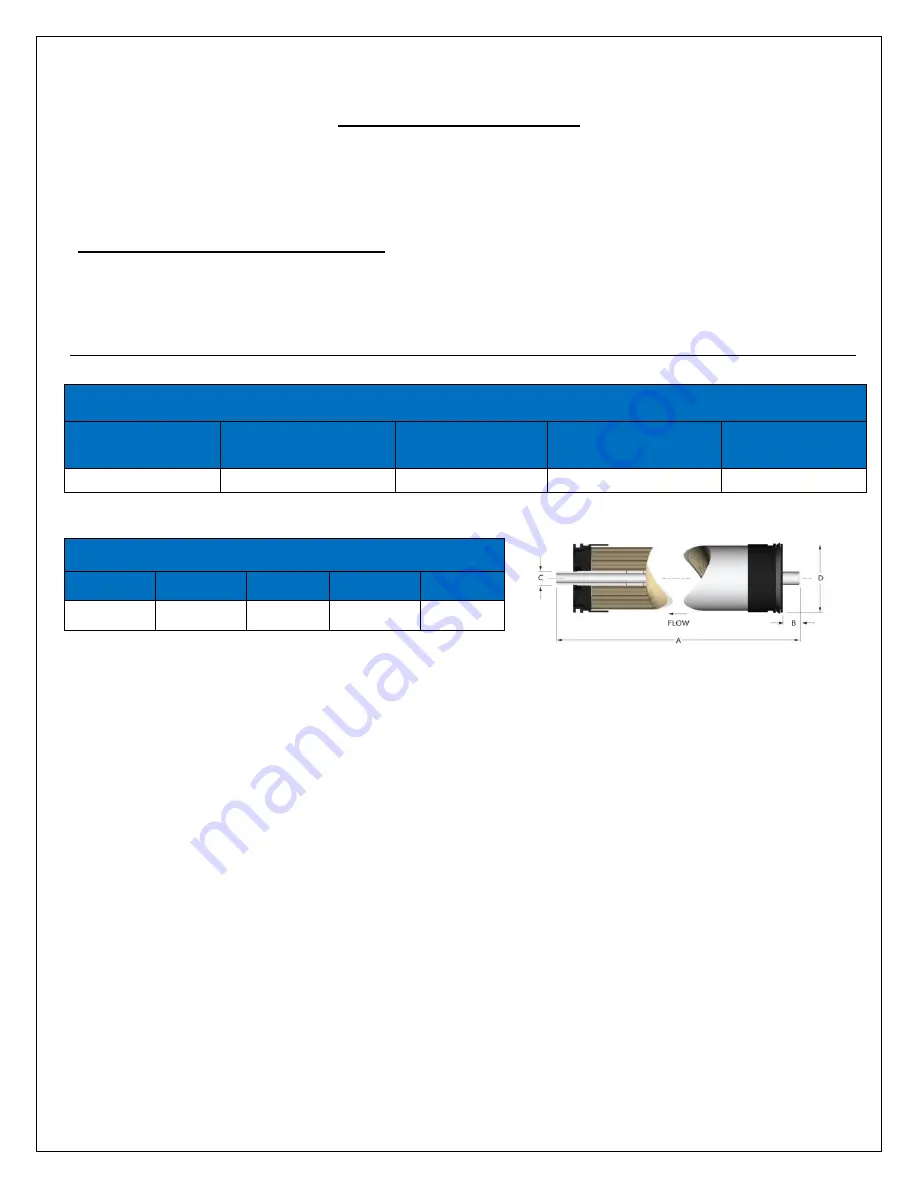
ELC
– Series User Manual
MKTF
– 506-A
10
03/18
MEMBRANE ELEMENTS
ELC
– Series Reverse Osmosis Systems are equipped with Thin Film Composite (TFC) HF5
– Ultra Low Energy membranes, unless otherwise specified. General membrane element
performance characteristics are listed below.
HF5
– Ultra Low Energy Membranes
▪
Membrane Type
: Polyamide Thin
– Film Composite
▪
pH Range, Short Term Cleaning (30 Min.)
: 1
– 13
▪
Maximum Operating Temperature
: 113°F
▪
Maximum Feed Silt Density Index (SDI)
: 5
▪
Maximum Operating Pressure
: 400 psi
▪
Chlorine Tolerance
: 0 ppm
▪
pH Range, Continuous Operation*
:
2
– 11
▪
Maximum Feed Flow Rate (gpm)
: 2.5” = 6; 4.0” = 16
*Maximum temperature for continuous operations above pH10 is 95°F (35°C).
