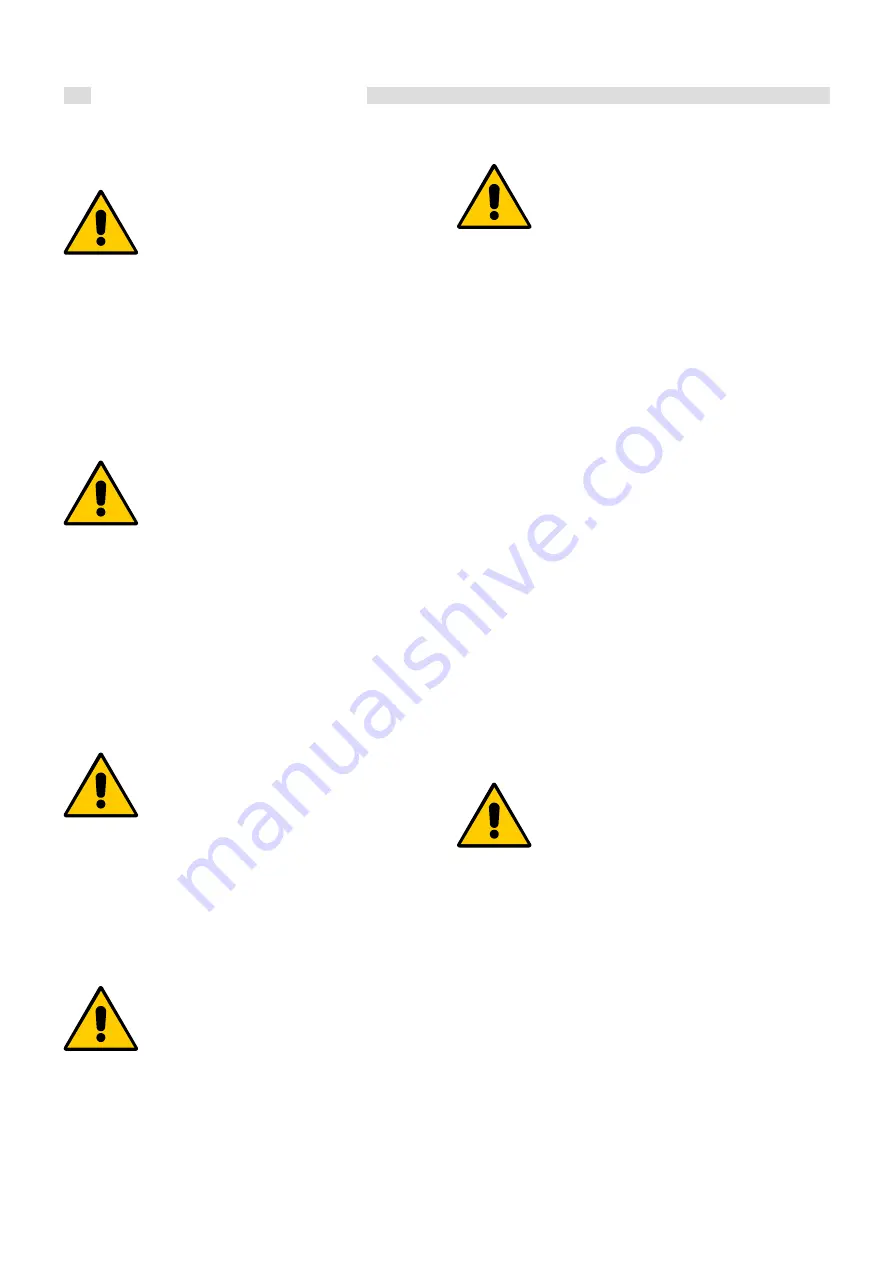
24
Installation instructions
3.9 - CONNECTING BOILER
TO SYSTEM
Attention!
Before connecting the boiler to the heating
system, thoroughly clean the piping with an
appropriate product in order to eliminate
metallic residue from processing and
welding, oil and grease which could be
present and which, reaching the boiler, could
alter its functioning.
Do not use solvents to wash the system as
they could damage the system and/or its
components.
Failure to comply with the instructions of
the following manual can cause damage to
persons, animals and objects for which the
manufacturer cannot be held responsible.
Attention!
Make sure that there are no mechanical
tension points while connecting the pipes to
avoid the risk of leakage!
Heating flow and return pipes must be connected to the boiler at
the respective fittings as indicated on pages 9, 10, 11, 12 and 14.
For the dimensioning of the heating circuit pipes, you must take
into account pressure drops caused by radiators, thermostatic
valves, radiator stopping valves and by the configuration of the
system.
The laying of the pipes must be designed taking every necessary
precaution to avoid air pockets and to facilitate continuous
degassing of the system.
Make sure that the pipes of the water and heating
system are not used as earthing electrodes of the
electric or telephone system. They are absolutely
not suitable for this type of use. Serious damage
could result for the piping, boiler and radiators in
a short amount of time.
Heating system safety valve discharge
Provide a drain pipe with a funnel and a siphon leading to an
appropriate drainage at the heating safety valve. This drainage
must be controlled on sight.
Attention!
If this precaution is not taken, triggering
of the safety valve can cause damage to
persons, animals and objects for which the
manufacturer cannot be held responsible.
Connection of expansion vessel
ECOMAX 3SC boilers are suitable for operating
with forced water circulation both with the
expansion vessel opened or closed.
An expansion vessel is always necessary to
compensate the increase in water volume due
to heating.
The connection pipes of the expansion vessel will start from the
T3 attachment (see DIMENSIONS TABLES) and must have no
shut-off valve.
Connecting the filling / draining tap
A specific tap can be connected to the T4 attachment at the rear
of the boiler for filling and draining.
3.9.1 - RECIRCULATION PUMP
ECOMAX 3SC boilers must always operate with forced water
circulation and a minimum return temperature of 55°C.
It is therefore recommended to use a recirculation pump, which
also has an anti-condensation function, installed between the
flow and return connections upstream the mixer valve.
This pump is dimensioned according to the formula:
Q = P x 22
where
Q
= Flow rate in l/hr
P
= Nominal output of boiler in kW
and
hydraulic head
1÷2 m H
O
3.10 - FILLING THE SYSTEM
Attention!
Do not mix the heating water with incorrect
concentrations of antifreeze or anti-corrosion
substances! This could damage the gaskets
and cause noise during operation.
Ecoflam will not be held liable for damage to
persons, animals or objects due to failure to
comply with the instruction above.
When all system connections have been completed, the circuit
can be filled.
This operation must be performed carefully, respecting the
following phases:
- open the radiator air release valves;
- open the filling tap gradually, making sure that the automatic
air release valves installed on the system work properly;
- close the radiator air release valves as soon as water comes
out;
- check the pressure gauge until pressure reaches
approximately 1 bar;
- close the filling tap and bleed air once again through the
radiator air release valves;
- make sure that all the connections are watertight;
Summary of Contents for ECOMAX 3SC 1000-N
Page 47: ......