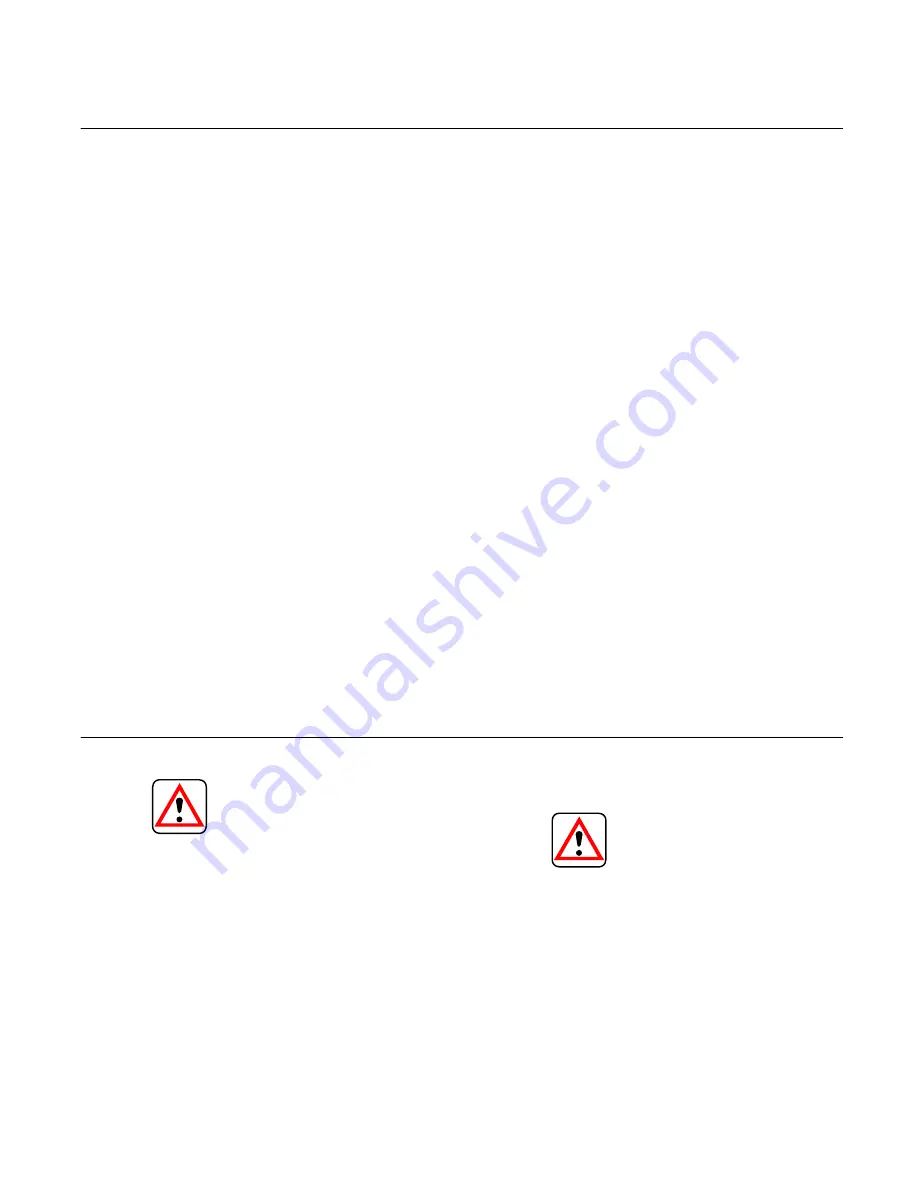
7
E. Start-Up
After electrical connection is made, the hydraulic system can
be started (with feedback devices disconnected). With
balanced current in the coils, the actuator controlled by the
servo valve should not move. If movement of the actuator in
either direction is excessive at this stage, and the current to
the torque motor coils is still balanced, the spool of the servo
valve is probably not centered.
