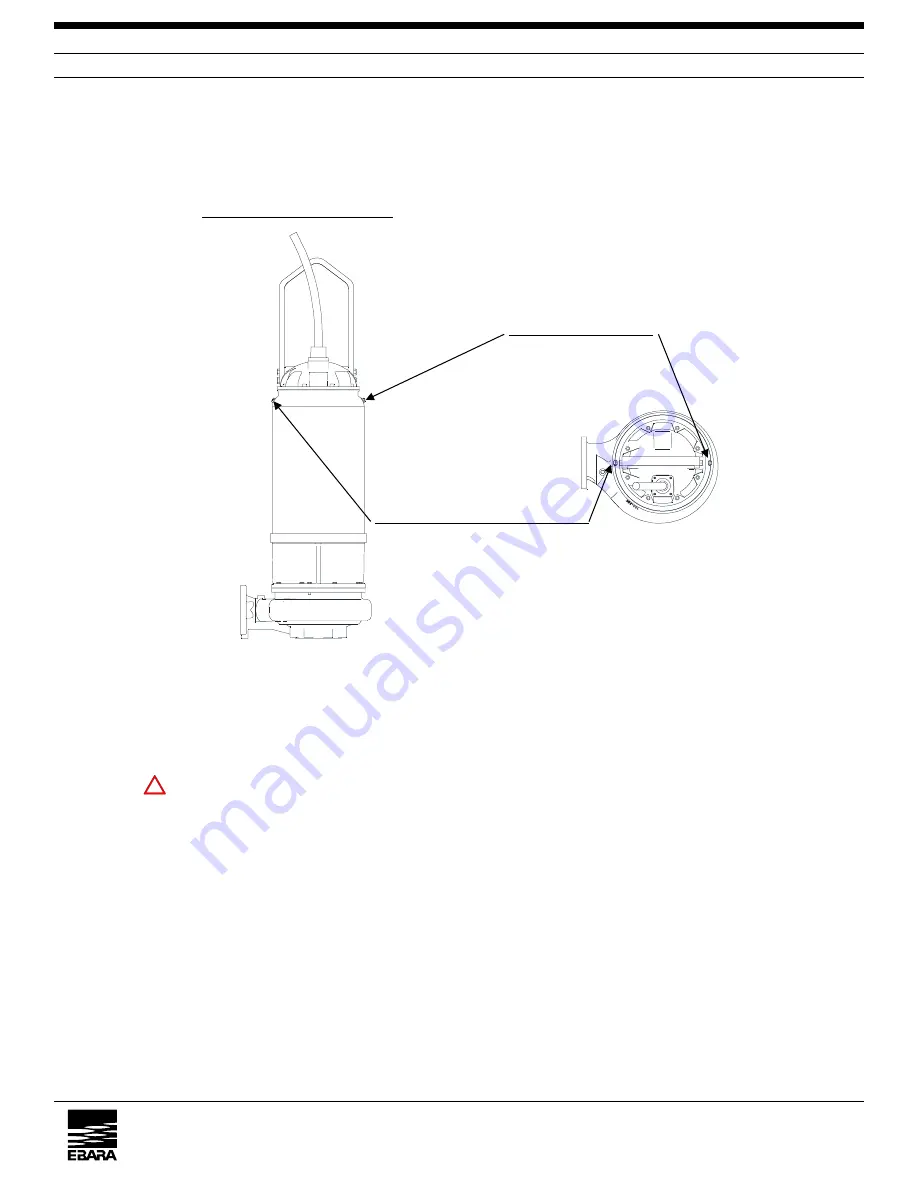
5
EBARA
PUMPS AMERICAS CORPORATION
www.pumpsebara.com
(t) 803.327.5005 (f) 803.327.5097
rev. 01/21
EBARA Submersible Sewage Pumps
Operating, Installation, and Maintenance
DL3FU / DL3MFU / DL3KFU / DL3KMFU / DDL3FU / DV3FU/ DML3FU
INSTRUCTION MANUAL
P.4
PM32U
3.1.1 Internal Liquid Supply (Figs. 1, 2 and 3)
2~5HP(1.5-3.7kW) models come standard without internal cooling system and are shipped with proper
oil capacity per Table 2. 7.5~60HP(5.5~45kW) are standard with internally cooled system (no oil fill
required) and are shipped with proper coolant capacity per Table 1.
Fig. 1 Fig. 2
The motor shaft is sealed with a mechanical seal. The coolant chamber provided between the
two sealing stages can be filled with coolant by standing the pump vertical
on a level surface
and remove plugs
“
Coolant supply hole
”
and
“
Air vent & full level check hole
”
.
CAUTION:
THE SEAL CHAMBER MAY BE UNDER PRESSURE. HOLD A RAG OVER
THE PLUG TO PREVENT SPLATTER.
Pour the specified coolant into the coolant chamber through
“
Coolant supply hole
”
until the
coolant flows out of
“
Air vent & full level check hole
”
. (See Table 1)
After the coolant chamber is filled to the specified level, plug the two holes.
!
Air vent & full level check hole
50%: Propylene Glycol
50%: Water
Coolant supply hole
COOLANT (Internal liquid)