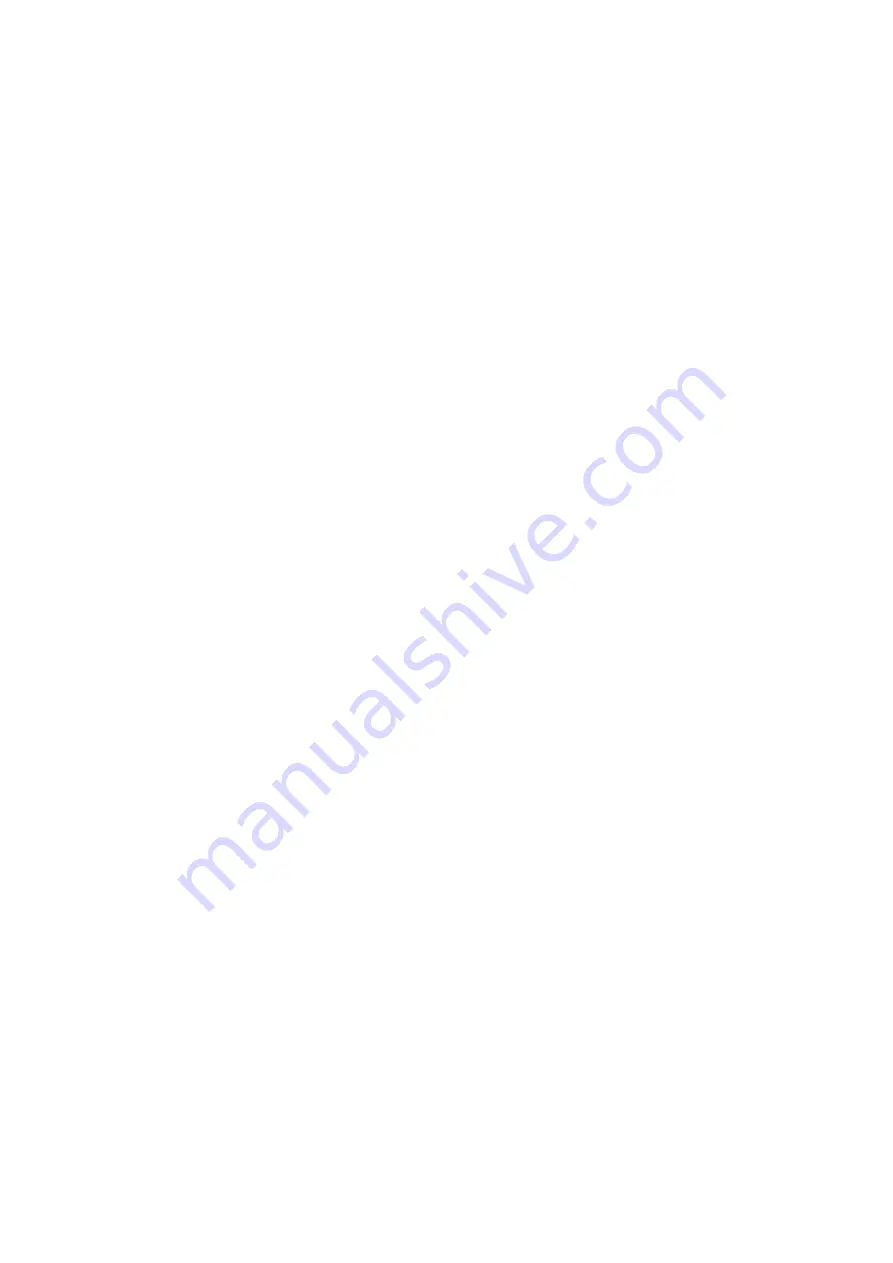
9
5.7 ADJUSTMENT
Note:
Final adjustment is carried out
after
the valve is
mounted on the pump and installed.
1.
To avoid overpressuring pump and system always
start on minimum setting i.e. Screw Out
2.
For increased bypass pressure, rotate Adjusting
Screw in clockwise direction ( i.e. screw in ).
DO
NOT
exceed pump or system design pressure.
2.
For decreased bypass pressure, rotate Adjusting
Screw anti-clockwise (i.e. screw out).
3.
Lock Adjusting Screw Lock Nut against BPV Cap
immediately after any adjustment is made.
4.
After Adjustment is completed, fit Adjusting Screw
Cap and Gasket.
Note:
Bypass valves characteristically exhibit three
distinct differential pressures during their operation:
a) The set or 'cracking' pressure which occurs
when product initially begins to be bypassed
against the preset spring load.
b) Maximum differential pressure, which occurs
when the flow of the bypassed product passes
through the bypass valve.
c) Full flow differential pressure which occurs
when all the product being pumped passes
through the Bypass Valve.
Note:
It is important to ensure the above characteristics
are understood fully in order to correctly apply and adjust
the Bypass Valve in a given system.
SECTION 6 - TROUBLE SHOOTING
6.1
PUMP FAILS TO PRIME OR DELIVER LIQUID
1 No liquid in supply tank.
2 Incorrect direction of rotation.
3 Speed
too
low:
a) If motor driven, check speed, line voltage and
phases.
b) If engine driven, check governor setting and
engine speed.
4 System discharge head too high - check system
head, friction losses and bypass valve setting.
5 Excessive inlet restrictions - check NPSH available
(inadequately sized inlet piping may cause high
friction losses, vapour pressure of liquid may be too
high). Check with vacuum or compound gauge.
6 Air leaks and/or air pockets in inlet line - check inlet
piping.
7 Bypass valve open due to obstruction under seat of
valve or setting too low.
8 Inlet filter/strainer blocked or leaking air.
9 Pump cannot clear vapour due to excessive
discharge pressure e.g. static head.
6.2
LOW OUTPUT
1 Discharge head too high.
2 Entrained air or gases in liquid pumped.
3 Strainer offering excess resistance to flow.
4 Inlet and/or discharge pipes of insufficient diameter,
causing excessive friction loss.
5 Bypass valve pressure setting too low - Increase
pressure by screwing in adjusting screw. DO NOT
exceed pump or system design pressure, or overload
motor etc.
6 Insufficient NPSH available.
7 Excess axial clearance setting of rotor to cover.
8 Excess clearances in pump due to wear.
6.3
EXCESSIVE POWER CONSUMPTION
1 Differential pressure higher than rating.
2 Liquid properties not as specified - check viscosity.
3 Rotating parts bind - check for proper clearances or
foreign matter in pump.
4 Bearings worn - inspect and replace as required.
5 Obstructions in pipe lines, clogged strainers, partially
open valves.
6 Pump speed too high.
7 Voltage too low.
6.4
PUMP IS NOISY
1 Cavitation is taking place - increase NPSH by:
a) Removing inlet line restrictions created by:
(i)
Inadequate
pipe
sizes / excessive line
lengths.
(ii) Incorrect selection of valves, fittings etc.
(iii) Strainer not permitting free flow of liquid to
pump.
b) Increasing static head in supply vessel.
c)
Reduce
product
viscosity.
2 Rotating parts bind - check for proper clearances.
3 Pump and driver misaligned - check coupling and
realign as required.
Summary of Contents for MD Series
Page 12: ...12 NOTES...