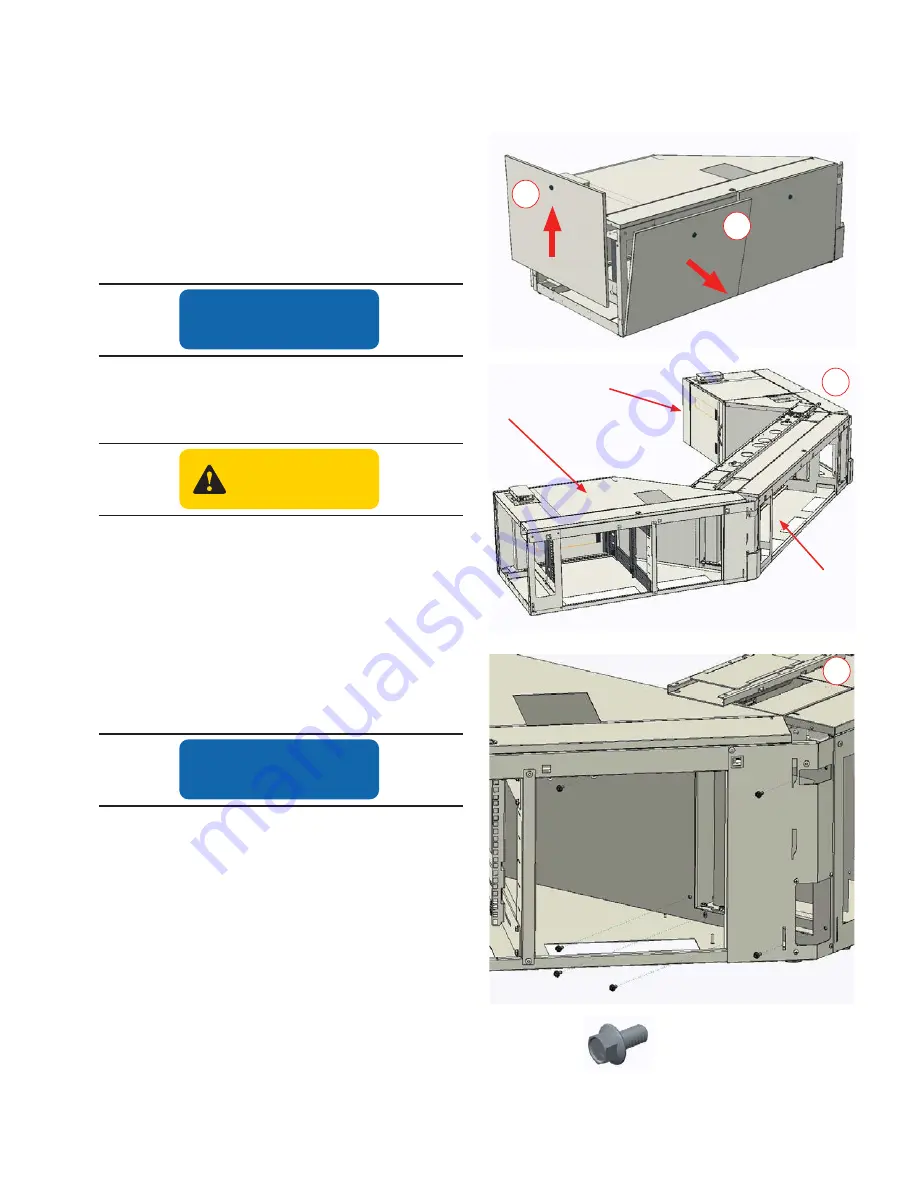
ONGUARD COMMAND CONSOLE INSTALLATION MANUAL
www.eaton.com/onguard
7
OnGuard Command Console
Installation Manual
A. Assemble the Base Cabinets
1� Unlock and remove rear panels from each of the base
cabinets� To remove a panel, open rear cable channel
cover, and pull panel off from top edge�
2� Unlock and remove the end panels from the left and right
base cabinets by lifting up on the panels�
3� Position the three base cabinets as close to their final
positions as possible
NOTICE
ONCE COMPLETELY ASSEMBLED, THE CONSOLE WILL
BE HEAVY AND DIFFICULT TO MOVE, PARTICULARLY ON
CARPETING.
CAUTION
TO ENSURE ADEQUATE COOLING OF STORED ELECTRONIC
COMPONENTS, DO NOT PLACE THE REAR OF THE BASE
CABINETS CLOSER THAN 3" TO A WALL.
4� Assemble the left and right base cabinets to center base
cabinet with (12)
1
⁄
4
" x ½" self-threading hex head screws
(6 screws for each flank base cabinet)�
5� Adjust leveling feet to ensure top of base structure is
level and aligned�
NOTICE
DO NOT OMIT ANY SCREWS. ALL SCREWS ARE REQUIRED
TO ENSURE THAT CONSOLE REMAINS STABLE WHEN WORK
SURFACE IS ELEVATED TO HIGHEST POSITION.
ALL LEVELING FEET OF BASE STRUCTURE MUST BE IN
DIRECT CONTACT WITH THE FLOOR TO ENSURE CONSOLE
REMAINS STABLE WHEN WORK SURFACE IS ELEVATED TO ITS
HIGHEST POSITION.
IMPROPER ADJUSTMENT OF THE LEVELERS MAY CAUSE THE
BASE CABINETS TO TWIST, RESULTING IN MIS-ALIGNMENT OF
FRONT DOORS AND DRAWERS. ENSURE THAT LEVELERS ARE
ADJUSTED IN SUCH A WAY AS TO ENSURE PROPER DOOR
AND DRAWER ALIGNMENT.
A x 12
Right Base
Cabinet
Center Base
Cabinet
Left Base
Cabinet
Hardware
required
A�1
A�2
A�3
A�4
SECTION III - Assembling the Console