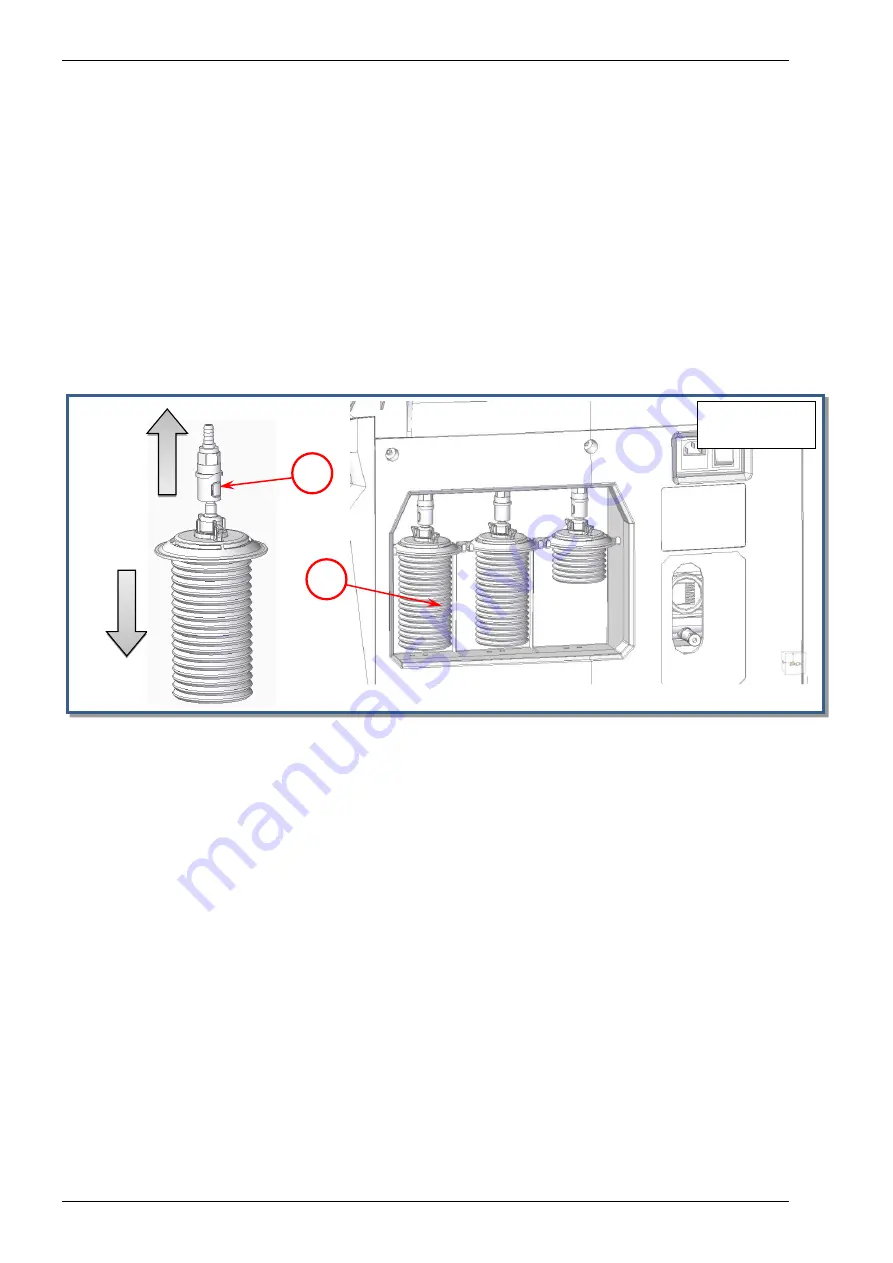
INSTRUCTIONS MANUAL
-96-
1
FIG. 30
b
REPLACE THE NEW OIL CARTRIDGE (PAG)
when the new / tracer oil level drops to a few ml it is preferable to replace the collapsible
cartridge in order to have sufficient reserve.
Types of oil: use only oils recommended by the manufacturer. Always refer to the
information provided by the manufacturer of the A / C system.
Procedure:
1. press the quick coupling button (ref 1, Fig.30) and disconnect the oil container
OIL cartridge (ref j, Fig.30);
2. remove the cartridge from its housing
1. Insert the male insert of the new oil cartridge into the quick connection and replace the
cartridge in its housing.
NOTE
: Store the cartridge, taking care not to exert too much pressure on the scale so as
not to damage it.
Summary of Contents for ECK FLAG
Page 1: ......
Page 23: ...INSTRUCTIONS MANUAL 24 FIG 8 p 9 g 8 FIG 9 s v u i w t...
Page 24: ...INSTRUCTIONS MANUAL 25 l FIG 10 k c d e 1 b f j v q r x...
Page 25: ...INSTRUCTIONS MANUAL 26 FIG 11 n o 2 m a y z...
Page 26: ...INSTRUCTIONS MANUAL 27 FIG 12 4 3 6 5 h 7...
Page 101: ...INSTRUCTIONS MANUAL 102 CODES SUMMARY OPTION code 43210791...
Page 102: ...MANUEL D INSTRUCTIONS 2...