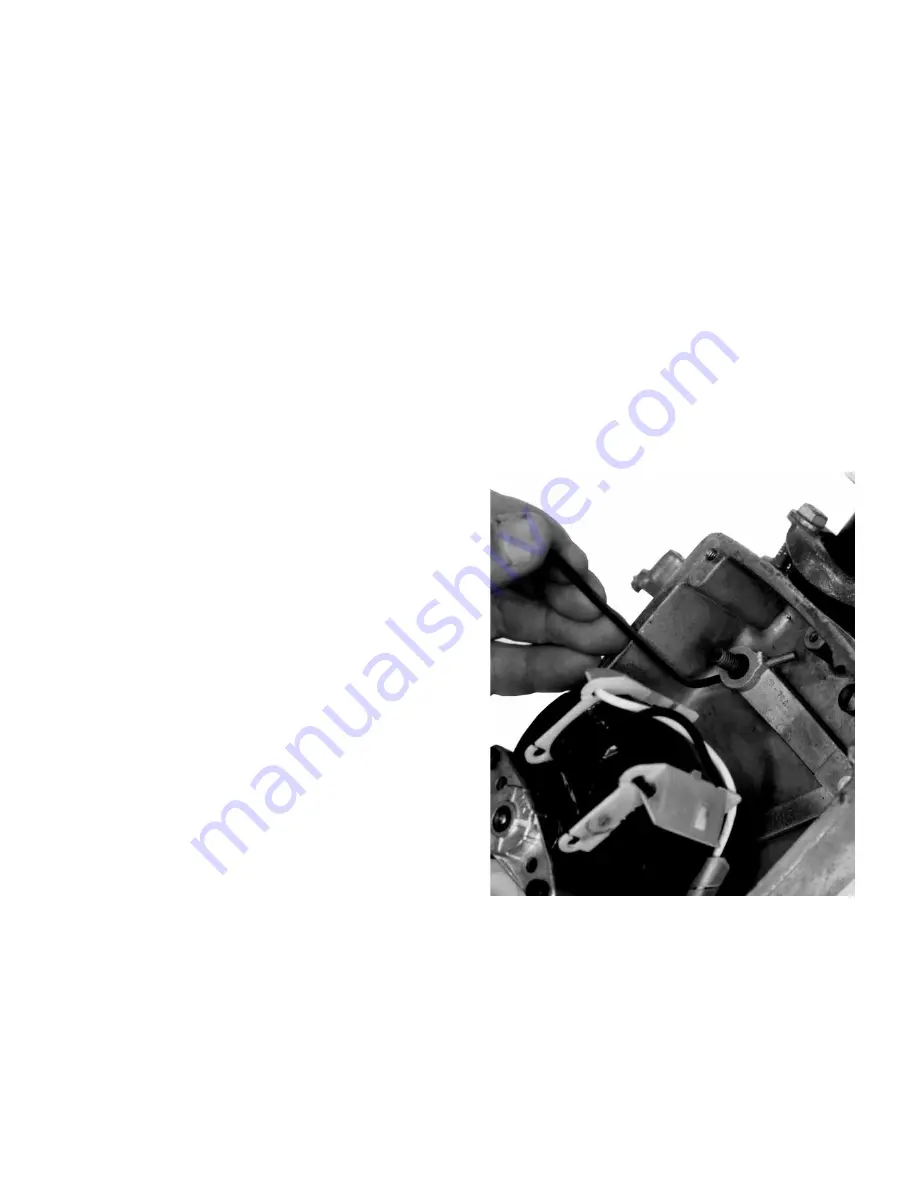
Actuator assembly replacement
To replace the actuator assembly proceed as follows:
1. Pull yellow handle down to open switch contacts.
2. Remove elastic stop nut, lockwasher and flatwasher
from operating shaft.
3. With a right angle punch or allen wrench force out
straight pin as shown in Figure 15.
4. Disconnect wire leads from terminal strip.
5. Remove four screws that secure actuator base plate to
housing. Carefully lift actuator assembly from housing,
pulling the drive lever straight from the operating shaft.
6. Place actuator assembly in mounting position and slip
drive lever over operating shaft. Loosely install the four
mounting screws that secure the base plate to the
housing.
7. Insert straight pin through drive lever and operating
shaft. Install flatwasher, lockwasher and elastic stop
nut. Tighten stop nut firmly to prevent straight pin from
backing out. Moderate force is sufficient to tighten stop
nut. Extreme force on nut can break straight pin.
8. Tighten four actuator assembly mounting screws.
9. Attach wire leads to terminal strip, as shown in Figure
12.
10. Operate the switch electrically and check for binding.
Check adjustment of selector switch (and holding
switch if equipped) as described in "Shop Repair
Procedures—Selector and Holding Switches" section.
Greasing recommendations
When a Type NR oil switch is removed from service, check
these points in the actuator for sufficient lubrication:
•
Spring anchor boss
•
Actuator drive lever spring anchor
•
Mechanism shaft through cam center
•
Pinion gear on motor shaft and mechanism gears
Apply “MOBILGREASE 28” or a similar low-temperature
grease to these areas. Well-lubricated mechanisms will
reduce subsequent wear and preserve smooth actuator
operation.
ote:
N
Grease need only be applied to these points when
the switch is removed from service. Do not remove
switch from service for sole purpose of applying
lubrication to the actuator mechanism.
Head mechanism
The head mechanism requires no periodic maintenance.
Observe the following procedure when disassembling the
head mechanism:
1. Remove the contact structure as described in "Shop
Repair Procedures—Complete Contact Box Assembly"
section.
2. Remove the bushings as described in "Shop Repair
Procedures—Bushings" section.
ote:
N
This step is not mandatory, but is suggested to
simplify working on the head mechanism if a service
rack is not available.
3. Perform Steps 1 and 2 in "Actuator Assembly" section
to free the actuator mechanism from the operating
shaft.
4. With a hammer and punch, drive out the roll pin that
secures the reset lever to the operating shaft (Figure
16).
5. Remove the sleet hood cover and slip the operating
handle spring from the reset lever. Slide out the
operating shaft.
6. Install new parts as required. Be sure roll pin that fixes
reset lever to operating shaft is driven in until 3/16-inch
of pin projects as shown in Figure 16.
Figure 15. Removing straight pin with allen wrench.
11
TYPE NR OIL SWITCH MAINTENANCE INSTRUCTIONS
MN230001EN February 2016