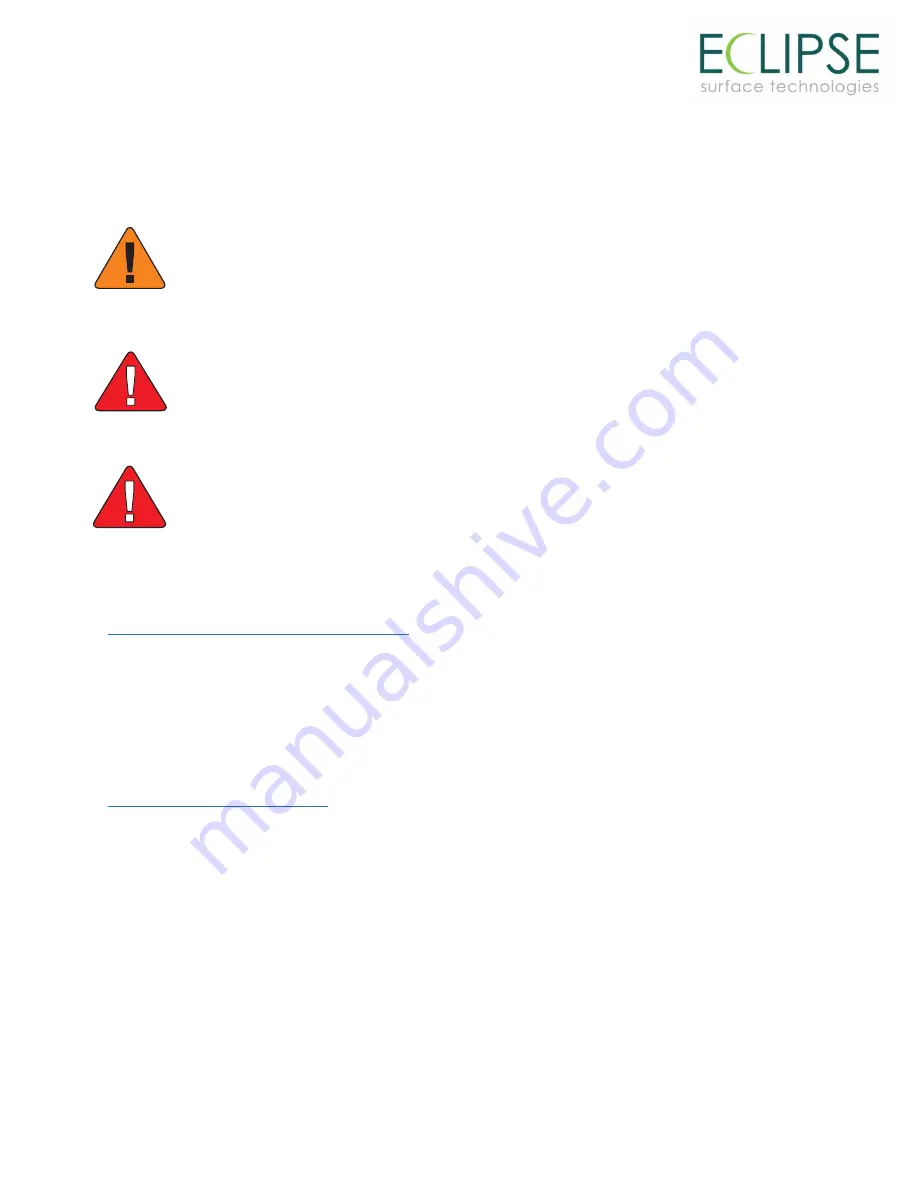
Page
6
of
23
SETTING UP THE ECO-100
WARNING
: The procedures provided in the Operating Procedures section of the
manual are designed to provide basic information on how to safely operate the
features of the ECO-Flex® ECO-100 Abrasive Blasters. Only personnel thoroughly
trained in abrasive blasting should operate the Abrasive Blaster.
DANGER
: Never perform any maintenance or attempt to open the Abrasive Blaster in
any way while it is pressurized. The violent release of compressed air and propelled
objects will cause serious injury or death.
DANGER
: Never perform any maintenance or attempt to open the Abrasive Blaster in
any way while it is pressurized. The violent release of compressed air and propelled
objects will cause serious injury or death.
Re-tighten Handway Assembly
After the Abrasive Blaster has been pressurized for the first time, tighten the nut on the Handway
Assembly. Tightening the nut on the Handway Assembly should also be done any time after the
handway has been removed for maintenance before and after the next pressurization.
Purge Air Supply Hose
Before connecting the Air Supply Hose to the Abrasive Blaster, purge the hose of any moisture or
foreign debris. Standing water or moisture in the airline will cause degraded performance of the
Abrasive Blaster. Air supplied to the Abrasive Blaster must be clean, dry and cool.
3-Stage ECO-Aire Air Drying System recommended and sold separately
1.
Connect air hose to (customer supplied) compressor. Treated (clean, cool, dry) air is required
to operate the ECO-100 properly. If compressor does not have an air-drying system built-in,
connect an
ECO-Aire Air Drying System
(sold separately).
Summary of Contents for ecoflex Eco-100 PRO
Page 17: ...Page 17 of 23 COMPRESSOR REQUIREMENTS ...
Page 23: ...Page 23 of 23 NOTES ...