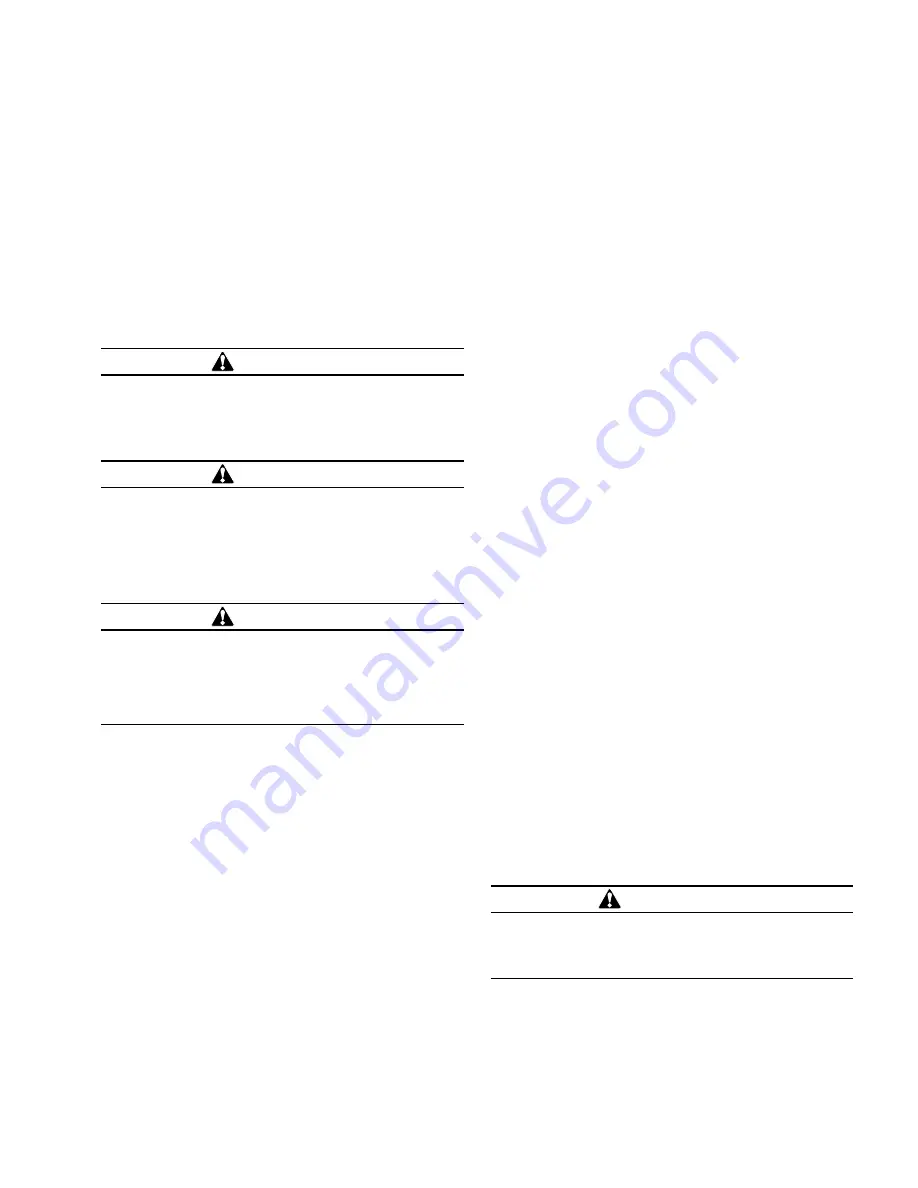
Cover removal
(For Envirotemp™ FR3™ fluid-filled units, see “Insulating
Liquid Maintenance” Section before continuing.)
Transformers that have been system connected should be
de-energized, grounded, and disconnected before being
opened for inspection.
Substation transformers may have either bolt-on or weld-
in-place main tank covers. Access to the interior of a trans-
former with a bolt-on main tank cover without handholes
requires removal of the entire cover. Access to the interior
of the welded-in-place main tank cover design is typically
through manhole or handholes.
WARNING
Before the tank cover, manhole cover or handhole cover
is removed, the transformer tank must be vented to zero
pressure by activating the pressure relief valve . Failure
to do so may result in severe personal injury, death or
property damage .
CAuTION
If the main tank cover, manhole cover, handhole cover
or access cover must be removed for internal inspection
or service of the transformer, precautions must be taken
to prevent dirt or moisture from entering the opened
unit . Contamination of the insulating fluid will prevent
the transformer from operating properly and may cause
serious damage to the transformer .
WARNING
Transformers must never be opened or serviced
while system is connected, ungrounded or energized .
Tampering with the covers or cover seals of a
transformer that has not been de-energized, grounded
and disconnected may result in severe personal injury,
death or property damage .
To remove a bolt-on main tank cover
1. Thoroughly clean the cover. Remove all dirt, grease and
moisture.
2. Relieve internal tank pressure by manually operating
the pressure relief valve.
3. Remove the hardware (3/8” inch nuts using a 9/16”
socket) which attaches the cover to the tank.
4. Gently pry the cover upward, making sure that the
cover gasket does not come in contact with the
transformer insulating liquid. Lift vertically to prevent
damage to cover, bolts, and tank gasket.
5. Remove the gasket sections from the tank flange,
noting the location and orientation (up/down) of each
piece.
To reinstall the bolt-on main tank cover
1. Return the gasket sections to their original positions
and orientation.
2. Reinstall the cover, using 25 ft-lbs. torque to tighten the
cover hardware. After installing all the nuts, re-torque
each nut to insure the proper torque is achieved.
3. Remove the pressure relief valve and pressurize the
headspace to insure that there are no leaks. The pres-
sure should not exceed 7 psig. The established pres-
sure should be maintained for at least four hours to
insure that all the seals are proper.
To remove a bolted-on manhole or handhole cover
1. Thoroughly clean the cover. Remove all dirt, grease and
moisture.
2. Relieve internal tank pressure by manually operating
the pressure relief valve.
3. Remove the hardware (3/8” inch nuts using a 9/16”
socket) which attaches the cover to the tank.
4. Gently pry the cover upward, making sure that the
cover gasket does not come in contact with the
transformer insulating liquid. Lift vertically to prevent
damage to cover, bolts, and tank gasket.
5. Remove the gasket sections from the manhole flange,
noting the location and orientation (up/down) of each
piece.
To reinstall the bolt-on manhole or handhole cover
1. Return the gasket sections to their original positions
and orientation.
2. Reinstall the manhole/handhole cover, using 25 ft-lbs.
torque to tighten the hardware. After installing all the
nuts, re-torque each nut to insure the proper torque is
achieved.
3. Remove the pressure relief valve and pressurize the
headspace to insure that there are no leaks. The pres-
sure should not exceed 7 psig. The established pres-
sure should be maintained for at least four hours to
insure that all the seals are proper.
4. Reinstall the access cover using 25 ft-lbs. torque to
tighten the access cover hardware.
WARNING
If the need arises to open a welded tank unit by cutting
welds, purge all gas space with nitrogen and keep
nitrogen flowing during cutting operations . Failure to do
so may cause gases to explode in the tank
.
13
SubStation tranSformer inStallation and partS replacement information
MN202002EN JUNE 2016