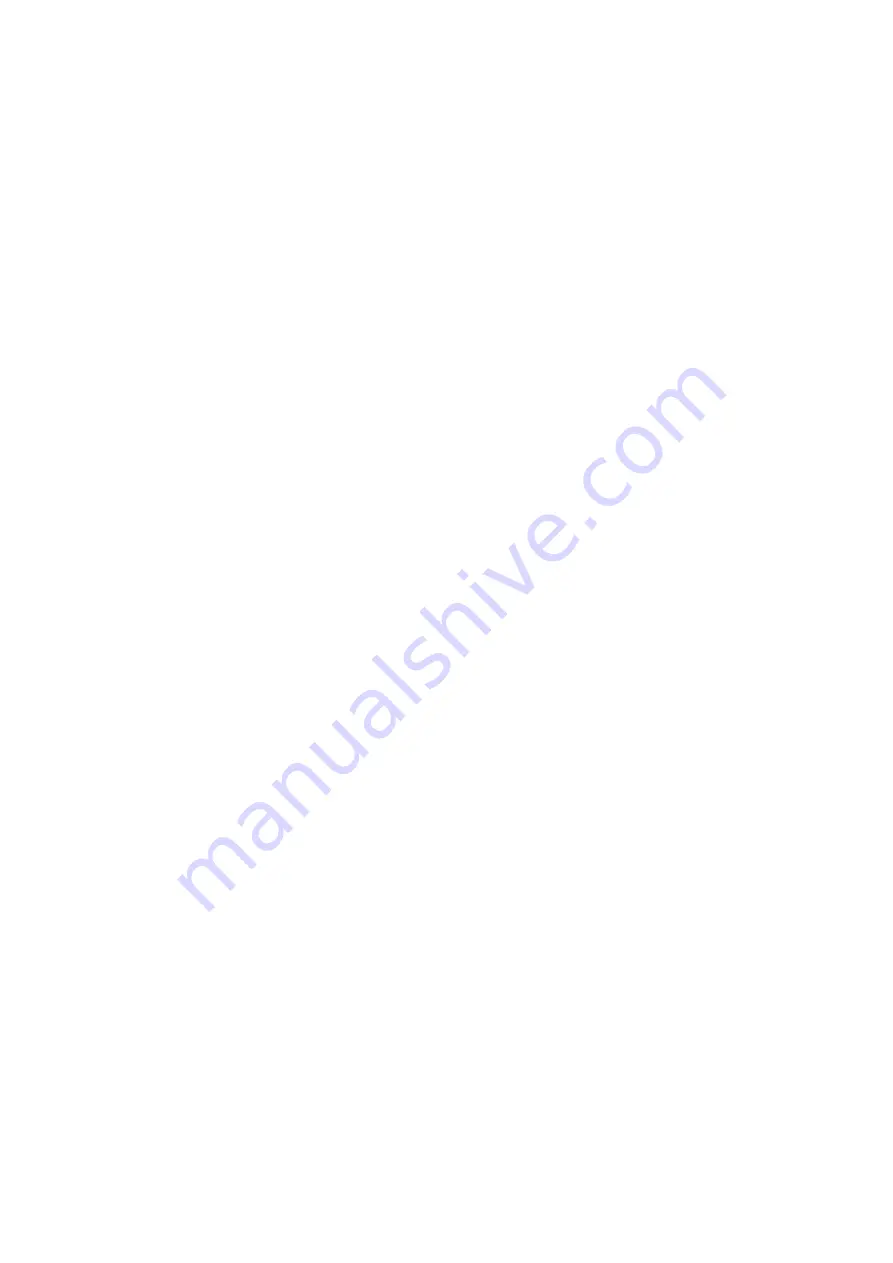
3.4
LUBRICATION
Lubrication of the Inner Rotor bearing and Bracket
Bearing (both are sleeve bearings) is dependent on the
pumpages' lubricating qualities/material selection of the
bearing.
