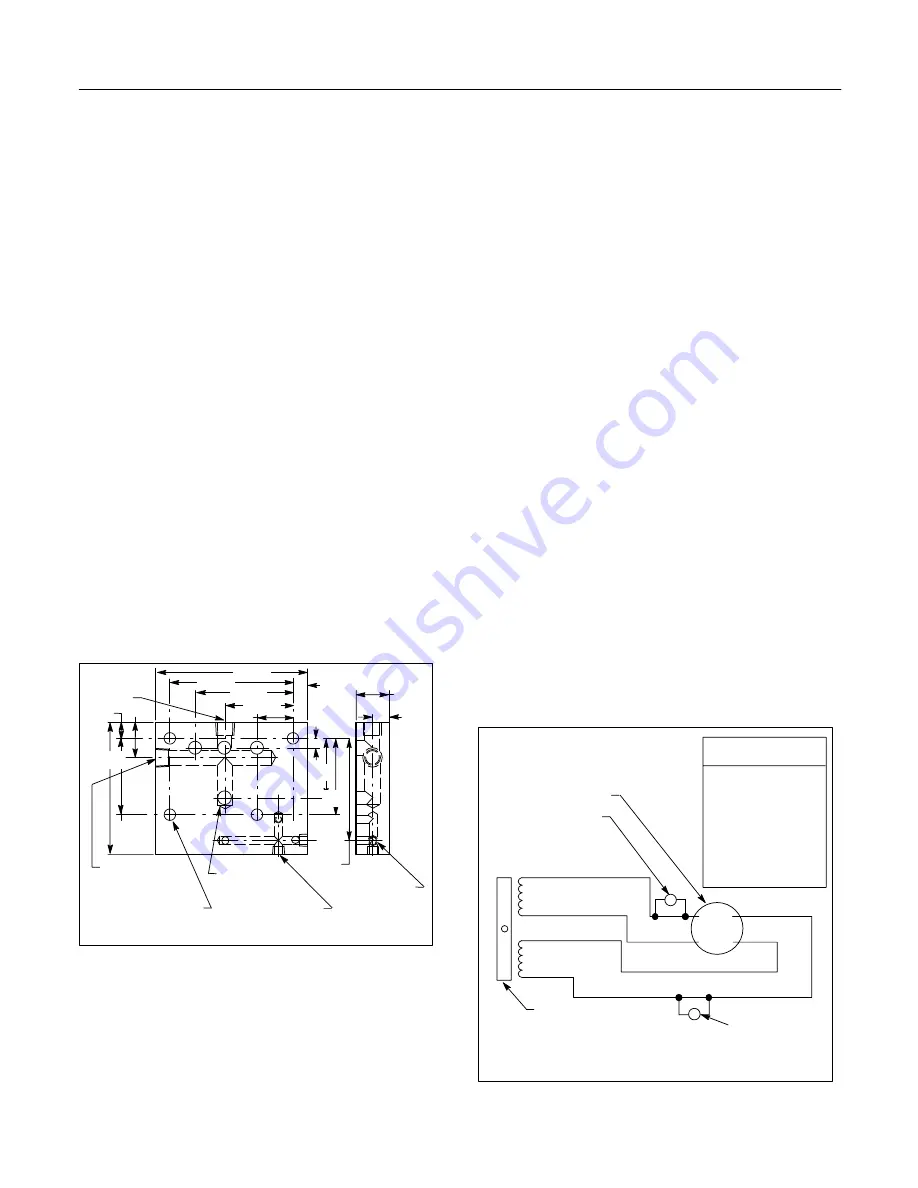
6
Section V – Installation
Installation drawing 501500 shows correct valve dimensions,
port location, sub-plate mountings and other data. Vickers
engineering personnel should be consulted to determine
correct valve use and other assistance. Because of the
extreme precision required of servo valve operation, extra
precautions must be taken with the application of the valve to
the circuit.
