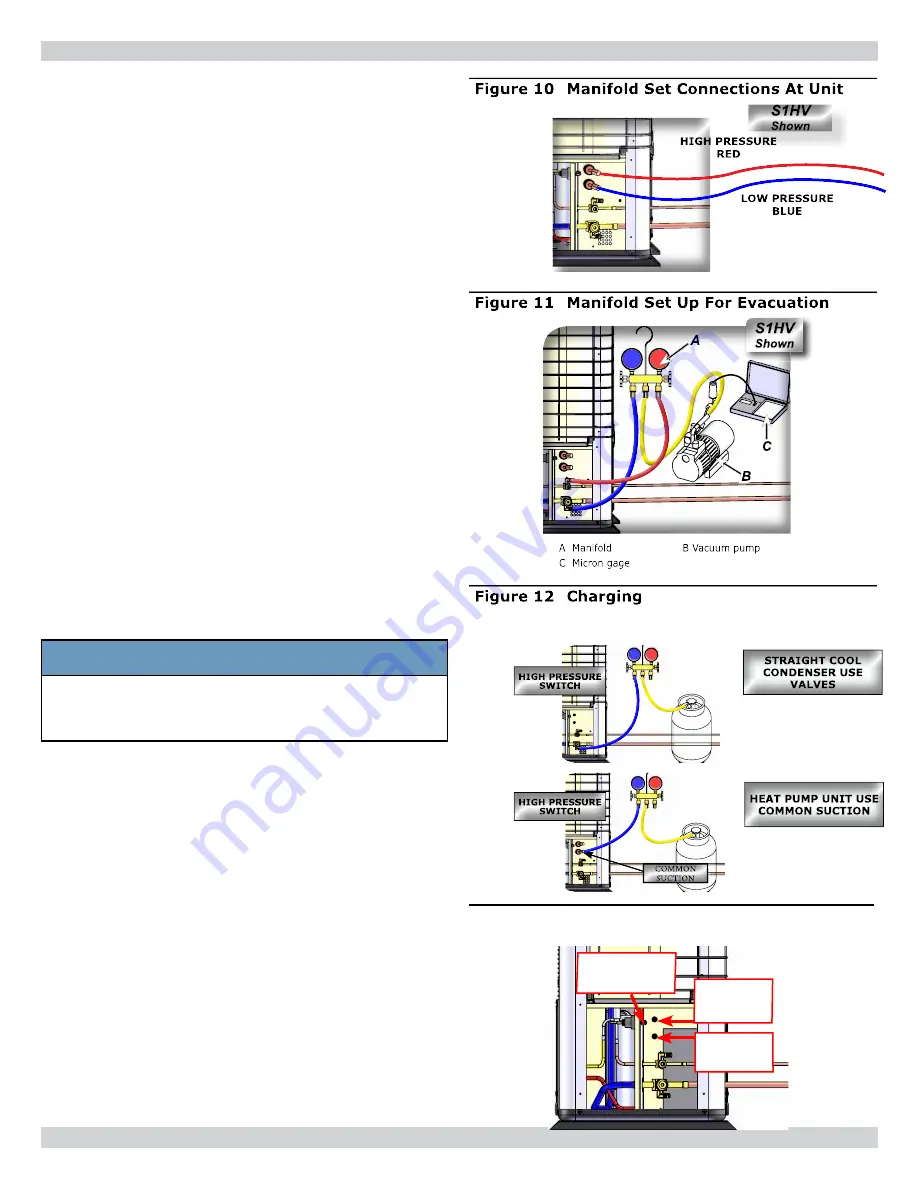
13
RefRIgeRANT PROCeSSINg
Refrigerant Processing
1.
Attach manifold set, vacuum pump, & Micron Gauge.
See Figure 10.
2.
Evacuate line to 500 microns or less to insure all
moisture has been removed and there are no leaks.
See Figure 11.
A.
Evacuate
B.
Pressurize with 100psi N2 or Nitrogen
C.
Evacuate again
D.
Charge with R410A
3.
verify evacuation and leak free joints. Back-seat valves
(counter-clockwise) to open and allow factory charge to
fill lines and indoor unit. See Figure 13.
Refer to refrigerant charge table for specified charge.
4.
Charge to proper weight. Charge based on feet of
interconnect.
Only add/remove R410A in liquid
form
. See
Table 5, Page 14
.
5.
Install all panels removed to this point. Panels are re
-
quired for proper air flow.
All systems require field charge adjustments. Refer to
“Refrigerant Charge Tables” for proper weight charge
and Operation Charts for proper system pressures and
temperatures at different outdoor conditions. Sub-cool
should be used for final system charge.
Charge with dial-a-charge or weighed in with scale.
NOTICe
It is illegal to discharge refrigerant into the
atmosphere. Use proper reclaiming methods &
equipment when installing or servicing this unit.
Units are delivered pre-charged with refrigerant for
condenser coil and air handler. Charging of field installed
piping is required. Refer to refrigerant charge table for
proper amount to be added for applications interconnect
piping. Unit service valves are solid brass, for sweat
connections.
• Measure all heat pump saturated suction pressures at
Common Suction Port
not vapor service valve.
• Common Suction Port
includes pressure drop and
temperature increase through reversing valve resulting
in more accurate and complete system charge.
• Port may also be used to charge system in heating
mode when both sides of line set are at high system
pressures or to determine saturated evaporator
pressure while in heating mode.
figure 13 Common Suction, Common
Discharge, & High pressure Switch
COMMON
DISCHARge
PORT
HIgH PReSSURe
SWITCH
COMMON
SUCTION
PORT