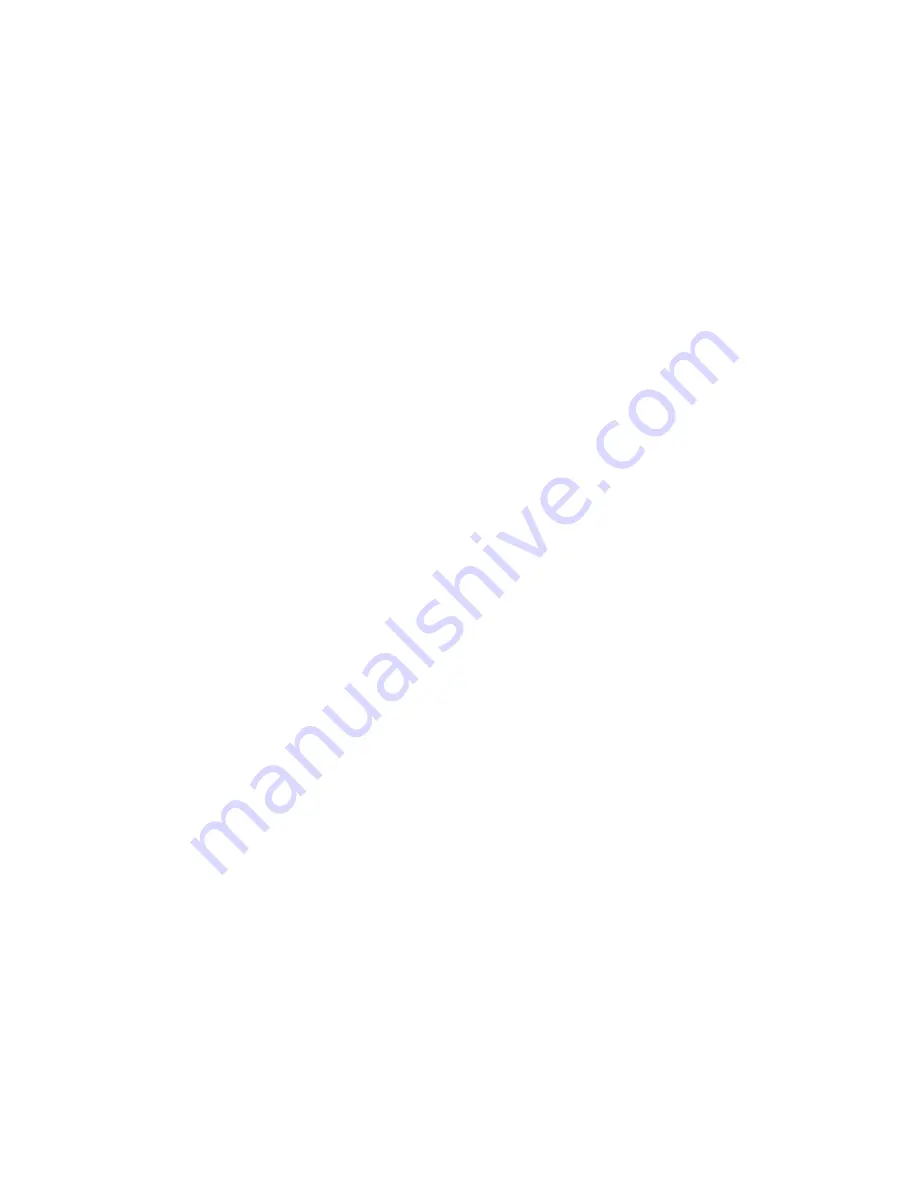
30
EATON
Series 1 Heavy Duty Hydrostatic Fixed Displacement Motors Parts and Repair E-MOPI-TS002-E September 2004
Hydraulic Fluid
Recommendations
The ability of Eaton hydrostatic components to provide the desired performance and life expectancy depends large-
ly on the fluid used. One of the most important characteristics to consider when choosing a fluid to be used in a
hydraulic system is viscosity. Viscosity choice is always a compromise; the fluid must be thin enough to flow easily
but thick enough to seal and maintain a lubricating film between bearing and sealing surfaces. Viscosity
requirements are specified later in this document.
Fluid temperature affects viscosity. In general, as the fluid warms it gets thinner and viscosity decreases. The
opposite is true when fluid cools.
When choosing a fluid, consider the start-up and operating temperatures of the hydrostatic system. Generally, the
fluid is thick when the hydraulic system is started. With movement, the fluid warms to a point where the cooling
system begins to operate. From then on, the fluid is maintained at the temperature for which the hydrostatic
system was designed.
In actual applications this sequence varies; hydrostatic systems are used in many environments from very cold
to very hot. Cooling systems also vary from very elaborate to very simple, so ambient temperature may affect
operating temperature
Introduction
Viscosity and
Temperature
Cleanliness of the fluid is extremely important. Eaton recommends that the fluid used in its hydrostatic components
be maintained at ISO Cleanliness Code 18/13 per SAE J1165. The code allows a maximum of 2500 particles per
milliliter greater than 5µm and a maximum of 80 particles per milliliter greater than 15µm. When components with
different cleanliness requirements are used in the same system, the cleanest standard should be applied.
A reputable filter supplier can supply filter information.
Cleanliness
Maintaining correct fluid viscosity and cleanliness level is essential for all hydrostatic systems. Field testing and
monitoring are the only ways to get accurate measurements of system cleanliness. Test and establish fluid
maintenance schedules designed to meet the viscosity and cleanliness requirements.
Fluid Maintenance
Premium grade petroleum based hydraulic fluids will provide the best performance. These fluids typically contain
additives that are beneficial. Eaton recommends fluids that contain anti-wear agents, rust inhibitors, anti-foaming
agents, and oxidation inhibitors. Premium grade petroleum-based hydraulic fluids carry an ISO VG rating.
SAE grade crankcase oils may be used, but it should be noted that these oils may not contain all of the
recommended additives. Using crankcase oils may increase fluid maintenance requirements.
Hydraulic fluids that contain V.I. (viscosity index) improvers, sometimes called multi-viscosity oils, may be used.
These V.I.-improved fluids are known to “shear-down” with use. Their actual viscosity drops below the rated value.
Fluid maintenance must be increased if V.I.-improved fluids are used. Automotive automatic transmission fluids
contain V.I. improvers.
Synthetic fluids may be used. A reputable fluid supplier can provide information on synthetic fluids.
Review applications that require the use of synthetic fluids with your Eaton representative.
Fluid Selection