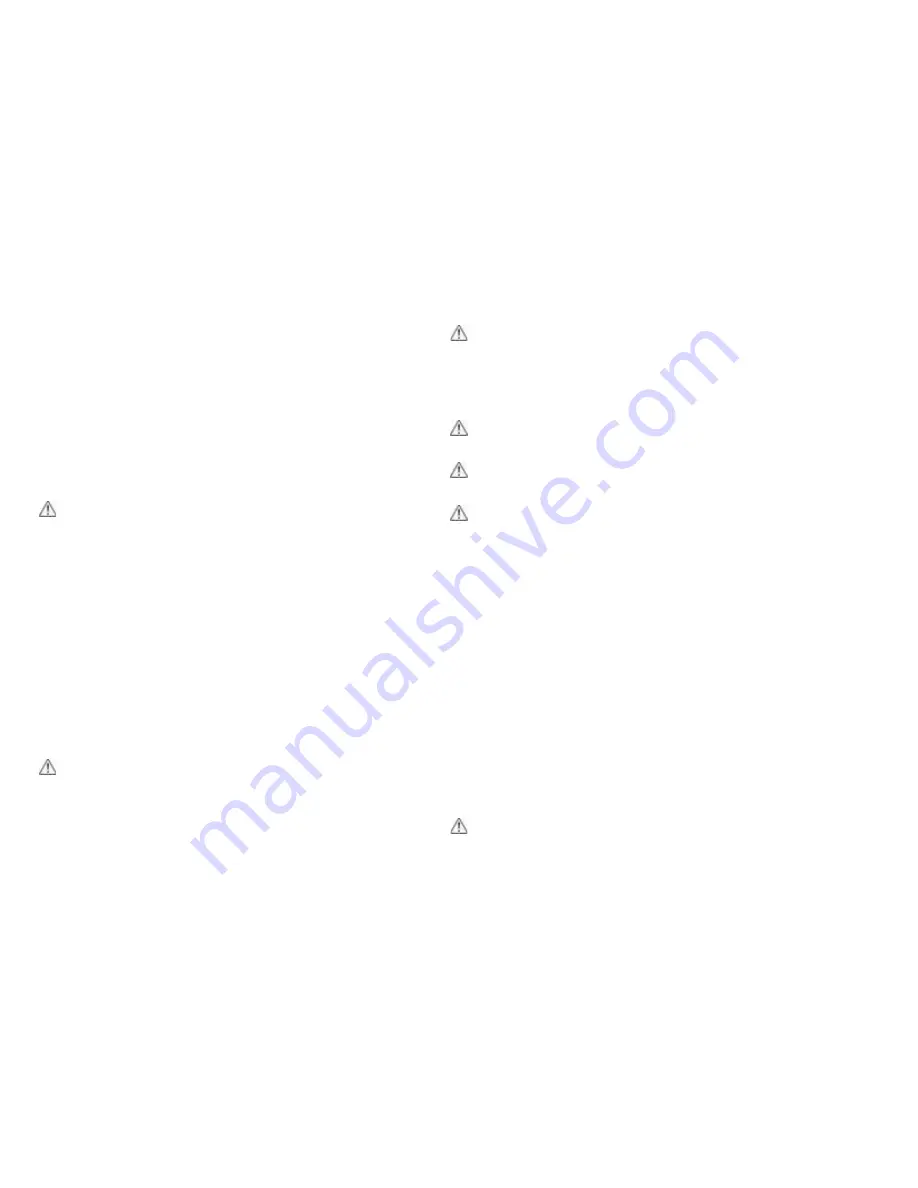
EATON Airflex WSB 11210 WCSB3 Installation Operation and Maintenance E-CLCL-11001-E October 2013
24
4.3.8 Lift the cylinder, spring housing, and pressure plate
off the studs as an assembly. Set the assembly aside
on a clean, level area, making sure to avoid damaging
the friction material surface.
4.3.9 Continue removing the remaining components if
required.
