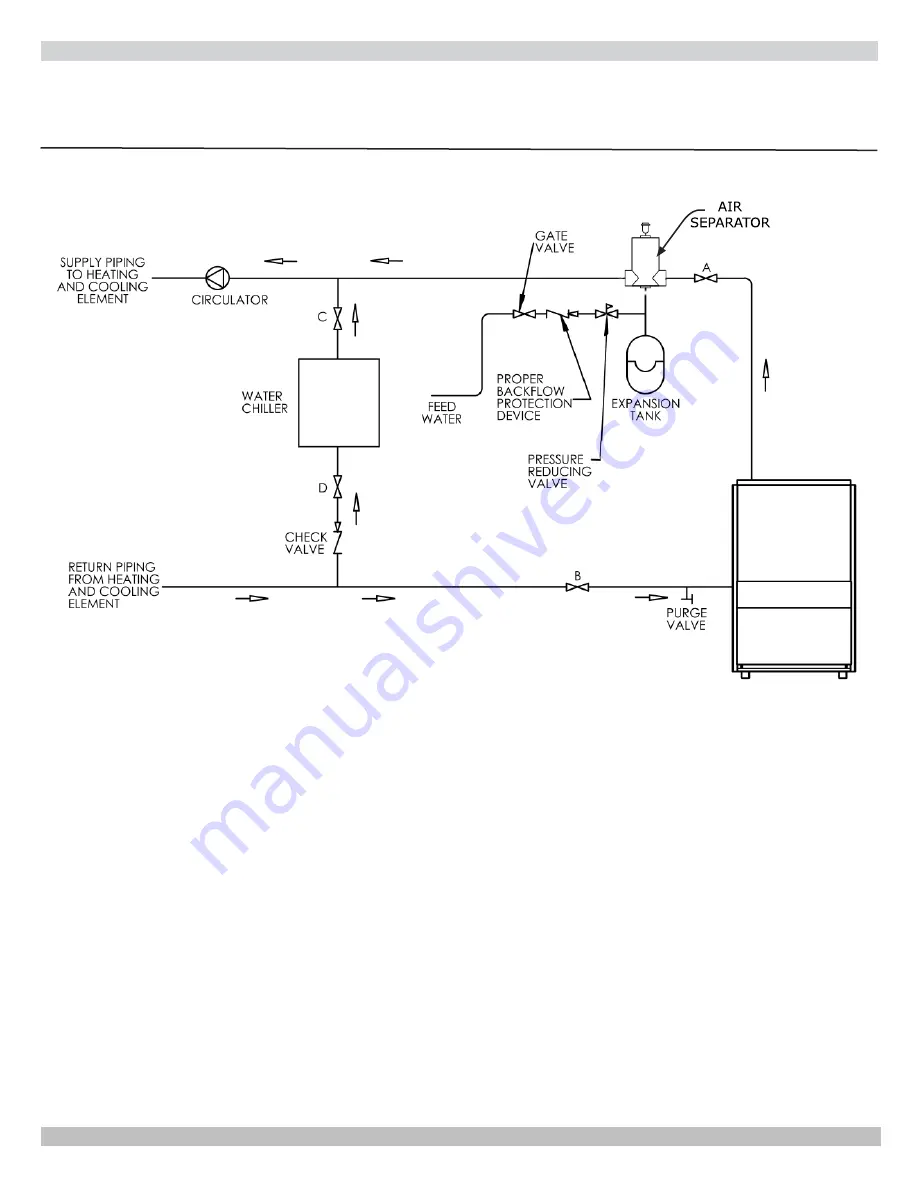
9
Circulators in following illustrations are mounted on system supply side, mounting on system return side is also accept-
able practice.
1.
Boiler used in connection with refrigeration system,
install so chilled medium is piped in parallel with boiler
with appropriate valves to prevent chilled medium from
entering boiler. See Figure 2.
2.
Boiler piping system of hot water boiler connected to
heating coils located in air handling units where they
may be exposed to refrigerated air circulation must be
equipped with
fl
ow control valves or other automatic
means to prevent gravity circulation of boiler water
during cooling cycle.
3.
Hot water boilers installed above radiation level or
as required by authority having jurisdiction must be
provided with low water cut-off device.
4.
Boiler connected to heating system utilizing multiple
zoned circulators, each circulator must be supplied with
fl
ow control valve to prevent gravity circulation.
5.
Hot water boilers and system must be
fi
lled with water
and maintained to minimum pressure of 12 psi.
6.
Bypass piping is optional which gives ability to
adjust supply boiler water temperature to
fi
t system
or condition of installation. This method of piping,
however, is not typically required for baseboard heating
systems. Typical installations where bypass piping is
used are as follows:
A. This method is used to protect boilers from
condensation forming due to low temperature
return water. Generally noticed in large converted
gravity systems or other large water volume
systems. Figures 4 and 5
.
B. These methods are used to protect systems using
radiant panels and material they are encased in
from high temperature supply water from boiler
and protect boiler from condensation.
NOTE#1:
When using bypass piping, adjust
valves V1 & V2 until desired system temperature
is obtained. See Figure 5, page 9.
NOTE#2:
Bypass loop must be same size piping
as supply and return piping.
4 - CONNECTING SUPPLY AND RETURN PIPING
Figure 3 - Circulators Mounted on Supply System, Boiler Used In Confi guration with Chiller System.
See Special Conditions, Page 9
Summary of Contents for Olsen OMGB II Series
Page 18: ...18 10 WIRING DIAGRAM Figure 14 Integrated High Limit Electronic Ignition Control 240008781 ...
Page 19: ...19 10 WIRING DIAGRAM Figure 15 Integrated High Limit Electronic Ignition Control 240008781 ...
Page 29: ...NOTES ...
Page 30: ...NOTES ...
Page 31: ...Date Service Performed Company Name Tech Initials Company Address Phone ...
Page 32: ...ECR International 2201 Dwyer Avenue Utica NY 13501 web site www ecrinternational com ...