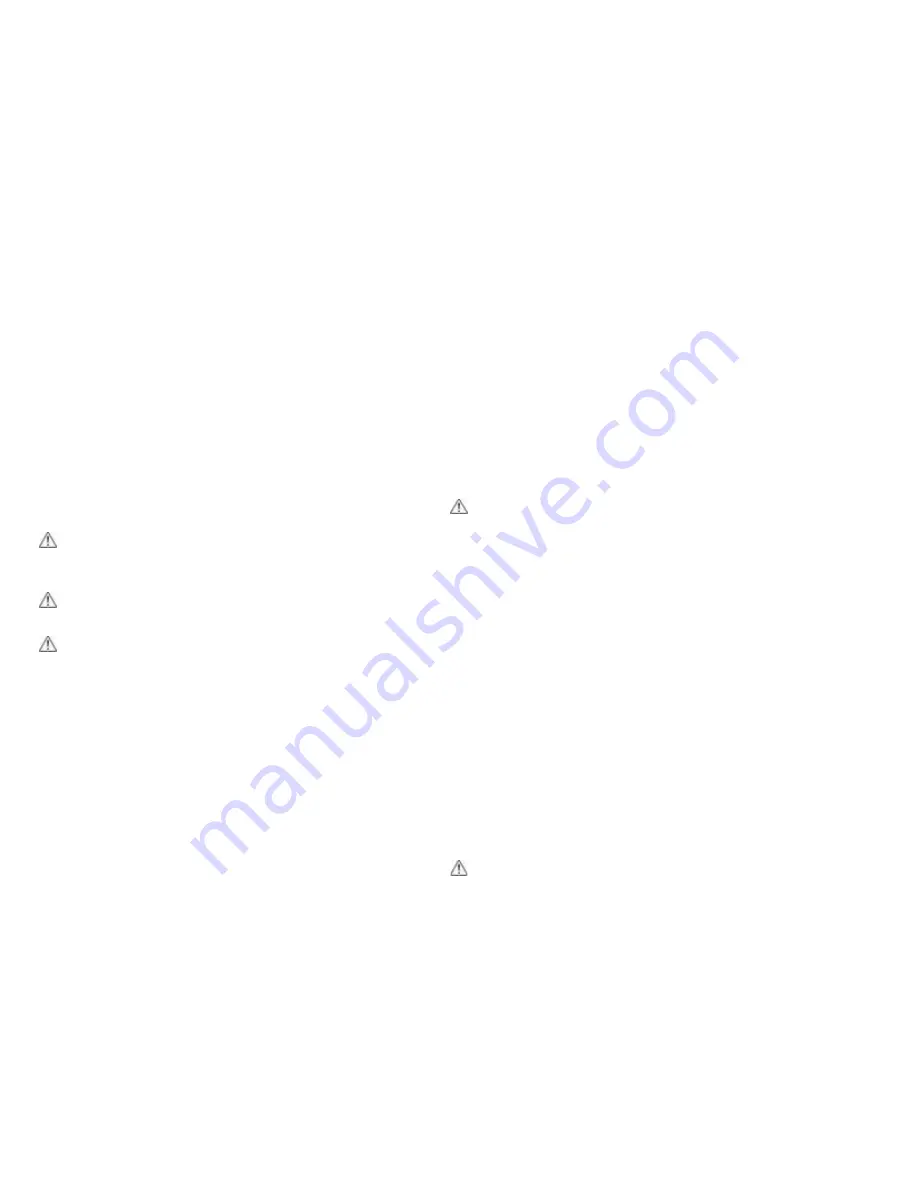
EATON Airflex WSB 11210 WCSB3 Installation Operation and Maintenance E-CLCL-11001-E October 2013
28
4.6.2 Mounting Flange/Cylinder Seals
Note: If the tensioner was completely removed and disassembled
to replace seals, refer to Section 4.9 to assemble.
4.6.2.1 Carefully examine the seal surfaces in the water
cooled cylinder or mounting flange/cylinder (112). If
the surfaces have worn to point as indicated on Table
13, the cylinder must be replaced. Small nicks or
scratches must be sanded smooth to prevent air
leakage.