Product Specifications
Part Number
Description
Applied
Pressure (psi)
Permeate Flow
Rate (gpd)
Nominal Salt
Rejection (%)
209175
HF5
– 3018
80
750
98.5%
Warranty Evaluation Test Conditions:
Permeate flow and salt rejection based on the following test conditions
– 550 ppm, filtered and dechlorinated municipal tap water, 77°F / 25°C, 15% recovery
and the specified operating pressure. Minimum salt rejection is 96%. Permeate flows for warranty evaluation may vary +/-20%. Maximum pressure drops at 13 psi / 0.9 bar.
Dimensions inch / mm
Description
A
B
C
D
HF5
– 3018
19.75
0.98
0.745
3.00
Proper start
–up of reverse osmosis water treatment systems is essential to prepare the membranes for operating service and to prevent membrane damage due to
overfeeding or hydraulic shock. Before initiating system start
–up procedures, membrane pretreatment, loading of the membrane elements, instrument calibration
and other system checks should be completed.
Avoid any abrupt pressure or cross
–flow variations on the spiral elements during start–up, shutdown, cleaning or other sequences to prevent possible membrane
damage. During start
–up, a gradual change from a standstill to operating state is recommended as follows:
▪
Feed pressure should be increased gradually over a 30
– 60 second time frame.
▪
Cross
–flow velocity at set operating point should be achieved gradually over 15 – 20 seconds.
▪
Permeate obtained from first hour of operation should be discarded.
▪
Maximum pressure drops across an entire pressure vessel (housing) is 30 psi / 2.1 bar.
▪
Avoid static permeate
–side backpressure at all times.
Under certain conditions, the presence of free chlorine, chloramines and other oxidizing agents will cause premature membrane failure. Since oxidation damage is
not covered under warranty, the manufacturer recommends removing all oxidizing agents by pretreatment prior to membrane exposure. Please contact the
manufacturer or your supplier for more information.
Do not use this initial permeate for drinking water or food preparation. Keep elements moist at all times after initial wetting. To prevent biological growth during
prolonged system shutdowns, it is recommended that membrane elements be immersed in a preservative solution. Rinse out the preservative before use. For
membrane warranty details, please contact the manufacturer or your supplier for more information.
If operating limits and guidelines given in this product specification sheet are not strictly followed, the warranty will be null and void. The customer is fully responsible
for the effects of incompatible chemicals and lubricants on elements. Use of any such chemicals or lubricants will void the warranty. These membranes may be
subject to drinking water application restrictions in some countries: please check the application status before use and sale. The use of this product in and of itself
does not necessarily guarantee the removal of cysts and pathogens from water. Effective cyst and pathogen reduction is dependent on the complete system design
and on the operation and maintenance of the system.
No freedom from infringement of any patent owned by the manufacturer or others is to be inferred. Because use conditions and applicable laws may differ from one
location to another and may change with time, customer is responsible for determining whether products and the information in this document are appropriate for
customer’s use and for ensuring that customer’s workplace and disposal practices are in compliance with applicable laws and other governmental enactments. The
claims made may not have been approved for use in all countries. The manufacturer assumes no obligation or liability for the information in this document. NO
WARRANTIES ARE GIVEN; ALL IMPLIED WARRANTIES OF MERCHANTABILITY OR FITNESS FOR A PARTICULAR PURPOSE ARE EXPRESSLY
EXCLUDED.
Summary of Contents for ELC-1500
Page 1: ...Membrane System User Manual ELC Series ELC 1500 w...
Page 2: ...ELC Series User Manual MKTF 506 A 2 03 18 This page intentionally left blank...
Page 11: ...ELC Series User Manual MKTF 506 A 11 03 18 SYSTEM IDENTIFICATION Figure 1...
Page 15: ...ELC Series User Manual MKTF 506 A 15 03 18 Figure 2...
Page 16: ...ELC Series User Manual MKTF 506 A 16 03 18 Figure 3...
Page 26: ...ELC Series User Manual MKTF 506 A 26 03 18 OPERATING LOG...
Page 30: ...ELC Series User Manual MKTF 506 A 30 03 18 ELC 750 FLOW DIAGRAM...
Page 31: ...ELC Series User Manual MKTF 506 A 31 03 18 ELC 1500 FLOW DIAGRAM...
Page 32: ...ELC Series User Manual MKTF 506 A 32 03 18 ELC SERIES ELECTRICAL SCHEMATIC...