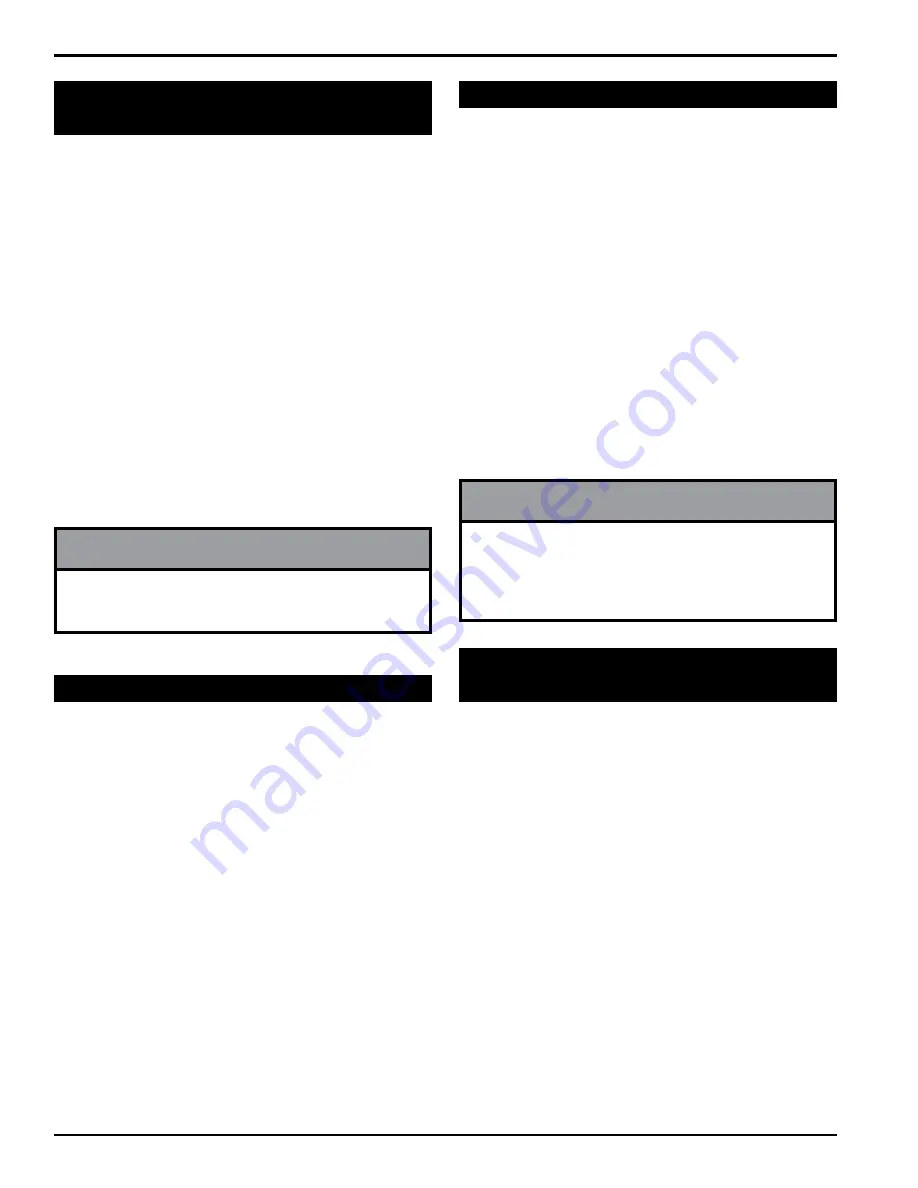
14
6 INCH CHIPPER
OPERATION
4.5 FEED ROLLER SPEED CONTROL
This machine is equipped with a flow control to vary
the speed of the feed roller. This allows the operator to
increase the feed speed when processing smaller material
and lower the speed when handling material close to the
maximum capacity of the machine. It is recommended that
operators start using the machine at the lower limits of the
speed control and slowly increase the speed, according
to the size and hardness of the material being chipped.
While occasional stopping and starting of the feed roller
is normal, frequent stopping and starting of the feed
roller and/or rapid decreases in chipper rotor RPMs is
an indication that the feed speed is too high. Continued
operation under such conditions can result in plugging of
the discharge, belt damage, and inefficient operation.
Recommended Procedure:
Turn the flow control knob
fully clockwise to bring the feed roller to a stop. Turn the
flow control knob counter clockwise two full turns and
begin feeding material into the chipper. Adjust as needed.
4.6 CHIPPER FEED CONTROLLER
This machine is equipped with a Digital Display Controller
(DDC). The DDC monitors the chipper rotor RPM and
regulates the feed roller.
When chipper rotor RPM drops too low,
the feed roller
is stopped automatically to allow the chipper rotor to
process material.
When the chipper rotor returns to chipping RPM,
the
feed roller will automatically reengage.
Try Again Feature:
If the feed roller becomes obstructed,
the controller will reverse the feed roller momentarily to
clear the obstruction. The controller will then engage the
feed roller and feed the material again.
This cycle may continue for 10 cycles before staying in
the reverse position. Remove or reposition the material
manually and activate the forward position.
Remember to sharpen blades when necessary so
material will feed smoothly.
The rotor sensor and safety bar sensors must be set
to the correct clearance or the chipper will not operate.
Set the clearance to 1/32" (the width of a credit card).
The sensor will flash with every rotation of the chipper
rotor when the clearance is set correctly.
NOTE
4.7 USING THE DIGITAL DISPLAY
CONTROLLER
The feed roller FORWARD and REVERSE functions are
controlled by the controller. In addition to the feed roller
control functions, the controller also provides service
reminders, onboard diagnostics, operating instructions,
troubleshooting help and language selection.
4.7.1 MAIN MENU
After turning the key to the ON position, the ECHO Bear
Cat logo will be displayed followed by the screen shown
in Figure 4.1.
The model number of the chipper is displayed in the upper
right hand corner. The model number shown should match
the model of the chipper. If it does not, contact ECHO
Bear Cat Service at 1-866-625-4520 for help.
A scannable QR code is located in the lower left corner. It
will lead you to the ECHO Bear Cat website where owner’s
and parts manuals can be viewed and downloaded.
Battery Voltage is displayed in the upper left hand corner.
4.4 SLOWING AND STOPPING THE
CHIPPER ROTOR AND ENGINE
NEVER disengage the belt as part of the stopping or
shut down process. The belt should remain engaged
during the entire shutdown process.
Leaving the belt engaged is a vital part of proper
shutdown and ensures the rotor stops spinning in
conjunction with the engine shutting off.
TO PROPERLY SLOW DOWN AND STOP
THE ROTOR AND ENGINE
1. With the belt still engaged, slowly move the throttle to
the SLOW position with the belt still engaged.
2. Allow the engine to run at slow idle for 30-60 seconds.
3. Stop the engine by moving the throttle to the STOP
position or turning off the ignition switch.
4. Allow rotor to come to a complete stop.
5.
Once the engine is off and the rotor has completely
stopped, the belt can be disengaged by moving the
belt engagement handle back to the START position.
The rotor will continue to turn for some time after the
engine has been shut off. Make sure rotor has stopped
completely before inspecting or servicing machine.
NOTE