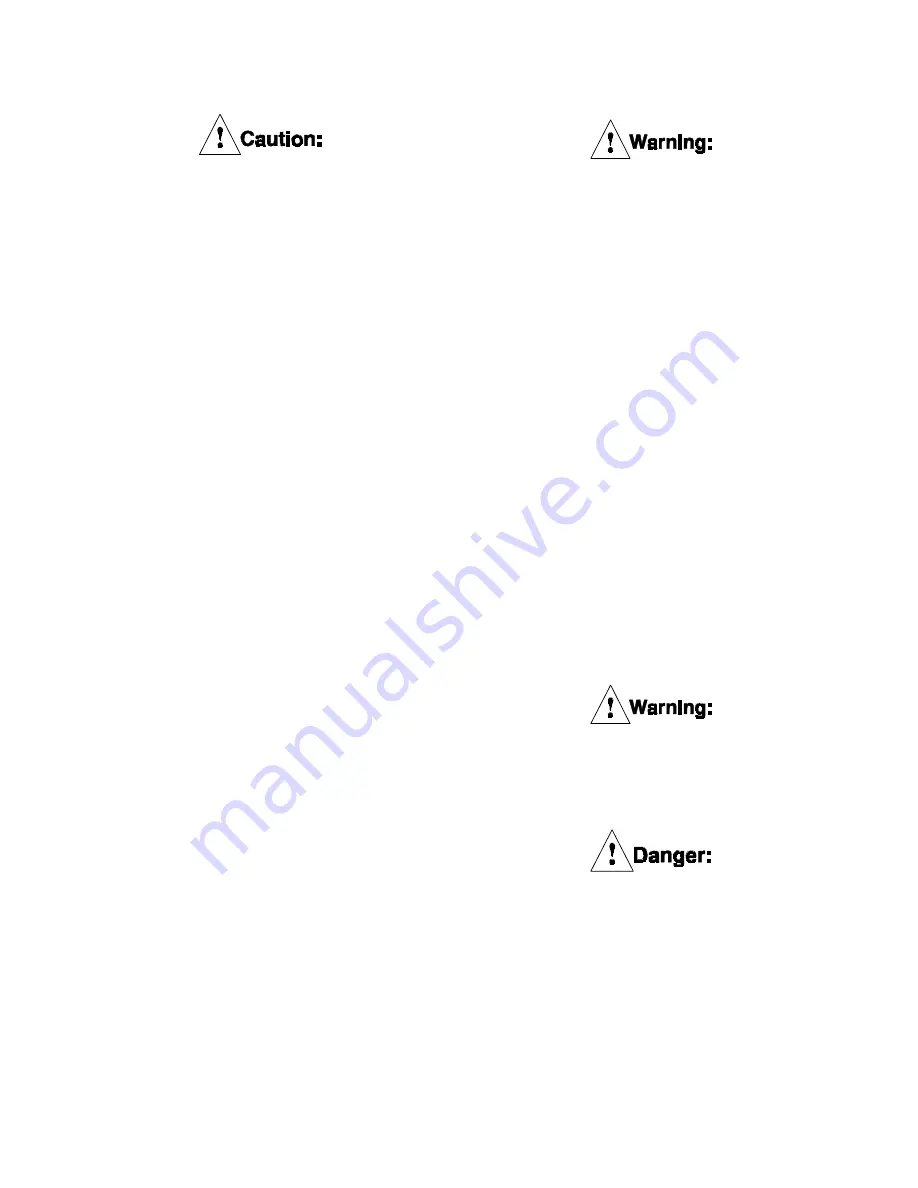
Excessive restriction of the brake
exhaust air will result in long stop-
ping times and inconsistent stop-
ping position.
3.2.3
If the DBB brake is used in combination with
a clutch, clutch/brake overlap may occur
which will result in excessive heat generation
and motor overload. Overlap may be
detected by monitoring the drive motor
current at the beginning and end of each
machine cycle. A current surge at the begin-
ning of the cycle usually indicates clutch
overlap which can be corrected by restricting
the air flow to the clutch or increasing the air
pressure to the brake. A current surge at the
end of the machine cycle usually indicates
brake overlap which can be corrected by
installing and adjusting a flow control valve
in the brake air supply line, as indicated in
3.2.2.
3.3
Periodic Inspection
3.3.1
As the friction material wears, the brake
torque will be reduced somewhat and
adjustment of the stopping position controls
(flow control or limit switch) will be neces-
sary. See table 4 for the friction material
wear limit.
3.3.2
Periodically check for air leakage in the area
of the cylinder seals (21,23). For
replacement, refer to the MAINTENANCE
section.
3.3.3
Periodically observe the friction disc
assembly(s) with the brake released.
Dragging friction discs may be caused by
wear or contamination at the gear/ring gear
contact areas.
3.3.4
Pneumatic and electrical control interlocks
should be periodically checked for correct
settings and operation.
3.3.5
Inspect for need for wear adjustment.
Refer to Section 4.2.
4.0
MAINTENANCE
Prior to performing any mainte-
nance on the DBB brake, make sure
the equipment is in, and will remain
in, a safe condition.
4.1
Wear Limits
4.1.1
Wear limits for the DBB components are
shown on Table 4. If any wear limit has been
reached or exceeded, that component must
be repaired or replaced.
4.2
Wear Adjustment & Disassembly
4.2.1
On both single and dual disc units, the
friction material must be replaced when worn
to the bottom of the groove on the friction
lining. See Figure 5. A wear adjustment is
required when the friction material is approxi-
mately one-half worn. To determine when
adjustment is required, measure the gap
between the spring housing (16) and the
pressure plate (13) with the brake engaged,
as shown on Figure 6. When this dimension
is .50" (12.7 mm) or greater, AND none of
the friction discs are worn to the bottom of
the wear groove, adjust per the following
procedure.
If a wear adjustment is not made,
the brake torque may deteriorate to
the point where the equipment will
not stop properly.
The Locknuts (18) must NOT be loos-
ened Unless air pressure is applied
tomrelieve spring pressure.
4.2.2
With 120 psi applied to the cylinder (19),
loosen and remove the locknuts (18) and
washers (17). Exhaust the air pressure.
NOTE: The socket size for locknuts (18) is
1 1/16" x 4" deep socket.
DBB 8104 PDF format
6
© Copyright Eaton Corp., 1998. All rights reserved.
(Revised: January, 1998)