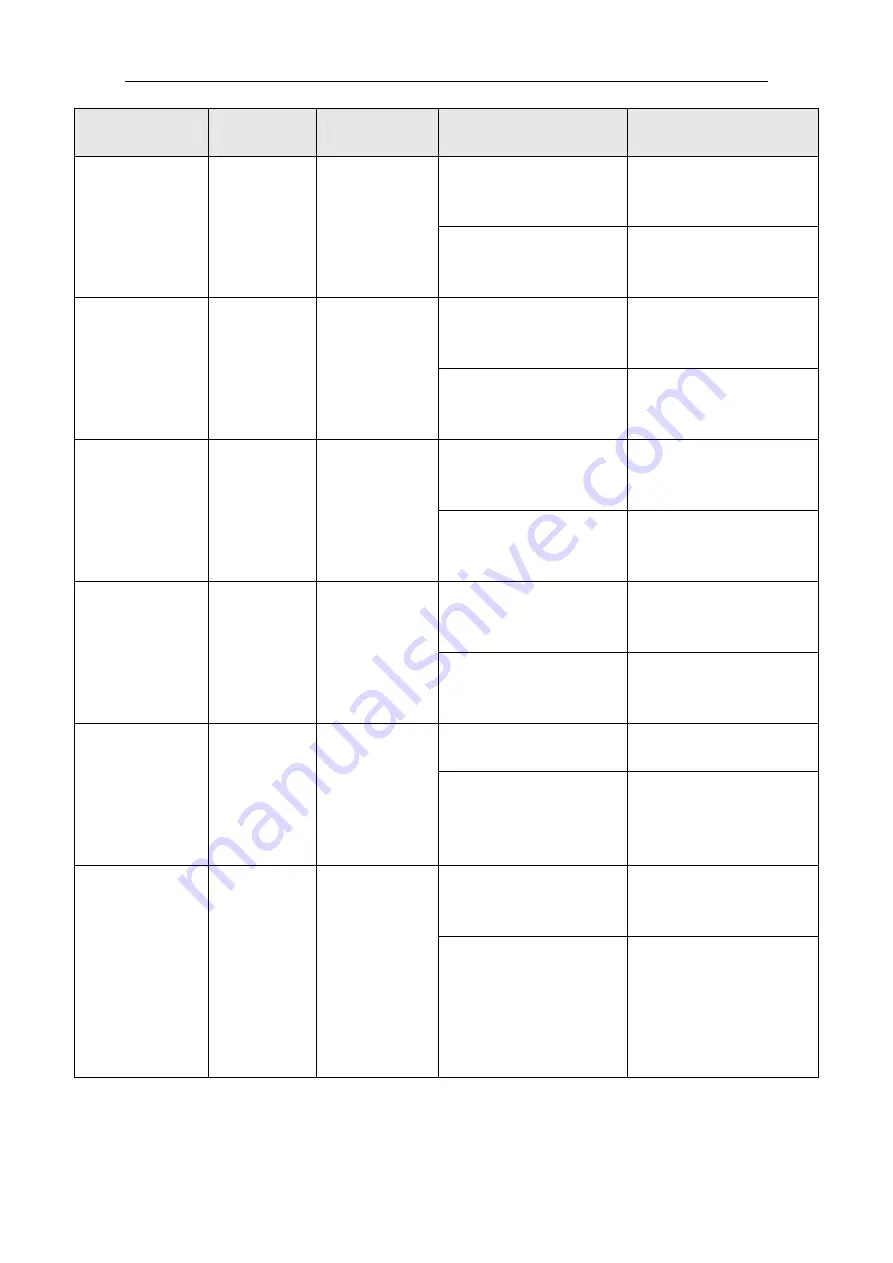
- 27 -
Malfunction cause
Malfunction
code
Safeguard
Enter condition
Resume condition
Circuit board temperature
probe is not inserted well
or loose
Re-insert temperature
probe
Damaged outlet
water temperature
sensor
E1
:
11
the unit stopped
Temperature probe is
damaged
Replacement of the
corresponding temperature
probe
Circuit board temperature
probe is not inserted well
or loose
Re-insert temperature
probe
Damaged
backwater
temperature
sensor
E1
:
12
the unit stopped
Temperature probe is
damaged
Replacement of the
corresponding temperature
probe
Circuit board temperature
probe is not inserted well
or loose
Re-insert temperature
probe
Damaged air
temperature
sensor
E1
:
13
the unit stopped
Temperature probe is
damaged
Replacement of the
corresponding temperature
probe
Circuit board temperature
probe is not inserted well
or loose
Re-insert temperature
probe
Damaged Y# coil
temperature
sensor
E1
:
27
Y# compressor
stopped
Temperature probe is
damaged
Replacement of the
corresponding temperature
probe
Power supply phase
missing
Check power supply
Phase sequence
protection
E1
:
01
the unit stopped
External power supply
phase sequence error
External power supply to
replace any of the
three-phase two-phase
power supply wiring
Water flow switch is not
properly access electronic
control box
Check and join
water flow switch
off
E1
:
02
the unit stopped
Regulation of water flow
switch spring preload
adjustment is incorrect,
resulting in insufficient
water flow, but flow switch
does not close
To re-install the flow
switch