35
•
cfm per Mbh for all appliances located within space.
Additional requirements where exhaust fans installed.
Interlock each appliance to mechanical air supply
system to prevent main burner operation when
mechanical air supply system not operating.
All Indoor Air. Calculate minimum volume for all
•
appliances in space. Use a different method if
minimum volume not available.
Standard Method. Cannot be used if known air
о
infi ltration rate is less than 0.40 air changes per
hour. See Table 3 for space with boiler only. Use
equation for multiple appliances.
Volume
≥
50 ft
3
x Total Input [Mbh]
Known Air Infi ltration Rate. See Table 3 for
о
space with boiler only. Use equation for multiple
appliances. Do not use an air infi ltration rate
(ACH) greater than 0.60.
Volume
≥
21 ft
3
/ACH x Total Input [Mbh]
Refer to National Fuel Gas Code for opening
о
requirements between connection indoor spaces.
All Outdoor Air. Provide permanent opening(s)
•
communicating directly or by ducts with outdoors.
Two Permanent Opening Method. Provide opening
о
commencing within 12 inches of top and second
opening commencing within 12 inches of bottom
enclosure.
Direct communication with outdoors or
communicating through vertical ducts. Provide
minimum free area of 1 in
2
per 4 Mbh of total
input rating of all appliances in enclosure.
Communicating through horizontal ducts.
Provide minimum free area of 1 in
2
per 2
Mbh of total input rating of all appliances in
enclosure.
One Permanent Opening Method. Provide opening
о
commencing within 12 inches of top of enclosure.
Provide minimum clearance of 1 inch on sides
and back and 6 inches on front of boiler (does not
supersede clearance to combustible materials).
Combination Indoor and Outdoor Air. Refer to
о
National Fuel Gas Code for additional requirements
for louvers, grilles, screens and air ducts.
Combination Indoor and Outdoor Air. Refer to
•
National Fuel Gas Code for application information.
National Gas and Propane Installation Code Requires pro-
viding air supply in accordance with:
Section 8.2 and 8.3 when combination of appliances
•
has a total input of up to and including 400 Mbh (120
kW).
Section 8.4 when combination of appliances has total
•
input exceeding 400 Mbh (120 kW).
Refer to Natural Gas and Propane Installation Code
•
for specifi c air supply requirements for enclosure
or structure where boiler is installed, including air
supply openings and ducts.
Table 3
Input Mbh
Standard
Method
Known Air Infi ltration Rate Method (Air Changes Per Hour)
0.1
0.2
0.3
0.4
0.5
0.6
50
2500
10500
5250
3500
2625
2100
1750
75
3750
15750
7875
5250
3938
3150
2625
100
5000
21000
10500
7000
5250
4200
3500
125
6250
26250
13125
8750
6563
5250
4375
150
7500
31500
15750
10500
7875
6300
5250
175
8750
36750
18375
12250
9188
7350
6125
200
10000
42000
21000
14000
10500
8400
7000
250
12500
52500
26250
17500
13125
10500
8750
300
15000
63000
31500
21000
15750
12600
10500