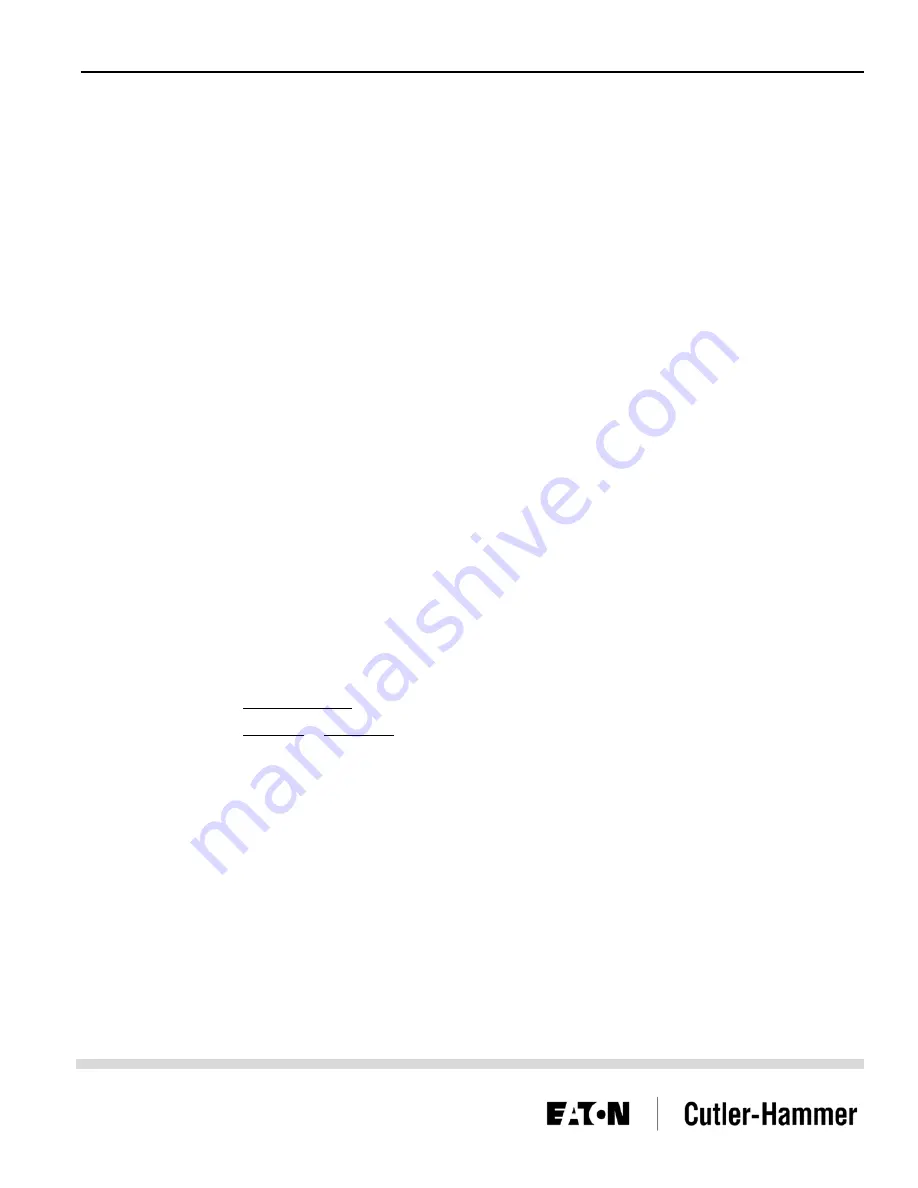
Chapter 4: Modicon P410 Servo Controller
45
Modicon 410 Word and Bit References
The following section describes the use of Modicon 410 word and bit references in your configuration.
The general word referencing method is:
[plcname,word#format]
The “plcname” is the name of the designated PLC as listed in the PLC Name and Port table. The
“word” is the reference number (address) of the word or register to be read or written. The “#format”
is a code that specifies the format of the data being read or written. The “plcname” and #format” are
optional.
The general bit referencing method is:
[plcname,bit]
The “plcname” is the designated PLC as listed in the PLC Name and Port table. The “bit” is the
reference number (address) of the bit, coil or input to be written or read.
See chapter 10 for a more detailed explanation of word and bit references, including format
descriptions.
This interface supports only reading and writing 32-bit signed user registers. Register addresses must
be in a decimal format, in the range of 0 to 99.
The default PanelMate unit read/write format is signed 32 (S32). Only 32-bit data types are allowed
(S32, U32, BCD6, BCD8, BIN6, BIN8).
The following is the format for a register reference:
[rr]
rr = PLC reference number of the register
(o – 99 decimal, leading zeros not required)
Examples
The following are examples of valid PLC references that may be assigned in the PanelMate expression
fields.
Word References:
Reference Description
[1]
Register
1
[36]
Register
36
[48]
Register
48
Note
The Modicon 410 will only perform single register reads and writes. Due to this fact, update
times will be affected by the number of registers being polled by the PanelMate unit. The
reason update times are slower is because a packet must be sent for each register that is read.
Maintenance Access
A Maintenance Template cannot be used to monitor Modicon 410 Servo Controller references.
Summary of Contents for Cutler-Hammer PanelMate Modicon
Page 3: ......