4.3.10 Inspect all components using the wear limits in Table
13 as a reference.
4.3.11 For friction lining replacement refer to Section 4.4.
4.3.12 For wear plate (3) replacement, refer to Section 4.5.
4.3.13 Refer to Section 4.6 to replace seals (21), (23) & (114)
for the mounting flange/cylinder (112) and seals (21)
& (23) for the brake cylinder (19).
4.3.14 For spring (34) replacement, refer to Section 4.7.
4.3.15 For bushing (54) replacement, refer to Section 4.8.
4.3.16 Assemble the tensioner per Section 4.9.
Caution
After replacement of friction material, a minimum
wear-in period is recommended for the friction couple
to achieve rated torque. See Section 3.3 for wear-in
procedures.
4.4
Friction Material Replacement
Note: When replacing friction material, it is recommended that
the mating wear surface be inspected for wear. A light touch up
of the wear surfaces may be performed to remove high spots or
burrs to minimize wear-in if required. See Table 13 for wear
limits.
4.4.1 Refer to Section 7.0 for the friction disc replacement
part numbers.
Caution
Use only genuine, Airflex friction material. Use of
material not of Airflex origin may result in unpredict-
able performance.
4.4.2 Disassemble the tensioner as per Section 4.3.
4.4.3 Remove the old screws and discard the old friction
material.
Note: Use of a pinpoint torch to heat the screws and soften the
Loctite
®
will ease removal of the screws.
4.4.4 Clean all burrs, corrosion etc. from the friction disc
core or mounting surfaces. Chase all tapped holes
with a tap to clean threads and remove any residual
Loctite.
4.4.5 Position the new friction material to align the
screw holes. Apply Loctite
®
#262 to the screw
threads and tighten the screws to the proper torque
value. For water-cooled disc assemblies, tighten
screws to 15 ft lb. (20Nm). Screws securing the
air cooled brake friction discs (118) or blocks mounted
on the pressure plate (13) and end plate subassembly
(117) should be tightened to 20 ft-lb (27 Nm) after
application of Loctite
®
#262 to the screw threads.
Install the screws in an even, crosswise pattern.
Screws in friction blocks should be installed from the
center most position in the block, then progressing
towards the outer edges of the block. One at a time,
install and torque each screw immediately after
application of Loctite
®
then proceed to the next
screw.
Warning
Loctite
®
may cure prior to properly tightening the
screw if not tightened to the proper torque value
immediately after installation.
Caution
Use only Airflex-supplied screws.
Caution
Loctite
®
#262 must be shaken prior to application.
Caution
Loctite
®
#262 may irritate sensitive skin. Refer to the
product label for proper safety precautions.
4.4.6 After replacement of friction material, assemble the
tensioner per Section 4.9. Observe wear-in
procedures during start-up per Section 3.0, Operation.
4.5
Wear Plate Replacement
Note: When replacing wear surfaces, it is recommended that the
mating friction material be replaced to ensure good contact
between the mating surfaces. See Table 13 for wear limits.
4.5.1 Disassemble the tensioner per Section 4.3.
4.5.2 Remove the screws (4) and locknuts (5) holding
the wear plates (3) and remove the wear plates. If the
wear plates cannot be easily lifted off, gently tap the
O.D. to break the gasket seal.
Caution
Do not attempt to break the gasket seal by prying be
tween the wear plate and housing. Damage to the
sealing surfaces may occur.
4.5.3 Internal Corrosion Protection
Note: Water-cooled tensioners used in both the open and closed
loop operating modes are required to be painted with Flame
Control TemperKote 1000 PRIMER and top coated with
TemperKote 1000 TOPCOAT.
4.5.3.1 Lifting off the wear plates (3) in section 4.5.2 will
expose the water passages. Inspect the water
passages and, if necessary, use a wire brush to clean
them. For best results, surfaces should be free from
oil, grease, dirt, mill scale, rust corrosion products,
oxides paint and foreign matter.
WCSB3 Brakes