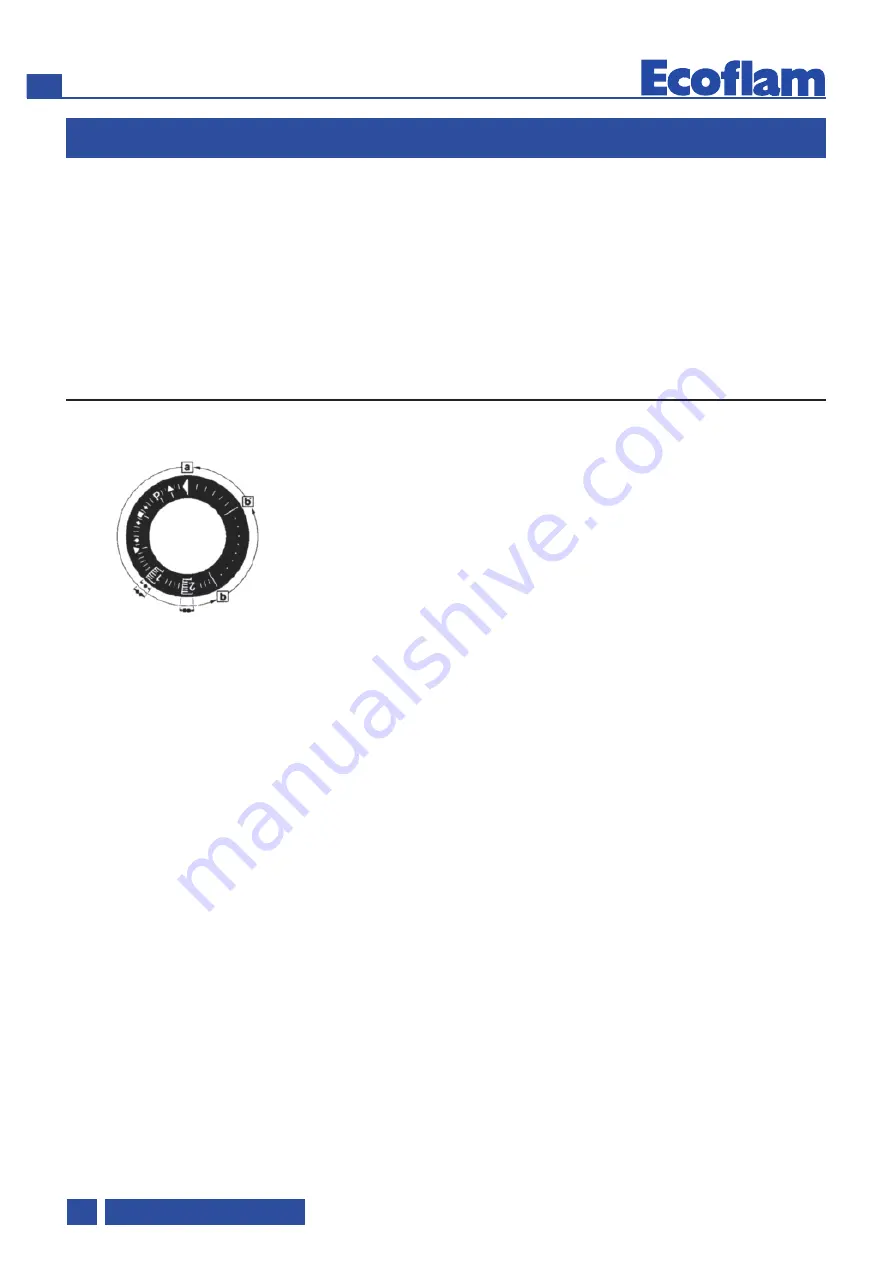
32
www.ecoflam-burners.com
EN
420010463703
OPERATING TROUBLE
In case of operating trouble it should be
checked whether the system is in proper
working order.
Make a check for the following:
1. Availability of fuel.
Availability of gas in the line at sufficiently
high pressure.
Availability of fuel oil in the tank (for dual
fuel burner).
Correct position of fuel selector switch.
2. Availability of electric power in the
burner system.