All piping should be thoroughly cleaned and pickled.
Reservoirs should be carefully cleaned and flushed prior to
addition of hydraulic fluid.
Full flow filters (10 micron) should be installed in both supply
lines and control pressure lines. If desired, parallel filters can
be installed with shut-off valves arranged so filters can be
changed without interrupting system operation.
NOTE
Hydraulic fluid should be filtered to 10 microns while
filling reservoir.
A. Flushing
Complete flushing of the hydraulic system will save
considerable time in start-up and downtime of the servo
system.
Before installing servo valve, flush the hydraulic system with
clean fluid. A flushing plate (see Figure 3) can be purchased
from any Vickers branch. It should be installed on the work
face or mounted by means of a sub-plate to permit free
return of hydraulic fluid from pressure to tank. Flush the
system from one to two hours, then, replace the full flow filter
cartridges and continue to flush. This procedure should be
continued until filter elements and the bottom of the filter
housing are free from contamination. After the system is
clean, install the servo valve.
1.81
Figure 1. Schematic Sketch of Servo Valve
Figure 3. Flushing Plate (938714)
4.62
3.75
2.06
3.00
1.13
.437
.43
1.03
2.312
4.00
.4218 Drill
2.50 deep
1/4 NPT
.4218 Drill
3.50 deep
1/4 NPT
.3750 Drill
thru 4 holes
.4218 Drill
.500 deep
4 holes
1.000
Stock
.500
.312
2.5
3.125
.234 Drill
2.625 deep
1/16 NPT
.234 Drill
1.250 deep
1/16 NPT
B. Mounting
Hydraulic connections between a servo valve and the
actuator it controls can be made by a sub-plate or manifold,
or the servo may be attached directly to a prepared, flat,
ported face of the work unit. The sub-plate (SVGM2-03-10 or
SVGM2-06-10) permits pipe connections with the work unit.
Manifolds (SVGM1-*-03-10, SVGM5-*-06-11 and
SVGM6-*-06-10) allow direct manifolding of the SA4 series
valves to any MF-2003-A thru MF-2020-A size hydraulic
motor.
Manifolds may be obtained with three variations: (1) with
cross line relief valves and variable orifice, (2) with cross line
relief valves only and (3) with variable orifice only. In all
applications the servo valve is attached by four mounting
screws which should be tightened to the torque values
specified in Table 1 in Section VI – Overhaul on page 7.
The mounting face of the servo valve has ten ports, each
containing an O-ring. When the servo valve is mounted, the
O-rings are compressed providing a leakproof installation.
C. Hydraulic Fluid Recommendations
Hydraulic fluids are required to perform the dual functions of
lubrication and transmission of power. Thus, oil should be
selected with care with the assistance of a reputable oil
supplier. If fire resistant fluid is required, Vickers application
engineering personnel must be consulted.
D. Electrical Connection
It is desirable to install milliammeters in series with the torque
motor connections as shown in Figure 4. This will prove
valuable for isolating electrical and hydraulic problems
occurring during system trim and in troubleshooting electrical
problems.
Electrical connections between the system and the torque
motor should be checked to insure that they are in
accordance with Figure 4.
When current through terminals “A” and “B” (Figure 4) is
greater than current through terminals “C” and “D”, flow from
Port “B” (FIgure 1) to the fluid motor or cylinder increases.
When the electrical system is turned on, current to the two
coils should be balanced (1/2 input differential in each coil).
Figure 4. Wiring Diagram – Schematic View
Coil “B” is located on end of torque motor which
has arrow and pilot valve connection nut.
Coil
Color
Resist.
20
Brown
25
Gray
40
Yellow
100
Orange
280
White
2200
Blue
5300
Black
Milliammeters
Receptacle
Torque Motor
Coil “B”
Torque Motor
Coil “A”
Torque Motor
Armature
Color
Red
Color
Red
Milliammeters
D A
B
C