The Ball Bearing is lubricated at the time of assembly
with a high quality lithium base grease. Replacement of
this grease is normally only necessary when major
maintenance is carried out.
3.5 STARTUP CHECKLIST
•
Lubricate as required.
•
Alignment of couplings.
•
Direction of rotation.
•
Freedom of rotation of shaft.
•
Inlet and discharge valves open
•
Product available for pumping
•
Special precautions as required
Note:
Do not start pump against closed discharge valve
or with inlet (suction) valve throttled. Ensure bypass
valve (if fitted) is operational and set to the correct
pressure.
Note: Do not exceed system or pump design
pressure as equipment failure could result. Do not
run pump dry. Failure to remove air/vapour could
prevent pump from priming and result in pump
damage.
3.6
OPERATIONAL CHECKS
Inspect pump frequently during the first few hours of
operation for such conditions as excessive heating of
bearings or stuffing box, vibration, unusual noises etc.
3.7
BYPASS VALVE
To protect the pump from overpressure due to
inadvertent shutting of discharge system, EBSRAY can
supply integral or inline Bypass Valves which are capable
of circulating the entire pump output. The integral type
Bypass Valve is mounted on the pump Cover and
bypasses pumpage from the pressure side to the inlet
side of the pump.
The inline type Bypass Valve is installed in the pump
discharge line and normally returns to the inlet side of the
pump or back to tank. Fluid temperature will rise if
differential pressure is high and recirculating bypass
conditions are maintained for extended periods
(particularly with integral Bypass Valve). The Bypass
Valve should be set on site, in accordance with the
predetermined pump and/or system differential pressure
required. Refer separate instructions.
SECTION 4 - MAINTENANCE
CAUTION
PRIOR TO ANY DISASSEMBLY OR SERVICE,
VERIFY THAT ALL REQUIREMENTS OF STATUTORY
REGULATIONS OR CODES ARE MET AND THAT
SPECIFIC SITE REQUIREMENTS ETC ARE
SATISFIED.
Some minor maintenance tasks and inspections can be
performed with the pump 'in line' so long as complete
isolation, depressurising and purging procedures have
been completed. However for major maintenance it is
recommended that the pump be removed from the
installation.
4.1
SPARE PARTS
1.
When ordering spare parts, to ensure a minimum
of delay and correct replacement to original
specification ALWAYS quote the pump Serial
Number which is located on the nameplate of the
pump.
2.
Advise the Cat #, Description and quantity
required. (Refer to Section 7 – Parts Designation)
3.
Advise complete delivery instructions.
4.2
PREPARATION FOR DISASSEMBLY
1.
Obtain the appropriate Work Permit if required.
2.
Isolate pump from liquids in inlet and discharge
lines, depressurise and purge out any toxic,
flammable, corrosive or air hardening liquids.
3.
Isolate power supply to motor.
4. Disconnect
porting
connections.
5.
Remove pump from installation.
6.
Mark relevant mating components for correct
reassembly orientation.
4.3
DISASSEMBLY
Note:
Before proceeding, make sure Bracket is firmly
attached to baseplate or bench etc. to avoid
overbalancing when rotor is withdrawn. Mark relevant
mating components to ensure correct replacement.
1.
Remove pump coupling half, key and Spacer.
2.
Release Grubscrew on Outer Lockring and
Grubscrew locking Race Carrier to Bracket
3.
If fitted, remove Bypass Valve assembly from
Cover – Refer Section 5.
4.
Remove suction/pressure circulation harness
assemblies if fitted.
5.
Remove Cover assembly complete with Inner
Rotor. Care should be taken to prevent Inner
Rotor sliding off Inner Rotor Pin. To facilitate
removal of Cover, tapped extraction holes are
fitted
6.
Disassemble Cover assembly if required.
.
4
Summary of Contents for MD Series
Page 12: ...12 NOTES...