4.6.2.2 Lubricate the seal surfaces in the mounting flange/
cylinder (112) with Molykote
®
O-ring lubricant and
carefully slide the cylinder onto the spring housing.
Take special care to avoid damaging the seal lips.
4.6.2.3 Attach the mounting flange /cylinder (112) to the
pressure plate (116) with the screws, washers
and spacer tubes removed in Section 4.6.1.1 Use
Loctite
®
LocQuic
®
Primer Grade “T” to clean and
prepare the screw threads and install with Loctite
®
#262. Using a crosswise pattern, torque the screws
to the value shown in Table 4.
Warning
Loctite
®
Primer “T” contains harmful vapors. Refer to
the product label for proper safety precautions.
Caution
Loctite
®
#262 must be shaken prior to application.
Caution
Loctite
®
#262 may irritate sensitive skin. Refer to the
product label for proper safety precautions.
4.6.2.4 If mounting flange cylinder seals (21), (23) and (114)
have been replaced, reassemble the tensioner/brake
per Section 4.9.
4.6.3 Install air lines and air test the assembly for seal
leakage per the following:
Apply 120 psi (8.2 bar) to an open port in the cylinder
(19) to disengage the spring-set brake and check for
release cylinder leakage. Apply 120 psi (8.2 bar) to
the outer port in the mounting flange cylinder (112)
and check for outer seal leakage. Allow the inner port
in the mounting flange cylinder (112) to remain open
to check for potential leakage from the outer cylinder
area to the inner cylinder area in the mounting flange
cylinder. Shut off the air supply and check for
pressure drop from the cylinders. If air pressure does
not drop below 100 psi (6.8 bar) within 10 minutes,
the seals have been properly installed.
Continue the test by releasing the air pressure in the
outer port in the mounting flange cylinder, and
applying 120 psi (8.2 bar) to the inner port in the
mounting flange (112). The outer port should remain
open to atmosphere. Apply 120 psi (8.2 bar) to the
cylinder (19) to disengage the spring set brake. Check
for leakage from the inner cylinder area to the outer
cylinder area in the mounting flange cylinder. Shut off
the air supply and check for pressure drop from the
cylinders. If air pressure does not drop below 100
psi (6.8 bar) within 10 minutes, the seals have been
properly installed.
4.7
Spring Replacement of outer & inner apply
springs (22) & (52) for Air Cooled Brake
4.7.1 Remove the tensioner as an assembly, and
disassemble per Section 4.3.
4.7.2 Match mark the cylinder (19), spring housing (16),
and pressure plate subassembly (13) to one another,
to ease reassembly.
4.7.3 With the cylinder (19) facing up, disassemble the
cylinder/spring housing subassembly by loosening
the hex head screws (20) ONE TURN AT A TIME,
following a crosswise sequence, until the spring force
is relieved. Remove the hex head screws and
washers.
Caution
Failure to loosen the screws (20) evenly and in small
increments as described may cause the screws or
cylinder to bind.
4.7.4 Lift and set aside the spring housing (16) and cylinder
(19) as a subassembly to expose the springs. Note
the locations of the springs and spring retainers (53)
- if applicable - for reassembly purposes. See Figure
1, Figure 1A and Figure 1B.
4.7.5 Inspect the springs for distortion by checking the
free height. If the free height of any spring is less
than the value shown on Table 13, the entire set of
springs must be replaced. Inspect the spring for
any surface fractures or high temperature color
change. Any conditions found require the entire set of
springs to be replaced.
4.7.6 Reassemble the tensioner by following the
procedures in Section 4.9, beginning with section
4.9.20.
Caution
The cylinder (19), spring housing (16) and end plate
(117) should not be re-assembled as a separate
subassembly. Improper assembly procedures may
result in uneven contact of the friction material with
the disc (119), resulting in low stopping torque.
4.8
Bushing Replacement
Note: The reaction plate (13), pressure plate (30) and end plate
(117) have bushings (54) installed in the reaction holes (Figure
14). The reaction plate, pressure plate and end plate bushings
are different lengths. Be sure to install the correct length bushing
in the proper component. Refer to the reaction plate, pressure
plate and end plate sub-assemblies in the parts list (Section 6)
for the selection of the proper replacement bushing. Replacement
of the bushings can be performed per the following procedures.
WCSB3 Brakes