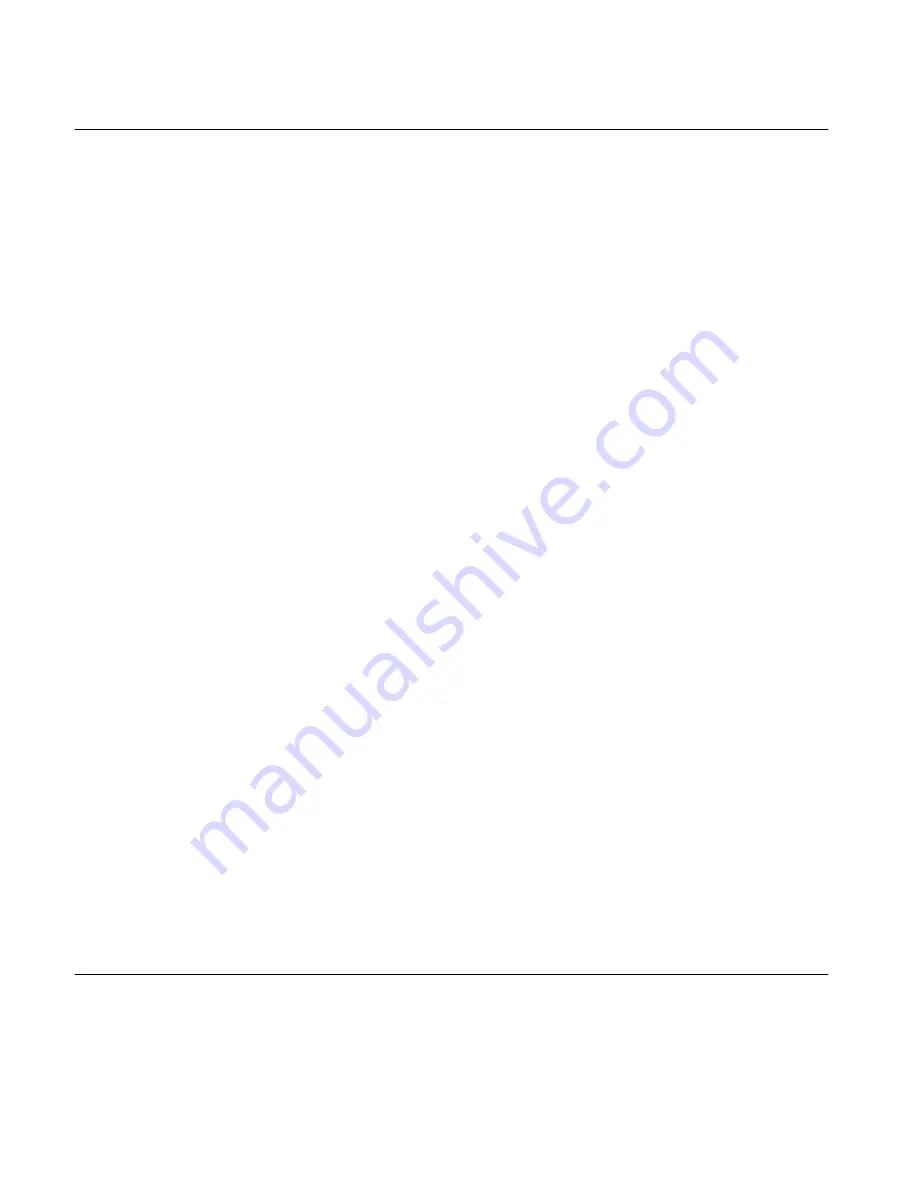
10
2.
Shaft End.
Remove the shaft key and foot mounting
(if used). Remove the snap ring from the body and tap the
cover end of the shaft to force out the shaft and front bearing.
If it is necessary to remove the bearing from the shaft,
support the inner race in an arbor press while pressing the
shaft out.
Remove the oil seal and tap out the inner bearing by
inserting a punch in the cover end of the body.
C. Inspection and Repair
1. Discard the used oil seal and o-rings. Clean all parts
in mineral oil solvent and place them on a clean surface for
inspection.
2. Check for wearing surfaces of the body, pressure
plate, ring and rotor for scoring and excessive wear. Remove
light scoring by lapping. Replace any scored or worn parts.
3. Inspect the vanes for burrs, wear and excessive play
in the rotor slots. Check that vanes do not stick in the rotor
slots. They should move from their own weight when both
rotor and vanes are dry. Replace any defective vanes.
4. Rotate the bearing on the shaft while applying pres-
sure to check for wear, looseness, roughness and pitted or
cracked races.
5. Inspect the oil seal journal on the shaft for scoring or
wear. Replace the shaft if marks cannot be removed by light
lapping.
6. Inspect vane rocker arms for wear and loss of ten-
sion. Replace the rotor sub-assembly if rocker arms are
defective.
D. Reassembly
Coat all parts with clean hydraulic oil to facilitate reassembly
and provide initial lubrication.
1.
Shaft End.
Place the body on a block, shaft end up.
With a driver which contacts the outer race only, seat the
inner bearing in the body.
Press the shaft seal into the body with the sealing lip facing
the cover end. Use a driver which will apply force only near
the seal periphery. Be certain the seal is firmly in place and is
not cocked.
Press the outer bearing onto the shaft while supporting the
inner race. Cover the shaft splines with tape or a bullet and
install the shaft. The outer bearing must seal firmly in the
body. Install the snap ring which retains the shaft and
bearing. If a mounting bracket is used, it can be installed
now. Tighten the screws evenly to prevent cocking. Install
the shaft key.
3.
Cover End.
Place the unit on blocks, shaft end
down. Install the o-ring in the groove in the body. Insert both
locating pins in the body face. Place the ring on a clean
smooth surface and insert the rotor inside the ring. Insert the
vanes into the rotor slots, being sure the rocker arm is
properly located behind each individual vane on both sides
of the rotor. The ring, rotor and vanes are now installed on
the locating pins.
NOTE
On -13 design models, pin location makes it
impossible to assemble the ring incorrectly.
When installing the vanes, be certain they rest squarely in
the slots and not on the rocker arms. Check this by turning
the shaft by hand and noting whether any vane extends
beyond the side of the rotor.
Position the pressure plate on the locating pins and install
the pressure plate o-ring and the wave washer. Install the
o-ring in the cover and carefully place the cover over the
plate and wave washer against the ring. Be sure the washer
and o-ring are not dislocated. slowly rotate the cover to its
correct position with relation to the body (see Figure 6).
Install the cover screws and washers and tighten them to the
torque shown in Figure 7. Turn the shaft by hand to be
certain there is no binding.
Section VII
–
Testing
Vickers Mobile application engineering personnel should be
consulted for test stand circuit requirements and construc-
tion. If test equipment is available, the motor should be
tested at recommended speeds and pressures shown on
installation drawings (see Table 1).