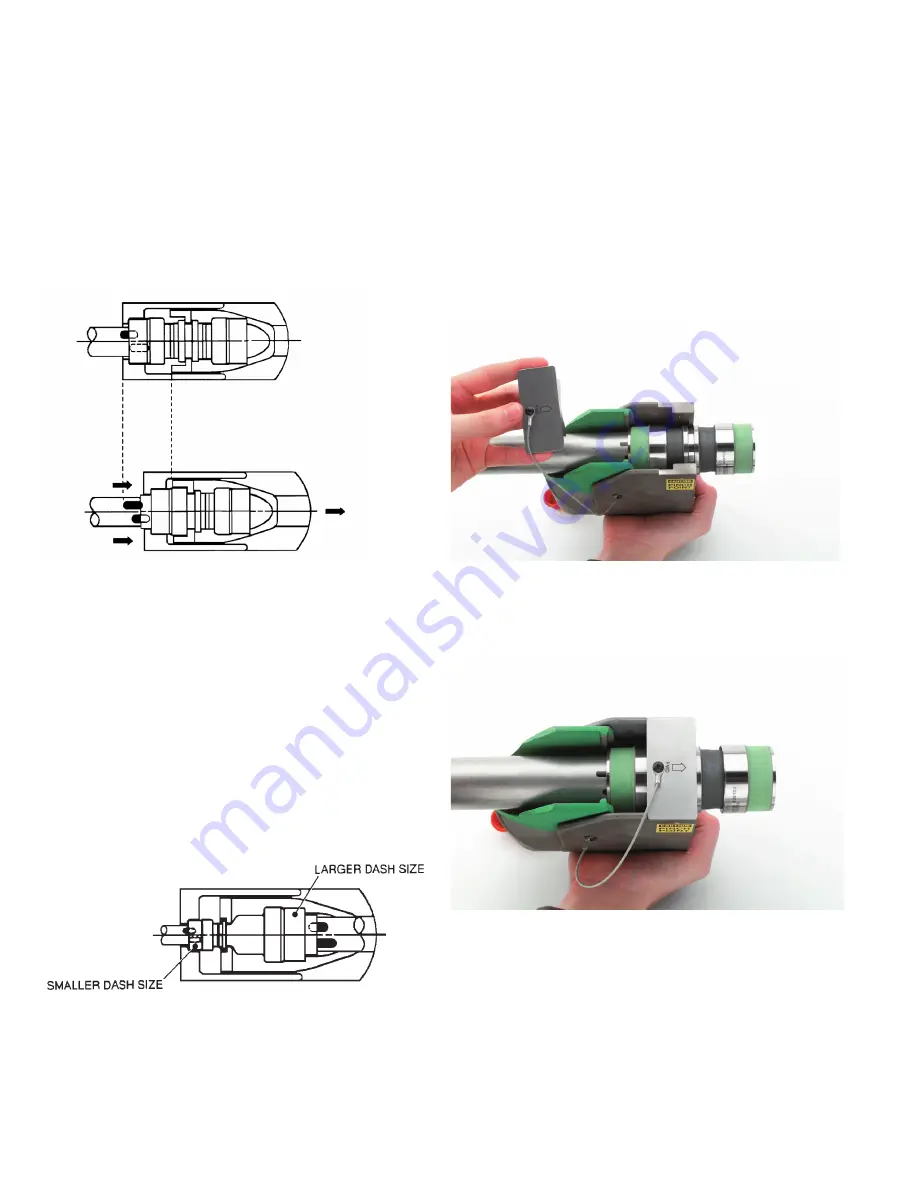
8
EATON
Aerospace Group
TF100-67A March 2013
Rynglok Fitting System Installation Guide
6.0
Special Consideration
6.1
Using the “Reversed Tool”
When using the RTST(X)R-01-SIZE “Reversed Tool”, care must be
taken in positioning the tool properly onto the fitting and in position-
ing the fitting onto the tube because of the relative movement of
the movable tool jaw. See Figure 12. The “Reversed Tool” is used in
situations where an installation is required at or near a bulkhead or
an adjacent fitting or structural member where the “Standard Tool”
does not fit. This tool allows the installer the opportunity to swage
the fitting end as close as possible to adjacent members.
Figure 12
Tool position before advancing the ring (note
tool/tool jaw/fitting position)
Tool position after advancing the ring
Caution:
Note relative movement of the whole tool with respect to
the fitting.
6.2
Special Consideration When Using The “Reversed Tool”
When using the “Reversed Tool” with reducer/expander fittings, a
special RTST(X)R-51-SIZE “Reversed Tool” is required. The standard
“Reversed Tool” is to be used with standard non-reducer/expander
fitting configurations, while the special “Reversed Tool” is intended
to be used where there is an opposite fitting end or forging body
size greater than the dash size of the fitting end being swaged, as
shown in Figure 13. These special “Reversed Tools” will be marked
with a colored band and the required swage pressures identified on
the tool body.
Warning:
The swage pressures listed on the special “Reversed
Tools” must be strictly adhered to, in order to prevent excessive
tonnage applied to the fitting which may result in a damaged fitting
or fitting failure.
6.3
Special Considerations When Using the -20 and -24 Tools
When using the size -20 and -24 standard and reversed swage tools,
a swage bridge attachment is used in conjunction with the standard
hand swage tool, see Figures 14A and 14B. The swage bridge is
to be oriented and bottomed into the swage tool detents after the
insertion of the fitting. The swaging operation shall then proceed
as normal. For the standard hand swage tool, the swage bridge is
inserted into the movable jaw.
Note:
The swage bridge is connected
to the hand swage tool via a flexible lanyard and should not be
separated. Proper orientation is noted by the “Front” arrow stamped
on top of the swage bridge and by “click” of the detents when the
swage bridge is sitting flush on the reliefs on top of the swage tool.
Figure 14A
Swage bridge prior to placement
Figure 14B
Correct placement of swage bridge on tool
Figure 13
Using the special “Reversed Tool”