3. Proper functional order and setting of all
control and safety instruments such as
temperature controller, safety limiter, water
failure cut-out, electrical limit switches, etc.
If the trouble is not found to be due to any
of the above-mentioned points it will be
necessary to test the burner functions very
carefully.
Prevailing conditions:
The burner will be found to be out of
operation and in faulty and interlocked
position.
Proceed with searching for the cause of
the trouble and eliminate it. Unlock the
control box by pressing the fault eliminate
key and start the burner.
Do not press the fault eliminate key longer
than 10 seconds.
The start-up program will be initiated and
should be carefully monitored.
The possible cause of the fault may be
quickly found by reference to the fault
indicator of the control box and watching
the start-up and operating program.
Control program in the case of trouble
and fault indicator LFL 1... / LGK 16...
LFL 1... / LGK 16...
a-b
Starting program
b-b’
In a number of time versions; idle
steps of the program unit to self-stop after
burner start-up (b’ = operating position of
program unit)
b(b’)-a
After-flushing program after
regular stop. In the starting position “a” the
program unit will automatically stop or
initiate an immediate restart of the burner,
e.g. after a fault has been eliminated
• Duration of the safety period for single-
tube burners
•• Duration of the safety period for
burners with ignition gas valve
Basically, any type of trouble will result
in the immediate stop of the fuel supply.
At the same time, the program unit and
consequently the fault indicator will stop.
The type of trouble can be identified by the
symbol opposite to the reading mark of the
indicator:
◄
No start
, e.g. because the “CLOSED”
signal from the “Air Damper CLOSED” limit
switch is missing or a contact is not closed
between terminals (12) and (4) or (4) and
(5); or the contacts of all control and safety
units in the controlled system are not
closed (e.g. gas pressure or air pressure
switches, temperature or pressure
switches, temperature or pressure
regulators).
▲
Operating stop
because the “OPEN”
signal from the “Air Damper OPEN” limit
switch is missing.
Check and adjust the limit switch
concerned.
P Shut-off on trouble because there is
not air pressure
signal at the beginning of
the air pressure check.
Any air pressure failure after this time
will also lead to a shut-off on trouble.
■
Shut-off on trouble
because of a fault
in the flame monitoring circuit.
▼
Operating stop
because the position
signal of the “Partial Load” limit switch (air
damper in “Partial Load” position) is not
available on terminal (8). Check and adjust
the limit switch concerned.
1 Shut-off on trouble
because a flame
signal is not available on the expiry of the
(1st) safety time.
Any failure of the flame signal on the
expiry of the safety time will also lead
to a shut-off on trouble.
2 Shut-off on trouble
because the flame
signal has not occurred on the expiry of
the (2nd) safety time (flame signal of main
flame with burners having an ignition gas
valve).
| Shut-off on trouble
because the flame
signal failed during burner operation or a
lack of air has occurred.
◄
Shut-off on trouble
during or after the
control program flow due to external light
(e.g. by flame not extinguished, leaking
fuel valves) or a faulty flame signal (e.g.
fault in flame monitoring circuit, or similar);
see flame monitor.
If the shut-off on trouble occurs at any
other time between start and pre-
ignition that is not identified by a
symbol as above, this will normally be
due to an early flame signal which is
considered to be a faulty flame signal.
The control box may be unlocked
immediately after a shut-off on trouble
using the unlock button with integrated
fault signal lamp or an external switch.
After it has been unlocked (and after a
defect with resultant operating stop has
been eliminated and after a voltage
failure), the program unit will in any case
return to its starting position with voltage
being only supplied to terminals 7, 9, 10
and 11 as preset by the control program. It
is only at this stage that the program of the
control box will restart the
burner.
Summary of Contents for 3142132
Page 3: ...3 www ecoflam burners com EN 420010463703 CONFORMITY DECLARATION ...
Page 34: ...34 www ecoflam burners com EN 420010463703 APPENDIX Fluidics nozzle chart ...
Page 35: ...35 www ecoflam burners com EN 420010463703 APPENDIX Fluidics nozzle chart ...
Page 36: ...36 www ecoflam burners com EN 420010463703 APPENDIX Fluidics nozzle chart ...