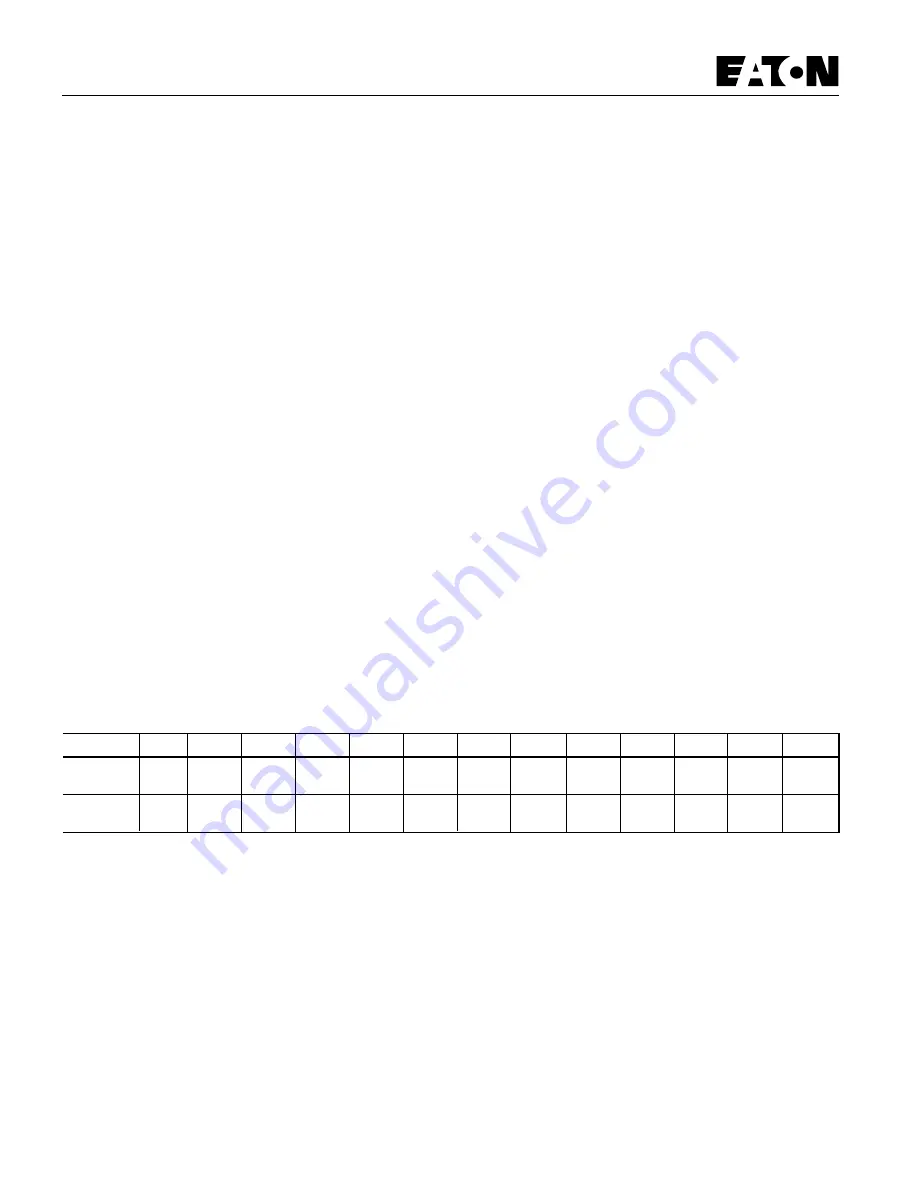
10
Series 26 - Model 26000 Multiple Gear Pump
Minimum Gear Width per Displacement
Model Number
26001
26002
26003
26004
26005
26006
26007
26008
26009
26010
26011
26012
26013
Pump Disp.
6,6
8,2
9,5
10,8
13,8
16,7
19,7
22,5
24,3
25,2
27,7
29,0
30,6
cm
3
/r [in
3
/r]
[.40]
[.50]
[.58]
[.66]
[.84]
[1.02]
[1.20]
[1.37]
[1.48]
[1.54]
[1.69]
[1.77]
[1.87]
Gear Width
7,85
9,75
11,20
12,95
16,15
19,35
22,56
25,76
28,12
28,96
32,16
33,78
35,36
mm [in]
[.309]
[.384]
[.441]
[.510]
[.636]
[.762]
[.888]
[1.014]
[1.107]
[1.140]
[1.266]
[1.330]
[1.392]
Inspection
Front plate and Backplate Inspection
1
Oil groove in bushings in front plate should be in line with
dowel pin holes and 180
°
apart. The oil grooves in the
backplate bushings should be at approximately 37
°
to the
pressure side.
2
Replace the backplate, adapter plate or front plate if I.D. of
bushings exceed 19,2 mm [.755 in] (Bushings are not available
as separate items).
3
Bushings in front plate should be at 3,20 mm [.126 in]
above surface of front plate.
4
Bushings in adapter plate on the wear plate side should be
at 3,20 mm [.126 in] above surface of adapter.
5
Check for scoring on face of backplate orbackplate side of
adapter plate. Replace if wear exceeds ,038 mm [.0015 in.].
Body Inspection
1
Check body inside gear pockets for excessive scoring or
wear.
2
Replace body if I.D. of gear pockets exceeds 43,7 mm
[1.719 in].
Inspect Parts for Wear
General
1
Clean and dry all parts.
2
Remove all nicks and burrs from all parts with emery
cloth.
Gear Assembly Inspection
1
Check spline drive shaft for twisted or broken teeth or
check keyed drive shaft for broken or chipped keyway.
2
Inspect both the drive gear and idler gear shafts at
bushing points and seal area for rough surfaces and excessive
wear.
3
Replace gear assembly if shaft measures less than 19 mm
[ .748 in] in bushing area. (One gear assembly may be replaced
separately; shafts and gears are available as assemblies only.)
4
Inspect gear for scoring and excessive wear.
5
Replace gear assembly if gear width is below the following
dimensions. Refer to chart on this page.
6
Assure that snap rings are in grooves on either side of
drive and idler gears.
7
If edge of gear teeth are sharp, break edge with emery
cloth or stone.