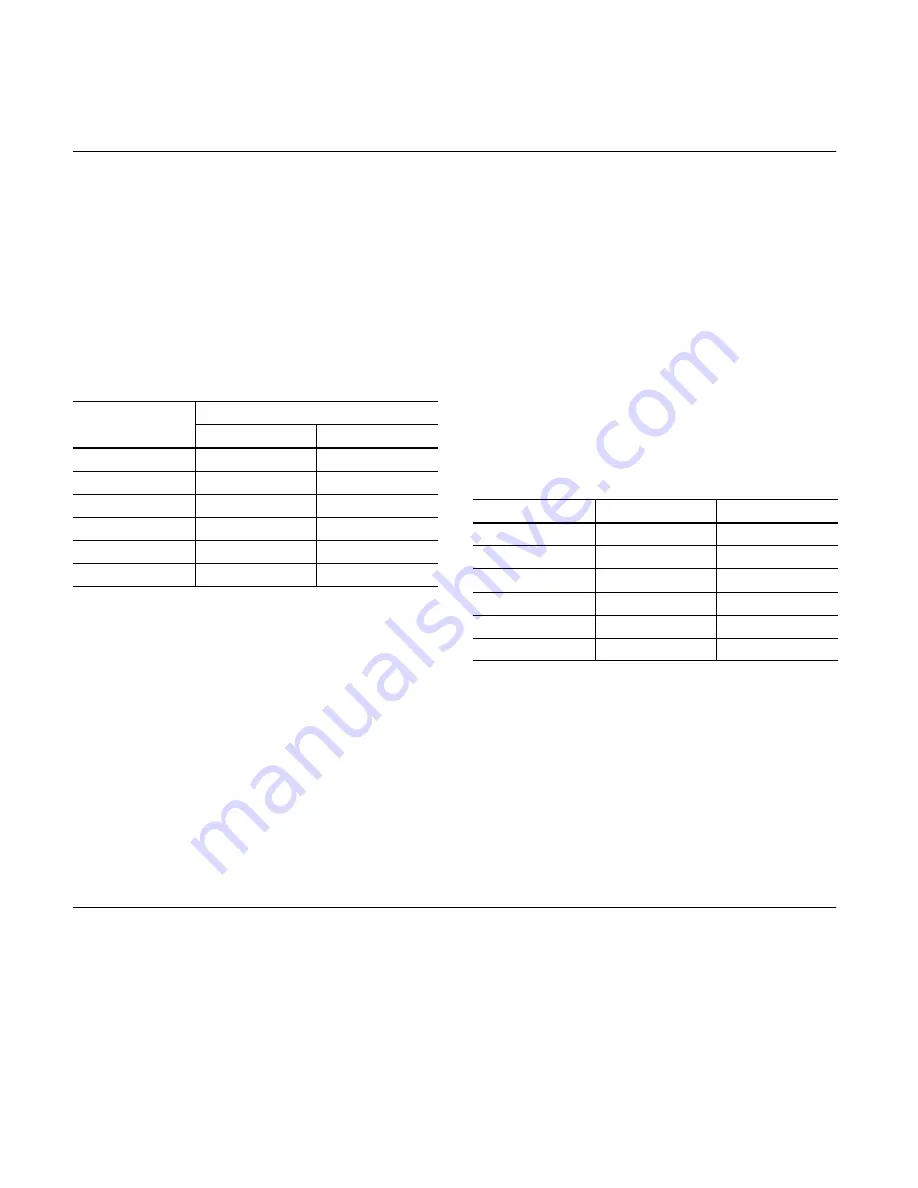
10
c. Make sure “O” ring (22) and back-up ring (21) are
assembled correctly. Position as shown in Figure 8. Apply a
small amount of system fluid to screws (24) and thread
screws into cartridge kit. Install cartridge kit 920) into body
(38).
7. Install “O” ring (36) over cartridge kit (20) and into
“O” ring groove of body (38).
8. Line up the two cartridge kit pins (26) with the holes in
housing (19) and then install the housing. Position the
housing according to punch marks made during step C.2 of
Disassembly procedure. Attach housing to the body with four
screws (18). Torque the screws to specifications noted in
Table 4.
Torque Specification
Model
N.m
lb.ft.
2520V
48–55
65–75
3520V
102–118
140–160
3525V
102–118
140–160
4520V
188–203
255–275
4525V
188–203
255–275
4535V
–
–
Table 4. Torque specifications for screw (18)
9. If cartridge kit (6) is replaced with a new kit, line up
pins (13) with holes in housing (19) and install kit into
housing. If cartridge kit requires assembly, assemble in
reverse order of disassembly. During assembly, note the
following precautions.
a. Make sure the rotation arrows on the rotor (15)
and ring (14) are in direction of pump rotation.
b. Be certain the sharp edges of vanes (16) lead in
direction of pump rotation.
c. Make sure “O” ring (9) and back-up ring (8) are
assembled in the correct position (Figure 8).
NOTE
Cartridge kit (6) is assembled into housing (19) in
the reverse manner of cartridge kit (20). Make sure
the rotation arrow of the ring points in direction of
rotation.
d. Apply a small amount of hydraulic fluid to screws
(11) and thread screws into cartridge kit.
10. Install sealing ring (10) into cover (5).
11. Install “O” ring (7) over cartridge kit (6) against the
housing face.
12. Position cover (5) over cartridge kit (6) according to
the prick marks made during step C.2 of disassembly
procedures. Install cover (5) and secure with screws (4).
Torque screws (4) to specifications noted in Table 5.
Model
N.m
lb.ft.
2520V
54–68
40–50
3520V
54–68
40–50
3525V
88–102
65–75
4520V
54–68
40–50
4525V
88–102
65–75
4535V
188–203
255–275
Table 5. Torque specifications for screw (4)
13. Install key (3) into groove on shaft (34).
14. Place pump into mounting bracket (2) and secure
with two screws (1).
Section VII – Start-Up and Test
A. Start-Up
Install the unit into the system. Make sure that the drive shaft
is aligned properly, all connections are tight and the hydraulic
oil source is open to pump inlet. If an overhead reservoir is
used, purge air from inlet line.
The pump should prime almost immediately with a minimum
drive speed of 600 RPM. Intermittently operate (jog) the
pump until it primes. It may be necessary to loosen the outlet
fitting temporarily to purge trapped air. Failure of the pump to
prime in a short period of time indicates incorrect assembly
or restricted flow from the reservoir.
B. Test
Use your hydraulic system to test the unit. Refer to the
installation drawings listed in Table 1 for recommended
speeds and pressures. If more precise testing is desired,
consult your Vickers sales engineering office.