F. Null Adjustment
Null is accomplished by loosening set screw (32) then
turning adjusting screw (33) clockwise to increase the flow
out of Port A and counterclockwise to increase the flow out of
Port B.
When sufficient adjustment cannot be made to properly
center the valve, remove the torque motor cover and adjust
the pilot spool with a 3/64 Allen wrench. In doing this, it
should be remembered the torque motor is immersed in oil
which will be released when the cover is loosened.
If the actuator (i.e., motor or cylinder) continues to move after
the spool is properly centered, check the electrical signal
shown in the milliammeters. If the current to the servo valve
also varies or is unbalanced, the difficulty is probably in the
electrical programming circuit. But if the milliammeters are
showing a constant current without feedback connection and
the actuator is still fluctuating erratically, the trouble is
probably in the servo valve or elsewhere in the hydraulic
system. If difficulty still exists after preliminary checking, the
troubleshooting table on page 9 should help locate it.
G. Linkage Ratio
Linkage ratio is the relationship of pilot spool movement to
main spool movement of the valve. This ratio is stamped into
the nameplate of each unit. Linkage ratio is set at the factory
based on information furnished with customers orders.
Required flow, load pressure, available supply and control
pressure should be specified. If this information is not
furnished with the order, valves will be shipped with a 3.5 to 1
ratio. Adjustment, if necessary, must then be made in the
field.
To adjust linkage ratio, (1) remove cover and torque motor,
(2) loosen fulcrum screw with a 5/32 Allen wrench, (3) slide
the fulcrum screw up or down in its slot. Ratio figures are
stamped in the adaptor plate for reference in screw
movement. If ratio is readjusted, have nameplate restamped.
H. Dither
The purpose of dither is to eliminate stiction and to increase
the dirt tolerance within the valve. To accomplish this, it is
necessary to keep the pilot spool moving within the
deadband of the valve.
In every application, dither of 60-400 cycles must be applied
to the pilot stage of the servo valve. Readily available
60-cycle current usually answers the dither requirement in
the easiest and least expensive way.
Dither should be established as follows: Increase the
amplitude of the dither until it can be felt at the output of the
actuator. Then, slowly back down on the adjustment until no
vibration can be felt on the actuator output.
Section VI – Overhaul
A. Disassembly
CAUTION
Before removing a unit or a part of a unit from a
hydraulic circuit, be certain the unit concerned is not
subject to hydraulic pressure or to an electrical
power source.
Complete disassembly of the servo valve should be under-
taken only at periodic intervals as recommended by the
manufacturer or as determined by the application and
operating conditions. Otherwise, a servo valve should not be
disassembled further than necessary to correct a malfunc-
tion. Follow the sequence of index numbers shown in Figure
6 for disassembly.
When disassembling a servo valve, special attention should
be given to identification of parts for proper reassembly. This
is especially important for returning the valve spools, sleeves
and other related parts in correct relationship to each other
and to the block. The torque motor is a wet type so that
removal of the cover results in the release of hydraulic fluid.
Slightly oversize holes in the torque motor base permit
proper readjustment of the torque motor as it is secured to
the servo body. Attention also must be given to mating port
holes mountings and gaskets on the bottom face of the valve
block.
CAUTION
Never use an air hose on or near a hydraulic device
because of water and dirt in the air stream.
Check the valve spools and block bores for roughness or
scratches. Slight scratches and abrasions can be removed
with crocus cloth or light lapping. Do not round off sharp
edges of valve spool lands. Coat the spools with hydraulic
fluid and test in the block bore for freedom of movement.
A malfunction of the torque motor can be checked by
energizing with proper current and measuring armature
deflection. Maximum current should give .020 movement of
the armature in each direction. If this deflection does not
occur, a continuity check of the coils should be made with a
volt-ohmmeter. If the torque motor or any parts on the pilot
spool linkage appear to be damaged, they can be replaced
with new parts.