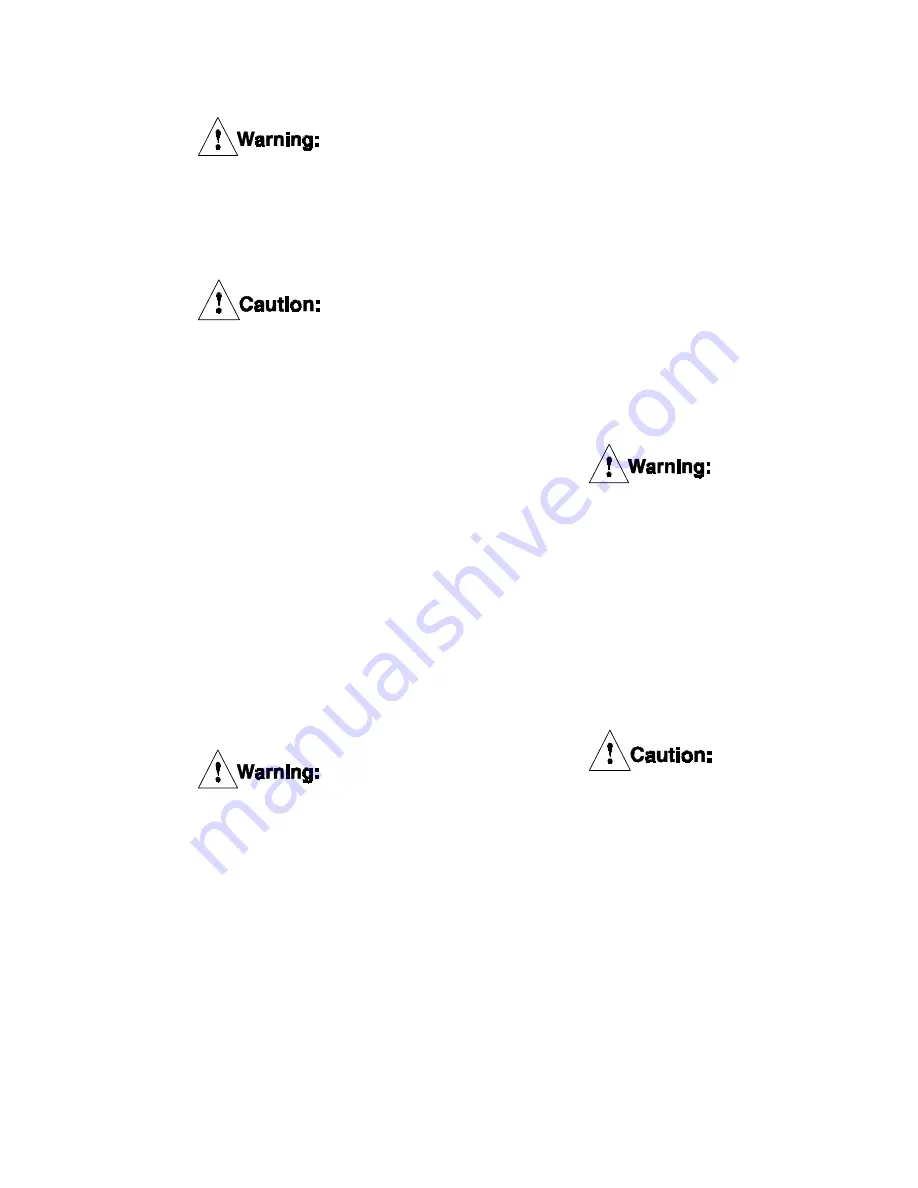
2.3
Air Supply System
Maximum allowable air pressure is
120 psig (8.2 bar). Operation of the
DBB at pressures exceeding 120
psig may result in damage to the
brake components.
Minimum releasing pressure for low
pressure brakes is 60 psig (4.1 bar)
and for high pressure brakes is 90
psig (6.1 bar). Operation at pres-
sures below minimum will result in
brake drag and excessive heat and
wear.
2.3.1
Since the air control arrangement will vary
from one application to the next, a specific
description cannot be presented here.
Following are some general guidelines for
installing the air control components.
2.3.1.1
Use full size piping consistent with the
control valve.
2.3.1.2
Keep the number of elbows to a minimum to
ensure consistent brake response.
2.3.1.3
Spool type solenoid valves are not
recommended. Use poppet type valves and
locate as close as possible to the brake.
If the DBB brake is being used on a
mechanical power press, special
valving may be required.
2.3.1.4
If the DBB brake is being used on a cyclic
application, an air receiver tank should be
installed in the air supply line and isolated
(check valve) from other air consuming
equipment.
2.3.1.5
The final connection to the brake inlet ports
must be made with flexible hose.
2.3.1.6
The DBB brake does not require lubricated
air; however the solenoid valve may.
Consult the valve manufacturer.
2.3.1.7
A pressure switch should be located in
the air supply line to the brake and
interlocked with the equipment electrical
controls.
3.0
OPERATION
3.1
Pressure and Speed Limits
3.1.1
Maximum applied pressure is 120 psig (8.2
bar). Minimum releasing pressure for low
pressure brakes is 60 PSIG (4.1 bar).
Minimum releasing pressure for high
pressure brakes is 90 psig (6.1 bar).
3.1.2
Maximum disc speed is 1800 RPM.
Operation at disc speeds exceeding
the maximum allowable, as shown
on Table 6, may result in exposure
to personal injury or product/equip-
ment damage.
3.2
Initial Operation
3.2.1
The non-asbestos friction material used on
DBB brakes may not develop rated torque,
as a short wear in period is required.
The non-asbestos friction material
used on Airflex DBB brakes may not
develop rated torque initially, as a
short wear in period is required.
Machine operation should therefore
be monitored closely until the
friction material wears in.
3.2.2
If the brake engagement appears harsh, a
flow control valve may be installed in the
brake air supply line. When using a flow
control valve, install so free flow is to the
brake and restricted flow is away from the
brake.
DBB 8104 PDF format
5
© Copyright Eaton Corp., 1998. All rights reserved.
(Revised: January, 1998)